Chesterfield BioGas looks at how to get rid of unacceptable components in the output gas from an anaerobic digester (AD), when a major part of the feedstock is food waste and the output gas is intended for biomethane-to-grid (BtG) processing.
ACCORDING to WRAP, the UK produces over 15 million tonnes of food waste per year. Over half this figure comes from non-domestic sources such as food processors, retailers and the hospitality sector, where bulk collection of the waste may be more consistent and its make-up somewhat more viable compared to domestic collections.
Every gram of this organic food waste is a potential source of biogas feedstock. But, at present, only a tiny fraction realises its maximum calorific and commercial potential through being upgraded to biomethane and injected into the gas grid.
We know that the number of AD plants is now increasing at a rapid rate due to the release of brakes on investment. Even so, very few ADs are processing – or plan to process – food waste as the primary feedstock element.
This appears to have nothing to do with the problem of eliminating non-biodegradable residuals, but much to do with the content of the upgraded biogas. When derived from food waste there are particular challenges in ensuring that, when upgraded to biomethane, the output gas complies with the Network Entry Agreement of the local gas transporter who will be accepting the gas into the grid.
What gases need to be removed?
While removal of CO2 is the main function in biogas upgrading, there are three other groups of components in the AD gas produced from food waste which must be treated:
• Hydrogen sulphide (H2S)
• Siloxanes and
• Volatile organic compounds (VOCs)
H2S features to some degree in the output gas of all ADs. Stripping out this inert component to less than 1ppm is a fairly standard part of biogas water-wash upgrading and thus, while essential, its treatment by that method is not new. But removal of siloxanes and VOCs is a much more complex matter.
A ground-breaking project is about to prove that the challenges that these components pose can be overcome with efficiency and reliability.
The installation of a BtG system at the ReFood waste processing site at Widnes has been described by one industry expert as potentially “one of the most efficient and effective biogas projects in all Europe”.
Chesterfield BioGas was awarded the contract to supply the 1800m³/hr Greenlane® water-wash upgrading system and de-sulphurisation package. The upgrader selected is a standard Totara model, capable of processing up to 2000Nm³/hr. This core technology is not new. But the way it has been combined efficiently with siloxane and VOC removal is very definitely novel.
Treating such soluble gas components prior to the main upgrading process is known as pre-wash and allows the subsequent water-scrubbing system to work at maximum efficiency.
Food waste and the gases it produces
One helpful input with devising the new system was from ReFood’s waste collection site already in operation at Doncaster, similar in its mix of food waste contents in the AD feedstock to those expected at Widnes. Although not sending gas to the grid, the Doncaster raw biogas was used to very accurately anticipate the clean-up regime that would be needed.
The collected food waste for both sites is a mixture of organic solids including fruit and vegetables, salads, meat, pies, sauces, dough and other baked products. But also included is sugar water, soft drinks and beer, cooking stock, blood and other liquid wastes, plus process drain water. Thus the risk assessment for the output gas at Widnes could be fully anticipated in advance and the additional system equipment developed.
Siloxanes and VOCs are more prevalent in food waste than in other AD feedstocks such as energy crops. They derive from a number of sources including traces from detergents and cosmetics
The Doncaster site produced various concentrations, made up of more than a dozen different VOCs. Some of these are borne in the process drain water which is included in the collected waste.
Around 20 different VOCs were found to be present in the biogas. Typical of those requiring treatment was d-limonene, which is widely used in cleaning agents. The gas we use in our homes and businesses has to conform to the smell we classically expect. Such a component may affect the odour of the injected gas and may also change its calorific value (CV), both of which will have closely specified parameters in any Network Entry Agreement.
The problem with siloxanes
Siloxanes – which are a sub-group of silicones – present a specific problem. They too can find their way into the waste mix from detergents, cosmetics, even migration from paper coatings.
For the purposes of efficient digestion, the solids and liquids form a beneficial blended slurry which can be kept consistent in the AD, particularly in terms of its calorific value. But siloxanes do not decompose in this sludge and, when heated in the AD, will become volatile. This is an unwelcome addition to the product biogas because, when burnt, It can have a corrosive and clogging effect on gas appliances because it will convert to silica particles. The effect has been likened to putting sand in your car engine.
For treatment and removal of siloxanes, CBG produced a high-rate variant of the activated carbon method. While some of this polishing technology is not new, its application to cleaning up biogas from food waste is the first of its kind in the UK. A combination of elements in the filter absorbs the multiple components.
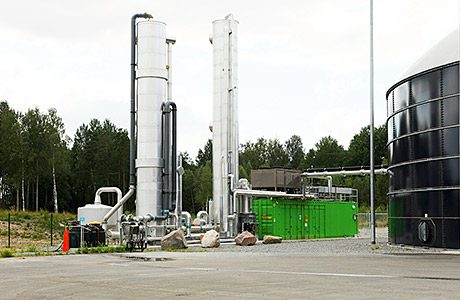
Avoiding clogging
In the AD product gas at the ReFood site, H2S is present in concentrations of about 1200ppm. This is oxidised to elemental sulphur in a biofilter and can then be returned to the AD. An additional adsorbant filter reduces the residual content to <1ppm, so satisfying the safety requirement of the gas transporter.
This biofilter precedes the activated carbon filter in the system, otherwise the activated carbon would react primarily with the H2S and rapidly clog. A blower raises the gas pressure between the biofilter and the activated carbon sections.
Hitherto, such biological systems only operated at oxygen concentrations greater than 2%. The 1% limit placed on total oxygen within the gas for UK grid injection meant further oxygen could not be added.
To accommodate this, a system was developed for low oxygen applications. It uses minimal water supply and sends virtually no process water to drain. No chemicals are involved so there are no storage and operational issues.
A dual channel system allows the filtration media to be periodically replaced without interrupting the operation of the main gas throughput system. Increasing the size of the polishers lengthens the period between media changes. A digital monitoring method indicates the level of available capacity in the filters before they require replacement. All such innovations produce a marginal increase in initial capital costs but very low on-going operational costs.
The key commercial benefit is that the system throughput is not slowed down by the need to remove VOCs.
The Widnes upgrading project is due for completion in the second quarter of 2014.
As with most chemical processing systems, optimising efficiency by assessing the right configuration of processing functions is key. When the feedstock is organic, and when that feedstock can be unavoidably variable, greater challenges are presented. The success of the CBG approach to the ReFood waste processing project will provide testament that such challenges can be overcome in making the most of biogas from food waste.