Clearfleau, a UK company that designs and builds on-site AD plants for liquid bio-degradable residues, looks at how AD is used in sectors like food and drink production
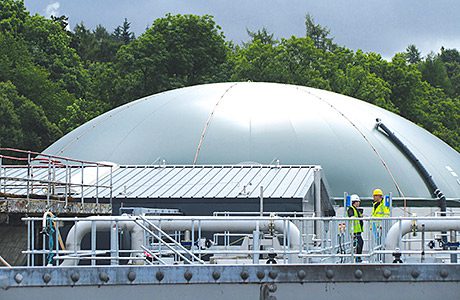
THE on-site energy recovery sector, an emerging market with a number of innovative British companies, is offering alternatives to long-established methods for handling bio-degradable residues.
Larger scale centralised facilities are used to handle materials collected by local authorities but smaller scale solutions offer effective options for on-site energy recovery. It is also more effective to convert production residues into energy closer to where they are produced, so that the heat and power can be utilised in commercial applications.
A number of energy recovery technologies (such as AD or biomass combustion) can operate at a smaller scale, to handle production residues from farms or food and drink processors (and SMEs in the catering sector), either on-site or at community facilities. This avoids transporting residues for longer distances, with loss of energy value, while incurring transport and other costs.
Although on-site solutions do not always generate large volumes of energy (smaller on-site AD plants can still achieve output levels of up to 250kWh – enough energy for 400 houses) they do offer other benefits, including cutting green-house gas emissions and more efficient handling of residues. Smaller businesses can supply residues to local plants or work with others to develop shared facilities, if there is not a local service already available.
On-site AD can also be integrated as part of on-site wastewater treatment plants to replace outdated, energy intensive aerobic systems and provide the basis for grey water re-use. Efficient on-site digestion can remove up to 98% of bio-degradable load from food and drink production residues and utilise an unused renewable energy source. AD can also reduce the cost of further treatment required to achieve local watercourse discharge standards. Only limited aerobic treatment is required to facilitate grey water re-use.
Clearfleau’s innovative technology converts production residues into energy for use in the factory, also providing increased treatment efficiency. The on-site AD plants can be tailored to the available feedstocks and will reduce the site’s treatment and disposal costs. Energy generated and used on-site qualifies for renewable energy incentives and, combined with savings on purchase of fossil fuels, can provide an attractive return on investment.
For industrial sites, AD is able to replace outmoded aerobic treatment, work that Clearfleau has recently undetaken for both Nestlé and Diageo, at two separate sites.
Diageo: Treatment of dilute distillery residues
Clearfleau has built on-site aerobic treatment for dilute co-products from one of Diageo’s distillery sites. Diageo is expanding whisky production in Scotland and had to upgrade the handling of its liquid co-products. The company chose to deploy anaerobic technology to treat residues from the distillery and adjacent cattle feed plant, replacing aerobic treatment. With post digestion aerobic polishing, the plant discharges cleansed water to a nearby river.
The on-site anaerobic bio-energy plant was installed during 2012. A second identical plant is being built on another nearby Diageo distillery. On a daily basis, the AD plant converts over 1,000m3 of dilute co-products into renewable energy, cutting treatment costs and reducing the site’s energy costs. The on-site digestion plant design could be adapted to facilitate the re-use of grey-water. Liquid anaerobic digestion generates value from unwanted processing residues and provides an investment return not available from traditional aerobic plants.
The plant was designed to fit within a limited footprint and was installed on site. It is bio-secure, in that it only treats site feedstocks. Diageo benefits from lower waste treatment charges, reduced energy consumption, and a reduction in the site’s carbon footprint.
The implications are fairly wide from a sustainability and CSR point of view, in terms of the environmental benefits of better practises for co-product and residue handling, and the fact that the biogas is used to replace fossil fuels.
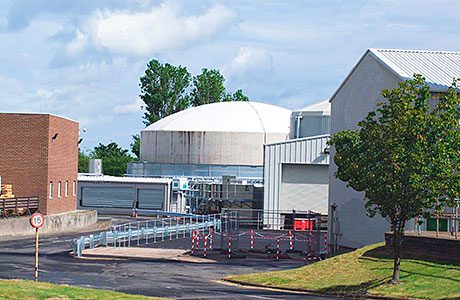
On-site AD for Nestlé Confectionery
Clearfleau’s on-site anaerobic treatment facility at the Nestlé site in Fawdon, Newcastle (see image, below) converts trade effluent (previously discharged to sewer) and confectionery production residues into biogas, used to generate renewable electricity for the factory. Power output is limited to under 250 kWh but there are other benefits. This recently completed facility has enabled the site to save costs and generate value from its production residues, while again reducing its carbon footprint.
The Fawdon site is being developed as an integrated sustainable technology demonstration site for the wider Nestlé business. The project illustrates how renewable energy recovery can be integrated with (but not detract from) the core business. The system also handles solid production residues from the factory which are dissolved to allow them to be included in the liquid based system. Also the ancillary equipment can be located in modular units to facilitate installation and provide mobility but also to help with access to export markets.