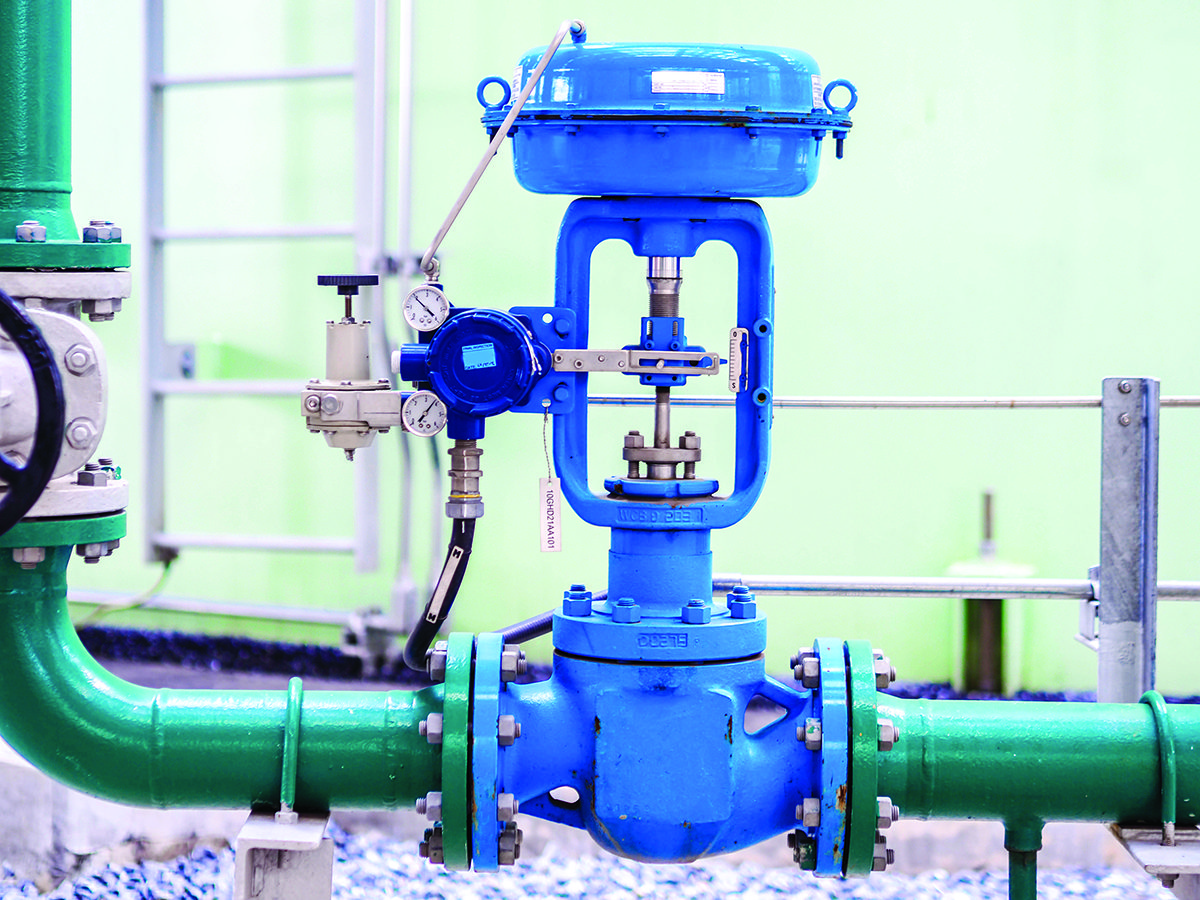
By Al Gunnarson, VP of Sales and Marketing, Warren Controls.
The advent of online sizing and selection tools has transformed the process of selecting valves, providing a more efficient and accurate way to determine the best valve for each application. These tools consider varying flow requirements, pressure differentials, and fluid compatibility across different applications within a facility.
Choosing an unsuitable process control valve can result in serious control issues, and lead to premature failure and costly downtime. The consequences include not only increased maintenance costs but also the potential for safety hazards and reduced system reliability.
