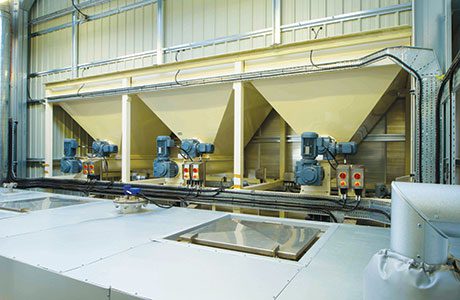
INDUSTRIAL AD systems supplier Clearfleau has revealed energy output results for its plant built for global food and beverage supplier Nestlé, one year after commissioning.
The on-site bio-energy plant was designed and built for Nestlé’s Fawdon confectionery factory, near Newcastle. The financial and environmental benefits from Clearfleau’s plant are contributing to Nestlé’s efforts to develop environmentally-sustainable manufacturing at Fawdon, as a beacon site for the overall organisation.
One year after commissioning, the plant is converting 200,000 litres per day of feedstock into renewable energy. This feedstock includes wash waters from the site and 1,200 tonnes of residual bi-products and ingredients per annum.
The biogas produced is fuelling a combined heat and power (CHP) engine, which produces 200kW of electricity, used in the confectionery production process. This is about 8% of the factory’s power requirements, cutting the annual electricity bill by about £100,000 per annum. In addition, the site has registered for the Feed in Tariff, and will receive annual payments of about £250,000 per annum.
Previously, production residues from Fawdon, the former Rowntree factory, home to gums, pastilles and Rolo’s, were discharged to sewer or fed to pigs in the locality. Following the installation of the AD plant, all bio-degradable production residues are now converted into renewable energy on the factory site.
Clearfleau used its mobile trial unit to showcase the digestion technology to the management and workforce at the Fawdon site before construction and to help optimise the process design.
Nestlé’s Head of Sustainability, Inder Poonaji, says: “We chose an innovative British bio-energy technology provider because we wanted a partner with experience who would design a plant to meet our specific needs.
“On-site treatment of production residues will help us reduce the wider environmental impact of our business and meet our sustainability goals. By working with Clearfleau, we continue to reduce our carbon footprint and generate value from food production residues.”
Key reasons why Clearfleau’s design was chosen include its high-rate liquid based digestion system, which uses an innovative and robust solids-processing system, together with its compact design to fit on the edge of the factory car park.
In addition to saving on fossil fuel purchases plus the other savings and revenue benefits, the project has reduced the carbon footprint and environmental impact of the site. The carbon footprint for anaerobic digestion is at least seven times smaller than for conventional aerobic treatment plants.
The payback period on Nestlé’s investment in Clearfleau’s AD plant is predicted to be 4-5 years. Clearfleau’s Chief Executive, Craig Chapman, says: “The advantages of anaerobic digestion are becoming more apparent and we are currently building AD plants on dairy, distillery, food and biofuel manufacturing sites. As a consequence of this industry support, we have built a strong team delivering on-site AD facilities.”