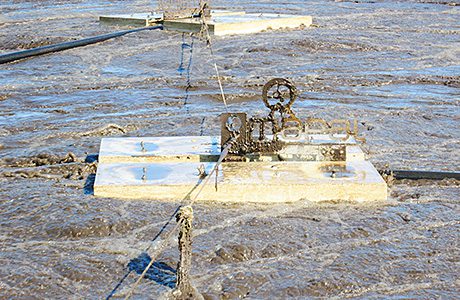
THINK of waste water treatment and for many, whether in the water utilities or manufacturing sector, that means old, concrete reactors with a mechanical surface aeration system slowly churning to oxygenate the liquid beneath.
The chances are the system is unreliable and it fails regularly, adding to maintenance costs and increasing downtime. Another certainty is that energy consumption will be high, as old mechanical aerators are known to be energy inefficient.
Whilst costly and time consuming to install, sub surface “fine bubble” aeration is acknowledged as an efficient alternative to introduce oxygen into the water to create an aerobic environment and thus allow organic matter to start degrading. However, specialist flat bottomed reactor tanks need to be built for the system to be mounted on, which also means this technology cannot be used in lagoons.
Against this background, the UK water regulator is constantly challenging the utilities to come up with smarter, cleaner ways to treat waste water. In the commercial sector too, the same aims apply, with the difference that dairies, paper mills, farms and other producers of high quantities of waste water are driven by the sometimes sharper focus of their shareholders.
Marrying the benefits of surface and sub-surface approaches
Wastewater treatment specialist Mapal Green Energy has come up with an alternative that it says is now tried, tested and live in more than 35 locations worldwide, including Brazil, South Africa, Angola, the Congo and importantly the UK, where Thames Water, United Utilities and Anglian Water are in advanced implementation of or actually trialling the equipment.
Mapal’s answer is floating fine bubble aeration. Described as a revolutionary solution, floating fine bubble aeration approaches the challenge of water oxygenation by marrying the strengths of surface aeration technology – easy to install and accessible for maintenance – with the efficiency which is derived from sub surface fine bubble aeration systems. With no moving parts generating friction and driving high energy consumption, a key benefit for users is apparently its dramatically reduced energy bill. As energy costs rise, so the environmental impact of high energy consumption is now a key consideration. Tests around the world have shown that in some cases, compared to surface aeration, a plant’s energy consumption can be reduced by up to 70% using the Mapal system, with savings of 50% regularly achieved.
By substituting a surface mounted propeller for a system of blowers and floating diffusers, not only is energy consumption reduced, but installation and maintenance is dramatically simplified. The system does not require a tank to be drained, nor does it need to be attached to a concrete floor. Aerators are automatically adjustable to water depth and because they float, are always level, thus delivering an even flow of oxygen within the reactor.
Wet and live installation is the norm, which makes for a very fast changeover of plant and a minimal downtime. The units are made from robust stainless steel, so have a long life and as a modular system, the installation can be added to or reduced quickly and easily. Thus far, their largest UK installation is designed to handle a flow rate of up to 10,450m3/day in wet weather.
The Mapal technology can be adapted for aggressive and hazardous liquids and is therefore suitable for application across a wide range of industry sectors where a solution based on aeration is required. Liquid waste from the paper, food and beverages, petro chemicals and other industries can all be treated.
In one UK live trial with Anglian Water, the signs look very promising. Matt Pluke, Energy Manager, Anglian Water comments, “Stanbridgeford is an example of how our established energy partners have worked together with new partners Mapal Green Energy to deliver energy-savings, whilst protecting the needs of our customers and the environment. Mapal Green Energy’s Floating Fine Bubble Aeration system was chosen because it was more energy efficient than the previously installed technology and, as a floating modular system, it can reduce operational down-time by being easier to install, add to and maintain. During the first six months of the pilot, we have seen energy savings averaging 22% attributable to Mapal Green Energy’s system.”