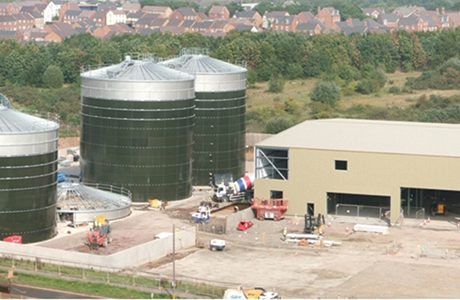
Paul Marsh reviews some recent developments in odour management for AD plants
LOCAL resident complaints and planning application refusals have highlighted the potentially malodorous influence of AD plants in the past year or so. But is the bad press merited? The EA has certainly cracked down on the issuing of permits in the sector, with odour now a central issue in the application process. Best practice continues to evolve and a wide range of odour abatement technologies is available to help.
Philip Branchflower, an air quality specialist with SLR Consulting, suggests it is only “a handful of sites” that have generated the bad publicity for AD. The number of AD planning applications has risen steeply in the past three years, and in that time a great deal has been learned about the associated odour issues – sites pre-dating this period have been principal players in the bad publicity.
“People have spent a lot of money putting in odour control systems that either aren’t big enough or haven’t been maintained properly, so they’ve broken down after a few months,” he said. “It can take three to six months to fix these kinds of problems, which equates to quite a big impact if you live next to it.”
The greater risk from these sites has brought a greater parsimony on the part of the EA, when it comes to handing out permits. An EA permit refusal on odour grounds is extremely rare, said Branchflower, but there have been two in the past six months for proposed AD sites, with the agency seemingly unconvinced that the odour control provisions were going to be effective in these cases.
One obvious contributor to the spike in reported odour problems in recent times is the influx of food waste as a feedstock in AD. And many of these facilities are being proposed for areas where there are local residents – a very different scenario from AD’s more typical deployment in rural areas to process agricultural waste.
Reception hall issues
One of the important areas to manage odour in food waste-handling AD installations is the reception and de-packing hall, where the waste arrives. “Some sites have assumed waste coming in will be fairly low odour risk when designing the plant,” says Branchflower. “But then they’ve built the plant and started bringing in waste that’s a lot more odorous than that – it all depends on what contract you get. If you get one for 10k tonnes of foods waste, there’s a financial incentive to take that in.” Colin Froud is managing director of CSO Technik, a firm that has contributed odour abatement solutions for Saria’s AD facility in Widnes. He says in the reception part of the facility, “a wide variety of organic acids, sulphides and VOCs contribute to the odour cocktail”. Reception halls tend to have a large volume and the amount of air required for treatment is correspondingly high, he says.
The kind of odour abatement solution that comes up for consideration here includes biofiltering, which Froud describes as “a very useful technology”, with the ability to remove a much wider range of odours than bioscrubbers, for example.
On the downside it can require a bit of space: For every 100m3 of air treated you will require a minimum of 0.5m2 therefore a 20,000 m3/hr system will require a footprint in excess of 100m2, according to Froud. Biofilters also require management, to ensure they are properly irrigated.
While the smell going in is taken care of, it has been said that some people don’t like the smell coming out. Froud clarifies: “It is possible that certain types of biofilter media can, when treating hydrogen sulphide, produce dimethyl sulphide and dimethyl disulphide, both of which are odorous and a potential odour nuisance.”
He says this can be counteracted through the use of appropriate media. “We offer various media types including a shell based media that provides a degree of protection against this as the calcium carbonate in the shell provides a natural pH buffer that prevents acidification of the media bed.”
Activated carbon is a more expensive technology than biofiltering. Froud says: “It has a role to play in acting as a polishing filter behind a biofilter system if the site is particularly sensitive and even low odour emissions are likely to give rise to complaints.” It is also useful, he says, as a sole technology for smaller flows, which may be remote to the principal odour control plant and where the cost of ducting over long distances is prohibitive.
CSO Technik offers an ionisation system “Terminodour”, which Froud says has a smaller footprint, suiting it to space-constrained sites. The system is installed in the food reception hall at the Saria Widnes site.
