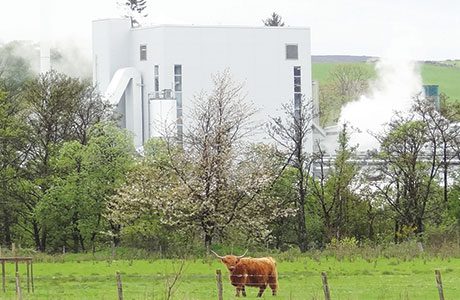
Paul Marsh reports on a novel use of distillery by-products as the feedstock for an ambitious CHP plant in Speyside, said to be the most distillery-dense region in the world.
SEEMINGLY a landmark project in terms of the efficient utilisation of distillery by products, the CoRDe Biomass CHP plant in Rothes, Speyside, has set impressive benchmarks in terms of performance and availability for large-scale biomass CHP, not to mention coming in on time and under-budget.
A £60 M construction project completed in 2013, the concept was conceived in 2005 when the Combination of Rothes Distillers (CoRD) – a joint venture serving several distilleries in Rothes – was approached by Helius Energy, a UK company which specialises in identifying, developing, owning and operating biomass-fired electricity generation plants.
Helius had an idea about using draff – a distillery by-product – as a biomass fuel. At the time CoRD was looking at how to both gain control over the costs of its by-products processing and improve its environmental footprint. Other motivating factors included the reliance of CoRD’s steam evaporators on gas, and concerns over rising fuel costs. Fast forward a little and the plan for the CHP biomass plant was conceived and the contract awarded to Danish firm Aalbord Energie Technik (AET), a supplier of biomass plants in the range 25 to 170MW, which also delivered the Western Wood Energy Plant in Port Talbot in 2008.
AET’s Peter Elliot presented on the CoRDe project at May’s All Energy event in Glasgow, setting it in context with the various distillery activities. The whiskey production process takes the three main ingredients of barley, water and energy, which are variously mashed, dried, fermented and distilled until you arrive at the finished product. Two by-products are draff – which comes out of the mashing process – and pot ale, which comes from distilling, and is converted into an animal feed product, pot ale syrup. Effluent is also produced.
Feedstock firing
The CHP plant employs both draff and wood chip as feedstocks. Draff arrives at the plant by lorry from distilleries in the area and, given its 80% moisture content, has to go through a process of pressing and drying. In this case both a screen press and a rotary drum dryer are used – AET was responsible for the design of this fuel reception and handling area (as well as full CHP plant).
The wood chips received at the plant are crushed from logs, forest material and clean, uncontaminated wood (received in a chip format and stored in silos).
Around 20 to 25 lorry-loads of wet draff arrive at the plant every day. On an hourly basis the plant receives around 7.2 tonnes of wood chip and 4 tonnes of dried draff.
These are then fed into the boiler via separate feeding systems – a conveyor system in the case of the draff.
The boiler itself is “a very efficient [ (92%) ] water-tube boiler”, said Elliot, which also uses very little oxygen, around 2-3%.
A steam turbine is located in another building, attached to the boiler house, and receives steam from the boiler at 80 bar and 450degC. And there is also a nearby condensing plant, using a water-cooled condenser.
The boiler is rated at 34MW and generates 42.5 tonnes per hour of steam at 84 bar and 452degC. Ratings for other systems include 8.7MW gross capacity on the steam turbine and 23MW for the condenser. The net output power from the plant is 7.2MW, or enough to power around 9000 homes. Net plant efficiency is 48%, said Elliot, “so that shows you what we can get out of a good quality CHP plant”.
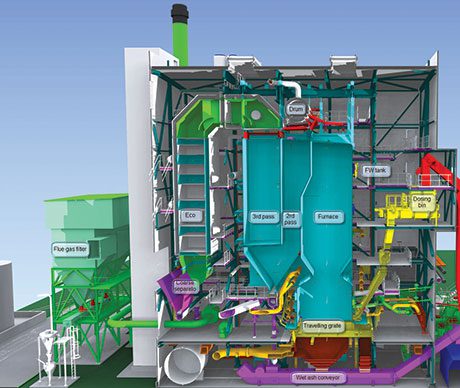
Emissions and boiler design
The CHP plant reduces the CO2 emissions from an equivalent sized fossil fuel plant by around 46k tonnes per year, “so it’s a significant plant in that respect”, said Elliot, and performs well below EU limits on emissions. Fairly stringent requirements had to be met on that score given the plant’s location in a town. NOx reduction for the plant is Class A compliant, for example.
