Envirotec asked Richard Gueterbock of Clearfleau a few questions about the state of the AD market in the UK, and where his own company’s technology fits in.
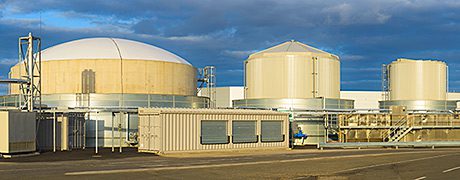
• Can you offer any general comment on how AD technology is evolving? It’s now being used as a replacement for aerobic bio-plants, in the case of your customers. How is it better than those plants, and when did the technology reach that stage?
The adoption of AD in the UK is developing quite fast but is not always being helped by a degree of incompetence at the top (DECC is unable to accept that smaller scale, on-site technologies, with decentralised energy supplies are key to a low carbon future). The AD sector has three key markets, the large scale merchant sector taking waste from local authorities to large centralised plants, the on-farm sector (includes plants based on livestock manures and the more questionable practice of digesting purpose grown crops) and the on-site industrial sector, where Clearfleau are focused.
The larger scale merchant AD sector, reaching over-capacity in some areas, may have limited growth potential. The future growth potential is with on-site AD, on farms, in communities and on a range of industrial sites, treating bio-degradable residues near where they are produced. Clearfleau now has 3 contrasting operational reference plants, with 4 new plants being built during 2014. For industrial sites, AD is able to replace outmoded aerobic treatment,
AD is able to treat a wider range of materials than previously recognised by policy makers, including many bio-degradable feedstocks that were previously discarded. Clearfleau’s on-site technology treats dilute liquid residues from Whisky production that were a problem for AD systems just a few years ago. It can also be adapted to take higher solids materials (by converting them into a high energy ‘soup’ for feed to the liquid based system). It is based on a pump based closed loop system. The on-site systems, fed with a consistent, homogenous feedstock are stable and robust.
• I’d gained the impression that the microorganisms involved in AD, and the process by which they do their work, are not really a focus of innovation. That this is aspect of AD that is more or less sorted. And that the innovation in recent times has been with things like clever ways of preparing waste for the digester, to optimise the yield of biogas. Is this a fair picture? In what ways is Clearfleau’s approach innovative?
We are aware of research being undertaken into optimisation of methanogenic bacteria. Much of the research for the merchant plant sector is focused on feedstock preparation. However, this sector is dependent upon imported technology and does not have long term growth potential.
Gas yield optimisation is not a big issue for Clearfleau. Our system is able to remove up to 98% of COD (the measure of biogas potential), one of our USPs. Our approach is innovative because we install our AD plants on a limited footprint and they offer a robust and cost effective means of dealing with production residues on-site.
UK research should focus on how to facilitate operation of plants on a smaller scale, to provide effective local solutions. AD can handle bio-degradable residues close to where they are produced and can supply energy to farms, factories or rural communities. Also smaller scale technology for converting biogas into vehicle fuel (bio-methane).
• Can you give an example of any factors that might make a particular site or facility unsuitable as a candidate for installing one of these digesters? Presumably a certain threshold level of biogas generation would have to look likely to be reached to guarantee a return on investment. Is that all there is to it?
Once a processing site has decided that it wishes to evaluate on-site AD and we have shown that a project is commercially viable, we visit the site to assess the integration with the site and things like energy optimisation. Apart from meeting site payback targets there are two major issues that need to be discussed, the scale of the plant and how it will fit on the production facility (and hence whether there is space and sufficient biogas potential in the feedstock) but also the nature of the solids based feedstock. Our technology is designed to treat a liquid feedstock but the AD can be adapted to accommodate higher solids materials (as is the case at Nestlé*), turning them into a gas rich ‘soup’ for the digester. However, there are some sites that have higher volumes of solids feedstock, where our technology would not be appropriate.
• Can you comment on the construction used for your own digesters? For example, is it a basic glass-fused-to-steel tank?
We tend to use concrete digester tanks that are very similar to those used by other AD technology suppliers. The concrete provides good insulation and is topped by a double layered gas holder, which is used to store the gas before it is fed to a CHP unit or for smaller plants to a boiler. We are developing a smaller scale modular system for sites with lower feedstock volumes and it is possible that we will make use of glass-fused steel for these sites. The tank is a very minor part of the value of the AD plant and we are more focused on effectiveness of the anncilliary equipment.
• Are there aspects of your digesters that make them cost efficient, compared to many of the others available on the market?
AD plants are not cheap to build but it is important not to under-engineer them (for materials like concrete and steel, costs continue to escalate, as do energy and other costs that are key drivers for many clients). Also our on-site system is designed to fit on a confined footprint. The digester tank is much smaller than it would be without the efficiencies that have been built into the process design. Hence a digester can be built on an industrial site without taking up too much valuable space. For instance Nestlé’s plant is installed on the edge of a truck parking area next to the Metro line.
• The Nestle plant referred to is the company’s facility in Fawdon, which is being developed as an integrated sustainable technology demonstration site for the multinational food and beverage company.