
UK plastic storage tank manufacturer Niplast has supplied two storage tanks to Suretank, a manufacturer of CCUs (Cargo Carrying Units) for the offshore oil and gas industry. The tanks, to be used to store sodium bromide and hydrochloric acid in the Caribbean, were commissioned by the customer in polypropylene rather than their usual steel construction, due to the highly corrosive nature of these chemicals.
An unusual, but key, design request from the customer was that the Niplast tanks would be able to be transported horizontally within a purpose built mild steel frame based on an ISO container specification. To facilitate shipping from location to location, the empty tanks will be held in the horizontal position via a flanged bolted base and a polypropylene lined cradle. When configuring how to best locate and support the empty tank within the frame, Niplast and Suretank designers had to take into account transportation loads and acceleration factors. Upon arrival in the Caribbean, both tanks will remain in their steel frames, but lifted into the vertical before being put into use. This required Niplast designers to consider the axial and circumferential thermal expansion of the tank whilst remaining in the steel frames.
Fabricated in Niplast’s manufacturing plant in Stockport, the tanks were designed and constructed to the CEN standard BS EN 12573, with a 50 degrees Centigrade working temperature and a 20 year design life. They each have a capacity of 22800 litres or 143 bbl for bulk liquid storage of either 50% concentration sodium bromide or 15% hydrochloric acid. If required, the tanks can be fully drained, returned to the horizontal and transported to other locations.
Shane Gilson, General Manager, Suretank UK said, “On our initial contact with our customer, the requirement for a poly tank was requested. Suretank had worked with Niplast before and invited them to become involved in the initial stages of the engineering concept.
It became apparent in this early stage that Adrian Greenwood and his team understood the complex requirements for the offshore industry and our customer. The Niplast team were dedicated and extremely professional in every aspect of this contract, the tanks were of exceptional build quality and have been manufactured to our demanding specification.
I would have no hesitation in recommending Adrian and his team and look forward to working again with Niplast in the near future.”
Niplast Director, Adrian Greenwood commented, “I am delighted that Niplast have been selected by such a discerning worldwide brand as Suretank Ltd. Our designers have relished the challenges that this unusual application for Niplast Tanks has thrown up.”
Niplast claims to be one of the UK’s longest established and leading plastic storage tank brands. The company manufactures storage tanks to CEN standard BS EN 12573 and to DVS 2205, to a maximum capacity of circa 100,000 litres.
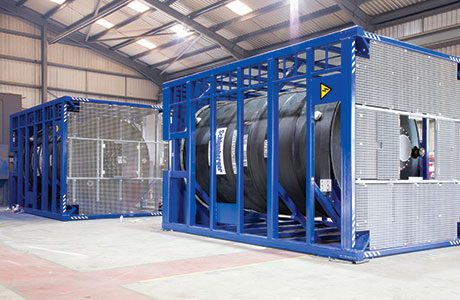
Tanks are butt-fusion welded from extruded thermoplastic sheets, which ensures inherent long-term strength. BSEN 12573 recognises that this technique gives the highest possible weld strength, above all other types including helical extrusion welding. All Niplast fabrication technicians are certified to EN 13067 by The Welding Institute (TWI).
Polypropylene, high density polyethylene and PVDF thermoplastics are used as materials of construction, due to their high corrosion resistance and their stability over a wide range of temperatures. These materials have considerable advantages over some traditional steels such as their lightweight nature, higher corrosion resistance and cost advantage.