The flue gas is cleaned using an AET urea-based Selective Non-Catalytic Reduction (SNCR) system in addition to bicarbonate injection to neutralise acids, and bag filters for the removal of fly ash and particulates. None of it needs to go to landfill either, it seems, as the bottom ash is used as an aggregate material on site while the fly ash (nutrient rich) has quite a good fertiliser value and “is currently undergoing an exemption from waste and being developed as a product,” said site manager Frank Burns, who was also present, and this is work to be completed over the next couple of years.
“Another aspect of lowering emissions is good boiler design,” said Elliot. “So we do need good boiler efficiency, low excess air ratios and precise dosing of the fuel to give good emissions.”
All in, the construction phase of the project lasted around 26 months. “The development of a biomass plant has always been a long and arduous road”, said Elliot, “And you can see from the dates that it didn’t happen that quickly.” Planning permission was granted in 2009 and boiler erection began in May 2012. Synchronisation with the grid and final handover were completed in 2013, with the plant going into commercial operation in July 2013.
Less fuel than guaranteed
For a plant like this, suppliers like AET have to provide customers with guaranteed performance and availability figures, said Elliot, as a condition of the contract. A June 2013 test using 100% wood chips provided 91.6% of guaranteed consumption. Putting it another way, this means the plant used 8.4% less fuel (for the same power consumption) than was stated in its original guarantee, he said. Similarly with a mix of 45% wood chips and 55% draff the figure was 89.5% of guaranteed consumption.
The same test also provided a net power production of 105.8% of the guaranteed value. “So If we fix the amount of fuel input, the plant actually produces 5.8% more power than we guaranteed,” he said. He attributed this to properties of the plant such as high fuel efficiency, high cycle efficiency and lower than expected in-house power consumption.
Availability is also a vital criteria for a plant like this because of its implications for revenue and “because there is a process behind all this that needs to keep going”. A test conducted between December 2013 and December 2014 recorded a net power production figure of 99.4% – “very good”, he said – and a slightly lower figure for the draff handling and firing system of 94.8%, where there were some issues.
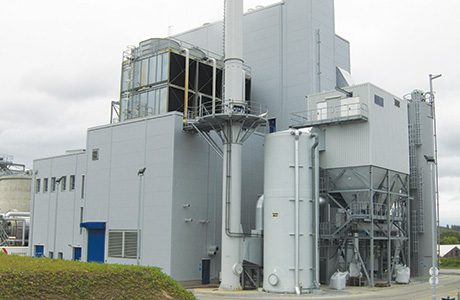
Wood and draff dosing
Part of his presentation covered AET’s wood and draff dosing system, employing the firm’s own design of dosing bins and rotary valves. For many years AET has worked with the German chip board manufacturing industry, developing a dust firing system for the draff which is “very similar to the sander dust and sawdust firing systems that we’ve done on chipboard boilers in Germany”.
Around 50% of the fuel is actually burning in suspension when it’s injected into the boiler, while 50% falls onto the grate and moves forward.
Audience questions addressed aspects of the plant concept and the practicalities of fuel choice. One member of the audience was curious as to the merits of burning draff. With its 80% moisture content, would the energy not have been better placed making more of the pot ale syrup or producing more power?
Burns explained that the first drying process is a mechanical dry and is not energy intensive, and subsequent drying uses recycled heat, since some of the steam generated by the process is diverted from the evaporator and goes to the dryer. “So we’re using our own low pressure steam on site,” he said. “We think it’s a pretty efficient way of making fuel,” he said, referring to this process of drying the draff with reclaimed heat. The particular draff product used here has a by-product, he added, and the traditional process was to mix that with the syrup, “but we moved away from that as it required a larger drying process, using fossil fuels.”
Another questioner asked about the availability issues encountered with the draff, in the early stages. Ongoing improvements are being made in that regard. What impact will these have going forward, in terms of the fuel mix between wood and draff that can be achieved?
Burns said that during the commissioning phase and first year of operations, the principal problems with the plant had been to do with materials handling of the draff from distilleries. “Now that we’ve resolved those, we have a much higher draff throughput into the plant and we’re running the boiler now at it’s maximum draff firing capacity. So there is an envelope of operation where you can go from 100% wood to 30% wood and 70% draff – and we’re now at that maximum firing rate in the envelope.”
The plant in Rothes is accredited as a combined heat and power plant under the Renewables Obligation legislation.