A range of turnkey, modular AD systems from SEaB Energy is claimed to lower the barriers to entry for small businesses and farmers who want to dispose of waste in this way. Autodesk explains how its 3D design software played an important role in the product’s development.
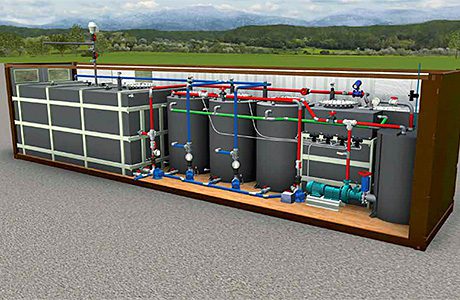
AD systems tend to be prohibitively expensive for most small farms and businesses and require trained engineers to operate. “We set out to create a self-contained, turnkey unit that delivered the benefits of a larger system without the drawbacks,” says Sandra Sassow, the CEO of SEaB.
Their ideal system, they reasoned, would offer a reasonable payback period, incorporate commonly available parts, and convert between 200 and 1,000 U.S. gallons of stable waste per day into renewable electricity.
Containment first
To protect the complex system—as well as enhance its visual appeal—the Sassows planned to enclose it within a shipping container. “No one had ever done that before, so we were basically starting from scratch.”
To create the 3D production model from the prototype, Paul Hackett, production and engineering manager at SEaB Energy, used software obtained through SEaB’s membership in the Autodesk® Clean Tech Partner Program.
SEaB used Autodesk Inventor software, part of the Autodesk Product Design Suite Ultimate, to envision and refine multiple design scenarios. “There are great advantages to designing in 3D with Autodesk Inventor as opposed to working with a physical prototype,” says Hackett. “Inventor and our digital prototype helped us pack us much as possible into a very confined space and cut six months off of the development cycle for four engineers.”
For help simulating system performance, SEaB has begun to use the finite element analysis and fluid dynamics simulation tools integrated in Product Design Suite Ultimate. “We used the fluid dynamics tools to simulate the mixing tanks and determine if the pasteurization process would work,” says Nick. This allowed him to validate the design on screen and avoid time-consuming and costly design changes in the confined space of the shipping container.
SEaB used Autodesk Vault data management software for version control.
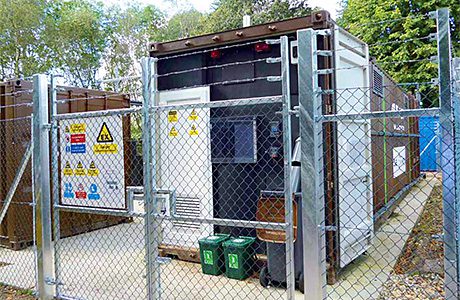
The result
SEaB has three active pilot installations and is ready to implement a full commercial model. “We use 3D design tools for all of our design work,” says Sandra. “We could not design and assemble the units without having in-house 3D graphics capabilities.”
SEaB’s success has not gone unnoticed. In 2012, SEaB was identified by the sustainability initiative LAUNCH: Beyond Waste as one of nine game-changing global waste technologies. “This technology could change the way we manage waste,” says Sandra. “You can take these units anywhere in the world, places where a much larger and costlier system is not feasible, and convert local sewage or food waste into as much as 65 kWh of green electricity—enough to power 25 average California homes or 650 average African houses.” Such systems could bring safe, clean, renewable electricity to some of the most remote areas of the world, while virtually eliminating the costs, fuel consumption, and GHG emissions associated with waste transport.
As it grows, SEaB plans to expand its use of Autodesk, including Autodesk SIM 360, which it currently uses to run multiple simulation studies in the cloud simultaneously. “That helps us avoid chewing up our local resources and gets us the answers we need in a short, concise time,” says Sandra. SEaB plans on adding Autodesk PLM 360 for full lifecycle management after it completes its implementation of Vault software.