A growing number of projects are successfully upgrading biogas for injection into the gas grid. Envirotec spoke to upgrader providers and plant managers to get a sense of the obstacles and opportunities in this new field
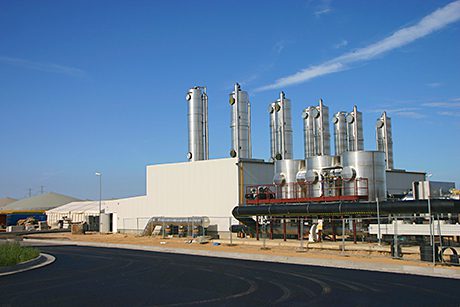
Germany
GIVEN its relative efficiency compared to using biogas for electricity generation, the idea of converting biogas for injection into the gas grid has long appeared commercially attractive.
The delivery of power to the end user by this method is more efficient than using biogas to generate electricity: Typical energy losses in natural gas transmission systems range from 1–2%, whereas the current energy losses on a large electrical system range from 5–8%.
In principle, it’s a relatively straightforward idea: the anaerobic digestion of organic material – much of it waste material that might otherwise have to be disposed of via landfill – produces methane, in addition to a little carbon dioxide and other gases. The technical problems involved in cleaning this gas to meet the requirements of the national gas grid have long been solved, although there are competing approaches with respect to how this cleaning is carried out.
According to the EU-funded GreenGasGrids project (www.greengasgrids.eu), the take-off of biogas-to-grid projects is being held back by a lack of cooperation between stakeholders, in addition to cross-trade barriers. According to John Bass of Chesterfield Biogas, a Sheffield-based provider of the ‘upgrader’ technology for converting biogas for the grid, there are complexities to address with respect to ensuring grid operators are supplied with the correct gas content, particularly in terms of the allowable oxygen content. In the UK a 1% oxygen requirement has been agreed upon, more stringent than many other countries, he says, where the requirement can be up to 3%.
Contractual headaches
Contracts with gas grid companies also take a great deal of sorting out in terms of flow rates and other aspects of infrastructure, it seems, the details of which will depend to some extent on how close the grid is to the site producing the gas. Bass points to recent clarification in the UK with respect to the tariffs paid to those producing biogas for the grid, another piece of the commercial jigsaw puzzle that he suggests has been very important to get in place.
Didcot Sewage Works in October 2010 became the first AD plant in the UK to supply biomethane gas to the national grid, for use in up to 200 homes in Oxfordshire. Others soon followed, including Adnam’s Bio Energy’s facility, which is based alongside the Adnam’s brewery in Southwold.
JV Energen produces biomethane for the grid from its site on the Duchy of Cornwall’s estate in Poundbury near Dorchester, using unwanted crops and factory food waste. According to the company’s Nick Finding, they started digging in June 2011, were building the plant in October of the same year and by March 2012 were generating electricity. Now they are putting this gas into the grid, a joint project between the company and its partners Scotia Gas Networks, Heat and Power Services, and DMT. It’s a project for which all four companies were joint recipient of an award this year from the AD & Biogas Association, in the category “Making the best use of biogas”.
A key technological ingredient in biogas-to-grid projects is the method used to upgrade the gas mixture – generally around 65% biomethane – to the 98%+ methane content required for the grid.
Sheffield-based Chesterfield Biogas has recently secured contracts to supply its ‘Totara’ upgraders to ReFood, the bioenergy arm of the PDM Group, for food waste processing at its site in Widnes. ReFood already has a waste processing facility in Doncaster, producing gas from food waste, which is then used to generate electricity.
“We have been given to understand that our UK presence and the long-term support we offer were significant factors in CBG being awarded this contract”, said md Stephen McCulloch.
One key aspect of Chesterfield’s upgrader technology is its use of water-wash technology, now widely regarded as the best solution for larger biogas-producing facilities, says Bass. The water-scrubbing method for the Totara upgraders is supplied by Chesterfield’s partner Greenlane®, a scrubbing technology it says is deployed at over 70 sites worldwide. It requires no heat or chemicals to operate, and can run purely on water, much of which can be recycled.
JV Energen opted against the use of water-washing for its upgrader facility, instead using a multi-membrane system. Nick Finding from the company says this was to some extent a constraint of the fact that the site on which they were choosing to build was one of outstanding natural beauty, and so they would have faced a lot of planning complexities in gaining permission for a structure that might be several metres high (see image, above).
Such strict planning permission requirements appear to be somewhat rare, says Bass, who says that the use of a water-wash upgrader in this situation could also possibly be accomplished by digging a hole and carrying out some landscaping work. In any event he suggests that the competing technologies of membrane and biological technology – the latter of which has been little adopted in the UK to date – would have a hard job justifying claims that they are greener or more widely adopted than water washing upgraders.
One way in which biogas projects have apparently become simpler in recent years is at a construction level. CBG’s upgraders are said to be “modular”, requiring “very little civil engineering”. Time will tell if the efforts of such developers is to bear fruit in the UK. But if Bass is typical, they now feel the regulatory pieces are in place to give this technology momentum.