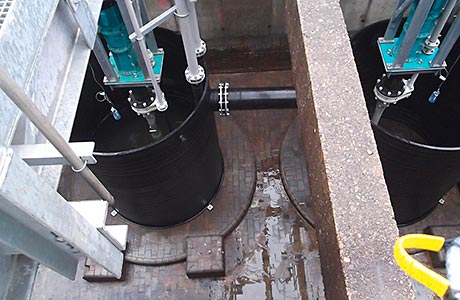
WERNERT vertical VKPF-50-250 pumps are apparently proving to be a great success for transferring chemical effluent from collection tanks to a treatment/neutralisation facility at a chemical processing plant in the north of England.
AxFlow now has five variable speed vertical, cantilever shaft pumps handling a mixed acidic solution. The chemical plant produces refrigerants/propellants such as A22 and Klea, and because of the highly corrosive and hazardous nature of the effluent, the pump shaft in the liquid area is protected by a plastic sleeve whilst the bearing in the thrust bearing lantern is protected from aggressive vapours and gases by a PTFE radial shaft seal ring.
First installed in 2010 and added to in 2012, all five pumps were required in order that the plant could comply with new emission controls. It is important that the continuous transfer of the chemical effluent is done reliably in order to prevent an overflow that could result in an emission to the local waterway. The Wernert pump is capable of handling this challenging application as it is especially suited to pumping liquids that are contaminated with solids. It is a true “cantilever shaft pump”, having support bearings above any process liquid, thus eliminating the need for external bearing lubrication or chance of wear due to exposure to the process liquid.
This type of pump is not provided with any sealing against the pumped liquid because leakages flow out above the impeller through lateral openings in the delivery suspension pipe.
“When it came to designing and building the pump installation, the challenges involved matching the required duty, ensuring the pumps were able to withstand the fluid duty and designing a means to easily remove the pumps when required,” says Mike Buhagiar, AxFlow Senior Sales Engineer with the company’s Process Department.
“We were called upon to provide technical advice and explain the pump details,” he continues. “We provided cross sectional drawings to explain the pump construction, supplied the pumps on time and offered installation and commissioning advice. To date, pump performance has been good and very reliable, with no pump changes required.”