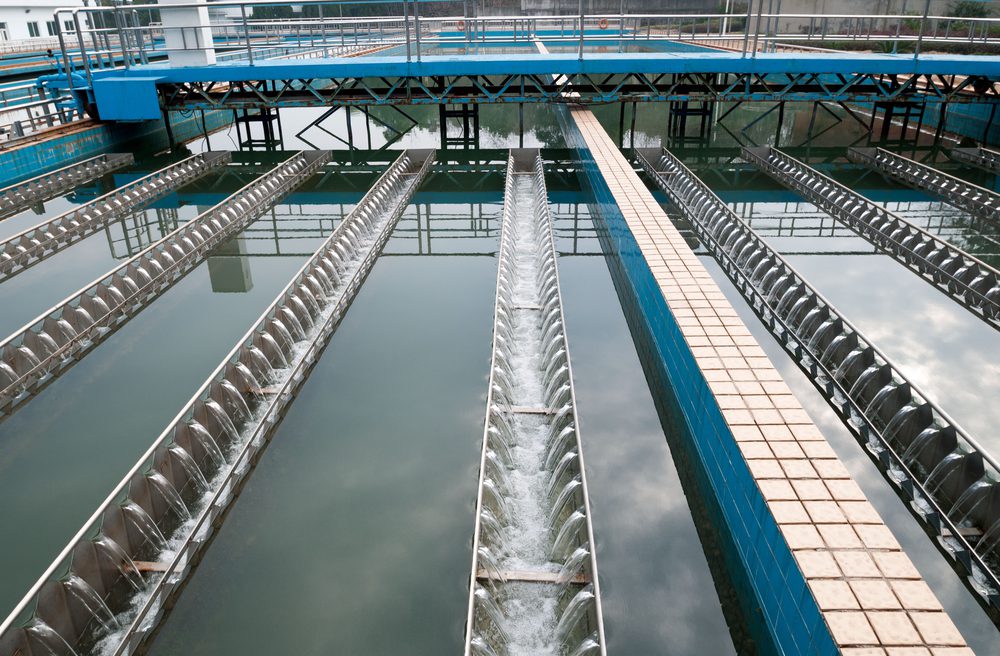
By Andrew Thornton, Head of Project Development (Northern Europe) with water quality expert and equipment manufacturer Hach.
With the soaring cost of energy and chemicals and ever increasing pressure to find sustainable solutions, the water industry is in the same dilemma as many other large power- and chemical-hungry undertakings. The operation of existing infrastructure is subject to ongoing increases in operating costs, which are only going to rise further, coupled with growing pressures to operate in a sustainable fashion. The scope for low cost, sustainable solutions is constrained by the need to manage ever increasing costs alongside ever more stringent discharge consent conditions. The development and implementation of innovative processes will help. However, without a large investment and capital outlay, it is difficult to foresee more than a short-term resolution. One can only assume that over the decades to come, many more sustainable capital projects will materialise. Still, the short-term goal must be to find innovative ways of utilising existing infrastructure more efficiently.
Waiting for the right instruments
The concept of RTC for process optimisation is by no means new but until recently had not seen deployment in the UK wastewater sector. The potential benefits have been widely publicised in recent years so what’s been the problem? A significant barrier has been the limitations of available instrumentation. Sensors and probes for the monitoring of wastewater constituents have been around for a long time but early models tended to prove cumbersome and unreliable, with confidence in their data being extremely low. Rapid technological advancement has seen the advent of much slicker models with far greater accuracy and reliability. As a result their use has grown significantly within the wastewater sector, with some utilities becoming heavily reliant on them for process monitoring. Over time this has made it possible to have more confidence in the data received from such instrumentation and this in turn looks likely to beget further deployment in the future.
How does it work?
The last few years have seen a step change in the use of advanced control systems for aeration processes and more recently for chemical dosing systems. In either case the operating principle is much the same. We currently design our plants to meet the maximum envisaged treatment capacity with an additional safety factor and apply an element of process control to deliver the required amount of treatment. RTC takes this to a more advanced level by using instrumentation to measure the parameter we are treating in real time and applying the appropriate level of either aeration or chemical dosing. This gives us the confidence to move away from the standard approach and in times of low load or concentration we can apply significantly less power or chemical to meet the required output. This allows us to achieve large reductions in our operating costs with minimal capital investment. Typical savings in terms of aeration are anywhere from 15-25% on a well operated plant (see Figure 1).