Froud says it offers a lower cost/ smaller footprint solution to treating high volume airflows where activated carbon would be too expensive to operate and biofilters are too large to squeeze into a confined site. Also in its favour, he says, is that it not only provides odour abatement for the neighbours but it provides a clean working environment for operators as well.
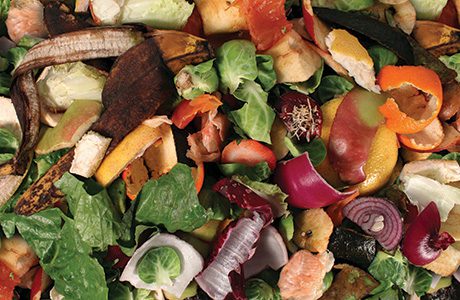
Back end odour sources
Aside from the reception hall, AD plants handling feedstocks like food waste produce odours in a few other areas. For example, pasteurisation and sludge screening tend to produce ammonia, with variable loads between pre- and post-pasteurisation.
Branchflower cites an issue with several sites of which he is aware, where still-warm – and odorous – digestate requires storage prior to subsequent stages of dewatering or drying, sometimes for up to six months. This might require the use of large lagoons for storage, and an OC solution tailored to match.
Formulating a plan
“All of these kinds of details have to be made explicit at the planning stage,” he says. The EA is now requiring that any pro-posed AD facilities have an approved Odour Management Plan (OMP) before being granted a licence to operate.
Guidance on how to complete an OMP is available from DEFRA, the EA (the technical guidance note H4 Odour Management (2011)), and the Scottish Environmental Protection Agency (SEPA). The Institute of Air Quality Management (IAQM) has a document called Guidance on the assessment of odour for planning 2014 (see http://www.iaqm.co.uk/text/guidance/odour-guidance-2014.pdf), which brings together the good practice requirements from these various sources.
The IAQM guide describes an OMP as “a live working document that formalises and describes how odour issues will be managed on site.” The aim is to show how odours will be managed and controlled, to minimise impacts, with provision made for abnormal events and foreseeable accidents and mishaps. On top of all that, it should be simple, with recommendations that are easily actioned by site operatives.
The cost of OC systems can be in the region of hundreds of thousands of pounds, says Branchflower, so it’s really starting to make a difference to the economics of a site. And in recent years, he says, people have “bought odour control systems in good faith which haven’t actually met the required standards.”
Branchflower has been hired by developers to advise on the process from the outset, and to help with things like measurement and computer modelling of emissions. “We tell people what target they need to meet, in terms of how much odour is permitted,” he says. He also advises on appropriate technologies. “If you are buying an OC system, you need to ensure there’s a performance guarantee in it,” he says, “if you want to avoid spending a lot of money on something that doesn’t work.”
Odour assessment is an important preliminary stage, and wasn’t always a requirement for the typical AD system until the past few years. These have been predominantly farm based, using animal slurries and so on, and on a relatively small scale. The situation where you’ve got around 25,000 tonnes of food waste and it’s not on a farm is “completely new”, he says.
Amongst the sites turned down by the EA in recent months was a food waste facility with houses within 50 metres, which would have required a very high level of odour control to be confident of avoiding problems.
One of the rare examples of an AD plant causing real odour problems is Biffa’s food waste processing AD facility in Poplars, which received EA enforcement notices and a large volume of odour reports in 2012 and 2013 following the commissioning of the plant.
The effort to fix it took around 18 months, and required a seemingly comprehensive effort on the part of the firm’s engineering team. This work included sampling and testing the various possible sources of odour, benchmarking these against what were deemed to be the best available technologies.
A description of the facility on Biffa’s website offers a few details on how air quality issues are now handled. The waste reception area, for example, operates at negative air pressure to prevent dust or odours escaping. This is maintained through the use of rapid open/shut doors which operate when waste is being delivered or compost removed. Air extracted from the building passes through two filters to remove odour and particles.
The facility has seen a noticeable fall in odour complaints over the last 12 months, and has operated within the terms of its EA permit. The Odour Management Plan required 15 drafts, and was approved by the EA in March. There appear to be plans to make it available on the agency’s website in the near future, as a learning tool for other AD developers.