Envirotec reviews aspects of solvent recovery, and recycling chemical waste streams
SOLVENTS are used in a wide variety of industrial processes, including areas like printing, manufacturing and electronics, and are often valued for their cleaning, curing and other properties. Organic solvents in many paints, for example, facilitate their application on a surface. Solvents are often produced as a by-product of processing or manufacturing activity, and the firms responsible for these waste streams have traditionally had two options available for dealing with them: disposal (via landfill/ thermal oxidation) or recycling.
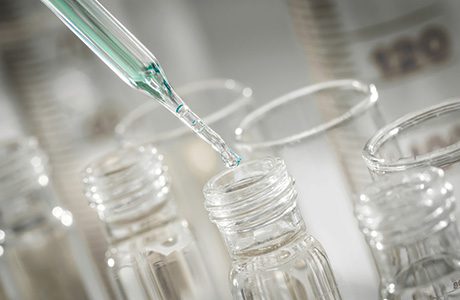
What is required by law?
Solvent recovery is covered by the European Union’s REACH regulations (the acronym is short for Registration, Evaluation, Authorisation and restriction of Chemicals), which set out the requirements that must be fulfilled by those undertaking solvent recovery. Article 2(7)(d) of REACH requires recovery organisations to ensure that:
i) The substance that results from the recovery process is the same as the substance that has been registered in accordance with Title II; and
(ii) The information required by Articles 31 or 32 relating to the substance that has been registered in accordance with Title II is available to the establishment undertaking the recovery.
Ongoing updates and guidance on REACH are available at the website of the European Chemicals Agency.
Recovery activities are also required to follow the principles of the waste hierarchy, as set out by Regulation 12 of the Waste Regulations. This states: “An establishment or undertaking which imports, produces, collects, transports, recovers or disposes of waste, or which as a dealer or broker has control of waste must, on the transfer of waste, take all such measures available to it as are reasonable in the circumstances to apply the following waste hierarchy as a priority order: (a) prevention; (b) preparing for re-use; (c) recycling; (d) other recovery (for example energy recovery); and (e) disposal.
For firms producing solvent by-products, there are a number of services available in the UK providing recovery.
Veolia provides what it calls “a unique service for the handling, cleansing, purification and recycling of a wide range of solvents”. The service encompasses everything from collection through to recovery, recycling and reuse and final disposal of residuals. It also takes care of all legal obligations, with accurate documentation provided to the customer.
At Veolia’s Solvent Recovery facility in Garston, Liverpool, the firm accepts waste streams including high residues, printing inks, cleaning solvents, solvent based paint and dirty thinners, and turns them into “green products” that can be reused repeatedly. Materials arrive, in containers such as drums, IBCs and tankers, and are sampled before being transferred to a tank farm, prior to recovery.
Distillation is a process commonly employed in the recovery process, to separate out the pure solvent and any contaminants – different methods have been in use here, including flash distillation and fractional distillation. Veolia has five distillation columns at Garston. It uses a fractionation process, which employs steam, a vacuum, and the physical properties of the solvents in question to produce high purity solvents.
More recently the firm has invested in a thin-film evaporator (TFE), said to be the UK’s newest, which supports very high-throughput processing of solvents for recovery.
The firm is equipped with the capacity to recycle 20,000 tonnes of solvents per annum via its five fractionation columns and an additional 10,000 tonnes per annum via the TFE.
Veolia offers two services: “Toll”, whereby recovered solvents are returned to customers, and “Recovery” which delivers recovered solvents that can then be sold on the open market or reused by industry. In both cases the customer is provided with an R2 recovery code (fulfilling obligations defined by the EU Waste Framework Directive 2008/98). The benefits to customers can include a reduction in the use of primary, virgin products – helping them reduce their environmental footprint and save costs.