Fay Dashper, Senior Recycling Manager for the Alliance for Beverage Cartons & the Environment (ACE) UK, describes the processes used at a new UK recycling plant
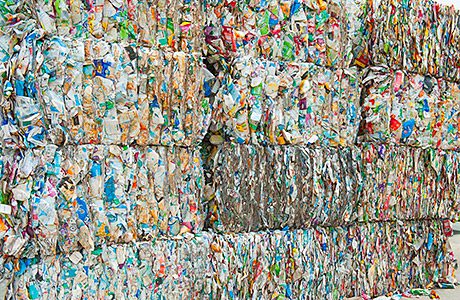
IN 2003 just one of the UK’s 406 waste collection authorities included cartons in its kerbside recycling scheme, and three years later there were still only 4% of local authorities collecting cartons as part of their kerbside recycling services.
Today as a result of the Alliance for Beverage Cartons & the Environment (ACE) UK working closely with local authorities, 57% now collect cartons at kerbside – and when ACE UK’s own bring-bank system is included, beverage cartons are now collected in 91% of UK local authority areas.
This demonstrates the real progress made in improving access to carton collections – until last year, however, the best available solution to recycle cartons was to export them to Sweden as there was no facility in the UK.
On 3 September 2013 that changed with the opening of the UK’s only purpose-built facility for recycling beverage cartons in Stainland, West Yorkshire. This is a joint initiative between ACE UK, representing the beverage carton manufacturers Tetra Pak, Elopak, and SIG Combibloc, and paper and packaging producer Sonoco Alcore.
Capable of recycling up to 40% of the cartons manufactured each year for the UK food and drink market (25,000 tonnes or 1.25 billion cartons), the facility is expected to further boost beverage carton recycling rates in the UK.
Sonoco Alcore is taking advantage of the strength and quality of the wood fibres found in cartons by using them to manufacture industrial-strength coreboard at its paper mill located on the same site. This in turn goes to produce cores and tubes for industrial applications.
But what are the processes which ultimately lead to cartons becoming coreboard? It all begins with the collection of used beverage cartons from homes and bring banks across the UK, which are then sorted, baled and transported to the recycling facility.
Pulper conveyor
The bales are loaded onto the converyor belt and dewired so that the cartons are fed loose up the conveyor to the pulper. This is done in 1.8 tonne batches
Pulper
The cartons are then pulped using ambient temperature water in a Kadant Helisoft pulper, using a large rotating screw. This separates out most of the polythene and aluminium layers from the paperboard layer. The paperboard is broken down into a fibre slurry, with the whole process taking around 20 minutes.
At this point the fibre slurry and the fine polymer and aluminium layers, used in beverage cartons to prevent leakage and provide a barrier to oxygen, are separated. What is now known as polyAl goes into a large conic drum, to be washed and to screen out heavy contaminants such as stones and glass. The moisture is then squeezed from the polyAl using a dewatering screw compactor and then a baler. At the moment the polyAl bales are being stored whilst ACE UK investigates the best recycling or recovery option.
The fibre slurry then moves on through the Poire coarse screen. This is used to filter out the smaller pieces of polymer, usually from the outer layer of the carton, from the fibre slurry (the polymer joins the polyAl from the conic drum to be processed in the dewatering screw compactor prior to baling) and the fibre mix is then sent to the final screening process.
ScreenOne
A specially-designed Kandant ScreenOne then removes any glue or final tiny pieces of polyAl from the fibre slurry using an energy-efficient three-stage screening process in one machine.
Drum thickener
The mixture then passes through the drum thickener. This reduces the water content to the optimum level for storage, with water content being reduced from 97.5% to 95% and the fibre content doubled to 5%.
Final stock chest
This has a capacity of 300m³, containing water and 15 tonnes of carton fibre and is the end of the line. Here the reprocessed fibre is stored in a large tank, ready for blending with fibre from Sonoco Alcore’s other on-site pulping operation to produce industrial-strength coreboard.
While this process is recycling the strong wood fibres contained in beverage cartons and putting them to good use, the facility is also a great opportunity for local authorities to reduce their carbon footprint, as the road and sea miles travelled by cartons for recycling will be reduced. Previously cartons collected through ACE UK bring banks were recycled at mills in Sweden. Recycling cartons at the UK facility instead will lead to an estimated annual reduction of 122 tonnes of transport-related CO2.
Also, if by using the new recycling facility local authorities and waste management companies are diverting beverage cartons from landfill, they will avoid landfill tax and gate fees. When the plant is running at its full capacity of 25,000 tonnes per annum, it could potentially reduce these costs by £3.6 m (based on 2013/14 costs).
By creating a domestic end destination for used beverage cartons, with a fixed price per tonne for cartons delivered, the facility also provides price stability for local authorities and waste management companies. It also enables local authorities with no-export policies for recyclates and an eye on the circular economy to have their cartons recycled in the UK.
Since its opening there has been a great deal of interest shown by a number of local authorities and waste management companies with the likes of Conwy, Belfast, Chelmsford and Mid Devon Councils already using the facility.
We are confident that, with the financial and environmental benefits the facility brings, it will drive an even greater step-change in beverage carton recycling in the UK.