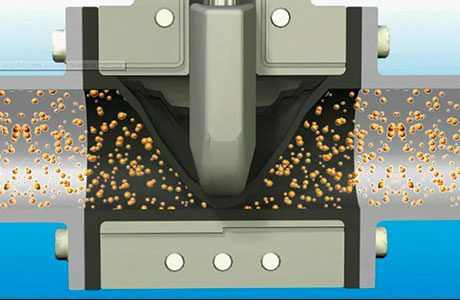
Dave Fitzpatrick of Cheshire Pump Company explains why he thinks peristaltic pumps and pinch valves are the best option for systems that process abrasive slurries.
WE talk to a lot of people about peristaltic pumps, pinch valves and their application. We think that this type of technology is the best solution for the transfer, isolation and control of abrasive process streams.
There used to be issues associated with peristaltic pumps such as poor hose life, an inability to run continuously – especially at high temperatures – and high lubricant consumption.
Using a contra-rotating roller design eliminates all of these problems and allows published performance data to be considered across the whole performance field without restrictions on temperature or continuous operation.
In our opinion pinch valves are the best option wherever a valve must both seal effectively and always open when required, and operate with little if any hydraulic losses. The combination of all three of these factors provides the lowest whole-life cost of ownership.
Incidentally, both pieces of equipment have one wear part: the pump hose in the case of the peristaltic pump, and the valve sleeve in the case of the pinch valve.
Peristaltic pumps: Where they’re used and how they work
This pump design is the best for pumping heavy abrasive process streams such as mine tailings, thickener feeds, and the thickened slurries commonly found in mining and mineral processing. The pumps use a rotating element to move a hose contained in a housing, a mechanism rather like that used in a hospital dialysis machine.
Most peristaltic pumps use lobes or adjustable shoes to rub against the hose, this creates friction, requires large volumes of lubricant, shortens hose life and prevents continuous running.
One manufacturer uses a contra-rotating roller design which simply squeezes the hose. A rolling design imparts little friction into the hose, and this minimises the volume of lubricant necessary, extending hose life, reducing motor power and, most importantly, it means that this pump can run continuously even at high temperature.
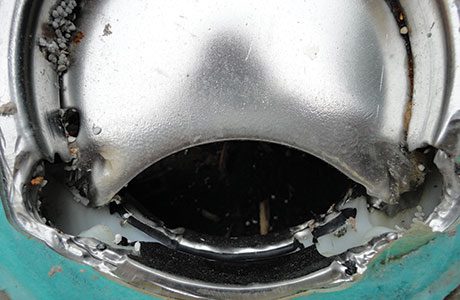
This rolling design can also be operated in the reverse direction by a simple switch on a speed control. This means that if there is a plugged flow or settled material lingering in a vessel, the pump can reverse material back into the system rather than shutting it down to rectify the problem.
This rolling design is used on the world’s largest peristaltic pump capable of 100m3/hour at 10bar continuous flow. For use in a typical pipeline layout, the inlet and discharge connections should be in-line. This enables the flow path to remain constant allowing the most practical layout.
Positive displacement pumps such as this are suited to heavy, dense materials with 70% dry-solids content being common.
Viscous fluids are also a common application. Normally this is quantified in the unit Centepoise (cP). If you think that egg yolk may be around 300cP, toothpaste is typically 15,000cP, a rolling design peristaltic is capable of over 28,000cP.
To get the best from the pump good engineering practice and common sense are required: keep the suction lines short large diameter and minimise suction lift
This type of pump ranges from small dosing pumps to very large industrial machines weighing over 6 tonnes.
Pinch valve design
There are any number of designs that purport to be pinch valves. Most of them are not true pinch valves they are diaphragm or
bellows types and are unsuitable for heavy industrial use and
applications such as dewatering pumps, quarry process water systems, and pump and pipeline isolation.
Only two types will provide real benefit: single acting or double acting pinch valves. Both use an internal sleeve made from a wear resistant material such as natural rubber, or styrene butadiene. This internal sleeve is “pinched” to create the valve function, open or closed (however it is not as simple as that – it never is let’s be honest).
Valve function should be considered at this point, and two very simple questions:
1) Is your application a shut-off / isolation valve? (e.g. pump isolation, pipeline isolation, fully open or fully closed).
2) Is your application a control valve? (e.g. used for the control of flow/pressure in a pumped system).
For shut-off applications you may use either single acting or double acting valves. Selection depends on size, pressure rating, frequency of open/close cycles and method of operating – manual (handwheel and handwheel with gearbox) or automatic (hydraulic, pneumatic or electro-motor actuated).
For simple, low cycle use, a single acting pinch valve can be used as they are less complex (and cheaper). They may employ non-metallic or metal body material and are ideal for pressures up to 10bar and diameters up to around 200mm. This type of valve closes from one direction across the full diameter of the sleeve.
For high cycle use a double acting valve should be used. These have a metal body, can handle pressures up to 100bar and feature diameters up 1200mm, as well as larger diameter specials. This type of valve closes from opposing directions across half of the sleeve diameter. Double acting pinch valves can also be used for control applications but they must be selected by the manufacturer, and never simply to match the pipeline diameter. There are complex technical matters to be taken into consideration for control valves.
If you ask your operators or plant designers to tell you about a valve that will always open when you ask it to, and will always seal when required, you are likely to have a long wait.
A well selected pinch valve has one wear part – the valve sleeve. When it wears, you replace it and put the valve back into operation, you do not put the valve into the workshop for a week or have to throw it in the scrap bin because it is beyond repair. Most importantly your plant will not be losing product or be stopped altogether.
Take the example of a knife gate valve that was being used to “throttle” a pump suction line in a pulp mill. The valves were 316SS, expensive, and lasted around three weeks from installation to this stage. The first pinch valve was installed in 2011 and has had one sleeve change since.
The most difficult applications
The most demanding applications for pumps and valves are not necessarily the most complex. Often these arise where you just want to shut-off, control or move a product from A to B.
In dewatering, quarrying and mineral processes, peristaltic pumps and pinch valves have the common advantage of one wear part (the pump hose or the valve sleeve, respectively).
In the UK we have pinch valves in some fairly unique industries such as nuclear decommissioning, where the instrumentation functions, such as fail-safe close or fail-safe open, are necessary but the principle remains the same: the valve (or pump) must work.
Get to know these products, which can save you time and money, improve reliability and production capacity. And understand that valves need not be throwaway items that leak continuously, or fail to seal or open.