Phil Burge of Swedish bearings company SKF explains a new aeration blower solution, and its potential to lower energy costs, improve operational efficiency and reduce environmental impact im the water and wastewater sectors.
A dual squeeze on cost and carbon now requires a much finer balancing act between replacing and maintaining assets to garner the best efficiencies.
Reactive maintenance, essential in applications such as water and wastewater treatment where managing process parameters can be pivotal to public and environmental health, is no longer good enough for day-to-day operations. Unplanned maintenance is also 50% more expensive than planned maintenance, leading to secondary damage and an excessive spares inventory. It’s not news to engineers that poorly maintained assets can also consume more energy than their more finely-tuned counterparts; and downtime is never cheap.
The water industry knows it needs to deliver more effective operational planning, but it’s not only utilities that face a knowledge deficit – it is also process and manufacturing operations that employ water and wastewater treatment. However, they do not yet have enough quality data to enable them to deliver the outcomes they need. So where do engineers and technicians begin? One option is to investigate a significant new innovation in aeration blowers, which are used throughout the wastewater sector as part of the biological treatment process.
The activated sludge process, invented in Manchester in 1914, remains to this day at the heart of the wastewater treatment process worldwide. The process relies on the injection of air into tanks containing wastewater, to encourage the large scale growth of natural bacteria that break down the impurities it contains. Depending on the type of wastewater being treated, the resulting liquid from this aeration process can usually be returned to the environment, although in some cases further treatment processes may be required.
The traditional compressors, or “blowers”, used to inject air into wastewater use large quantities of electricity. For example, Severn Trent spends around £9 million a year on electricity to run 300 blowers at its treatment works, more than half of the entire cost of wastewater treatment in the region. And industry estimates suggest that one per cent of all of the UK’s electricity is consumed by compressors used for the aeration of wastewater at the nation’s utility companies.
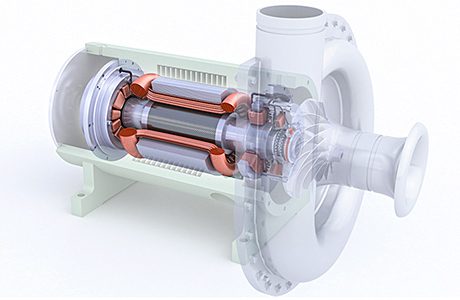
Induction motor losses
Traditionally, these aeration blowers have been powered by induction motors with mechanical gearing and oil-film bearings; although reliable, this configuration suffers from high energy consumption and power losses, accounting for up to 80 percent of the lifecycle costs of an aeration blower.
Although the introduction of variable speed drives has helped to reduce energy consumption, this effect has been limited. Given the cost of electricity consumption – and the associated CO2 emissions – water companies have been investigating alternative solutions with lower energy costs
PMM-based blower benefits
The new aeration blower system comprises a high-speed permanent magnet motor (PMM) available in sizes 75 kW-350 kW, active magnetic bearings (AMB) and integrated AMB control system. There are a number of features that enhance performance; for example, unlike traditional induction motors, the PMM maintains efficiency at half-load and half-speed operation. An energy efficient high speed motor / magnetic bearings system for aeration blowers also uses less mechanical parts than a traditional drive system, which means reduced maintenance, while powerful built-in monitoring and diagnostic capabilities maintain high performance and reliability.
With the introduction of a new system combining direct drive, high speed permanent magnet motors, active magnetic bearings and a magnetic bearing controller, it is possible for energy consumption to be significantly reduced. Additionally, the new system provides higher efficiency under nominal or partial loads, is more reliable and quieter, and is almost maintenance free.
Energy efficient aeration blowers with high speed motors and magnetic bearing systems now have the capability to reduce energy consumption by up to 40 percent. In wastewater facilities, the aeration blower system can demand as much as 80 percent of the plant’s total energy consumption, so the new solution offers the potential to make huge energy savings. When used in one of the largest 350 kW blowers it may result in annual savings of 500,000 kWh, which equals a 375-ton reduction in CO2 emissions.
This innovation represents a new and sustainable approach to the problem that targets the market challenges faced by the water and wastewater industry. An energy efficient high speed motor / magnetic bearing system for aeration blowers that meets the demand for energy efficiency, and the need for a reduction of maintenance and service costs, as well as the requirement to comply with air quality and safety standards. Compared with a traditional blower, one of the new wave of motors in a 350 kW centrifugal air blower offers payback on investments in one year from energy savings alone.
With this new generation of aeration blowers available for use throughout the wastewater sector as part of the biological treatment process, operators can be freed from the high energy consumption and power losses associated with systems powered by induction motors that depend on mechanical gearing and oil-film bearings, and make significant efficiency savings on the lifecycle costs of running an aeration blower.
The new innovation in aeration can make a significant improvement in the performance of water and wastewater plant, reducing energy and maintenance costs.