An unsuitable valve can fail to regulate flow properly, causing pressure surges or water hammer effects that can damage the piping system, leading to further leaks or catastrophic failures. These events not only increase the risk to personnel safety but also amplify the financial burden on the organization due to emergency shutdowns, increased maintenance requirements, and the need for replacement parts.
Choosing valves without using online tools
Before the advent of these online tools, choosing the right valve for a specific application relied heavily on complex differential equations and extensive engineering know-how based on the ISA (International Society of Automation) standards. This method, while precise, was incredibly arduous and error-prone, typically requiring upwards of 45 minutes for each process control valve to determine the correct specifications. Few were skilled or patient enough in the required math to achieve the necessary accurate results. Even when this is accomplished, selecting the correct complete P/N from a manufacturer, and gathering all this into a comprehensive report to present to a customer is another huge drain on time.
Given the complexity and time constraints faced by engineers and specifiers who don’t use online tools, there is too often a tendency to bypass these detailed calculations in favor of educated guesses or approximations.
In a typical scenario where a facility requires 30 process valves, all ostensibly needing to be 4 inches, a specifier might opt to select 30 of the same 4-inch valves rather than doing the arduous calculations to select different valves optimized for each particular application.
This one-size-fits-all approach often results in some valves being oversized or undersized for their specific tasks, resulting in higher initial costs for unnecessary capabilities or future costs due to premature wear, maintenance issues, and even system failures and safety and environmental hazards.
Importance of proper valve selection
Preventing cavitation damage is crucial. Certain valve types are prone to cavitation when exposed to higher flowing differential pressures, while others are not. Cavitation involves the formation and subsequent collapse of vapor bubbles within a liquid, inflicting severe damage to the valve. Such conditions can lead to valve failure in just a few weeks.
The consequences of cavitation go beyond damage to the valve itself; it can also cause leaks that pose safety and environmental hazards, alongside the direct and indirect costs associated with valve failure and replacement.
Vibration is a critical factor to consider, as aerodynamic noise can reach up to 120 decibels. High aerodynamic noise levels tend to occur in conjunction with higher flow rates and higher flowing differential pressures which often necessitate the use of sound insulation blankets or other sound-deadening techniques like silencers. Moreover, excessive vibration can damage the valve, leading to premature wear and failure. In some cases, one or more valves in series, sharing the pressure drops can be more cost-effective than a single valve with expensive, aerodynamic noise tuning trim.
Selecting the appropriate trim material for valves is crucial, especially in applications involving higher flowing differential pressures. Often, there is a lack of awareness regarding the impact of differential pressure on trim material selection. The reality is that the higher the flowing differential pressure, the more durable the trim material needs to be. This ensures that the valve trim can withstand the conditions and remain functional over an extended period.
Temperature is also crucial in valve selection, especially for processes above 450°F (about 232ºC). Materials like engineered plastics or elastomers, which don’t withstand these temperatures, limit choices. Selecting valves that can handle high temperatures without degrading is essential for maintaining process integrity and safety.
The actuator is as important as the valve
Choosing the correct actuator to pair with a valve is just as critical as selecting the valve itself. An actuator, responsible for the mechanical operation of opening and closing the valve, must be robust enough to operate reliably under the specific conditions of its environment.
If an actuator fails to actuate the valve when required, serious consequences can follow. This may lead to situations where critical flows are not properly regulated or the valve does not shut off properly to the advertised leakage rating of the valve, resulting in overpressure or overtemperature incidents, uncontrolled chemical reactions, or significant leaks.
Leveraging online tools
Online tools like ValveWorks® mitigate these risks by offering a precise, scientifically-based process that considers all relevant factors of the valve’s intended use. By inputting specific process conditions — such as fluid type, temperature, pressure, and flow requirements — users can leverage advanced algorithms to identify a range of suitable options.
This not only saves time and reduces efforts in the specification process but also enhances safety and reliability by ensuring compatibility with the application’s demands. Furthermore, these tools provide in-depth analysis of the trade-offs between different options, equipping users with comprehensive documentation. This documentation facilitates clearer communication and efficient record-keeping and streamlines the procurement process, making it easier to make informed decisions.
Online tools for selecting process control valves are a critical advance. professionals can avoid the twin pitfalls of over-engineering and under-specification, ensuring that their facilities operate smoothly, efficiently, and cost-effectively.