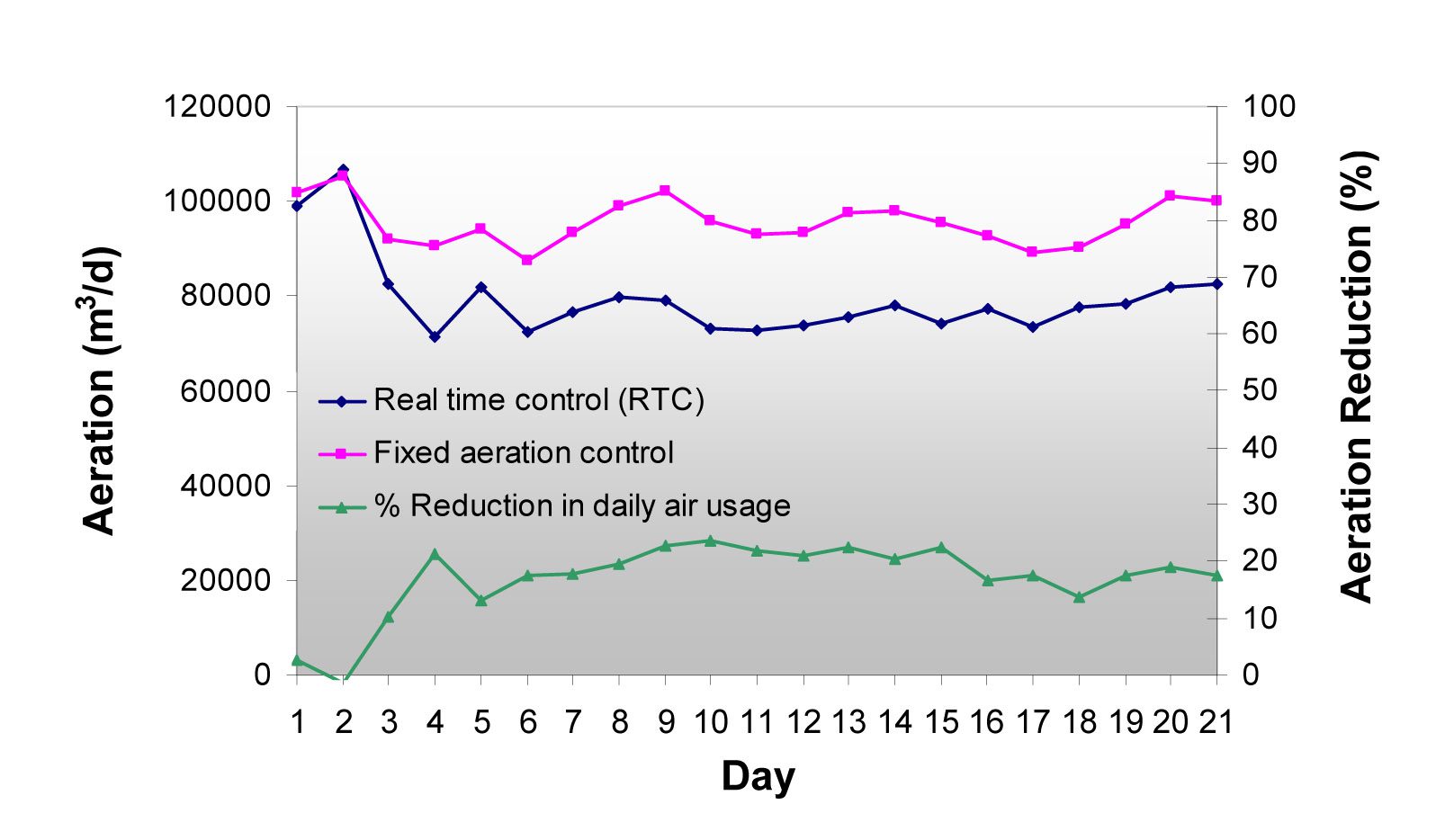
Greater process visibility
There are additional advantages to advanced process control on top of reducing the annual operating costs of existing plant. The status quo in the UK is that “compliance is king” and more often than not process optimisation is seen to come with an element of consent failure risk. In reality nothing could be further from the truth. With real-time measurement and control comes greater process visibility and the ability to react appropriately to abnormal conditions – more often than not the reason for failure.
Furthermore, with tighter control the implementation of RTC can often offset the requirement for civil upgrades in the case of tightening consents or population increases and there are a growing number of projects demonstrating this. Where applicable, utilising RTC as opposed to plant extensions, we can reduce capital outlay by as much as 95% compared to the conventional approach.
Case Study: MLE plant
The following case study briefly outlines the potential. The plant under consideration was an MLE plant with 3 lanes configured to meet a total N consent of 15 mg/l (Figure 2). The new consent imposed was a Total N of 10 mg/l. The conventional approach would have been to upgrade the plant to a 4-Stage Bardenpho by constructing an additional post anoxic zone with methanol addition and a reaeration zone. The alternative RTC solution was to provide additional instrumentation (Figure 2), a model based nitrification controller and an internal recycle controller. The RTC solution was approximately 5% of the cost of the conventional solution. After significant consideration the RTC solution was chosen and commissioned in AMP 5. As a result a large capital investment was avoided along with eliminating the requirement to dose supplemental carbon. In addition, the operating costs were reduced by 15% due to the installation of the model based controller. This is an exceptional case but does outline the potential that advanced process control can offer.
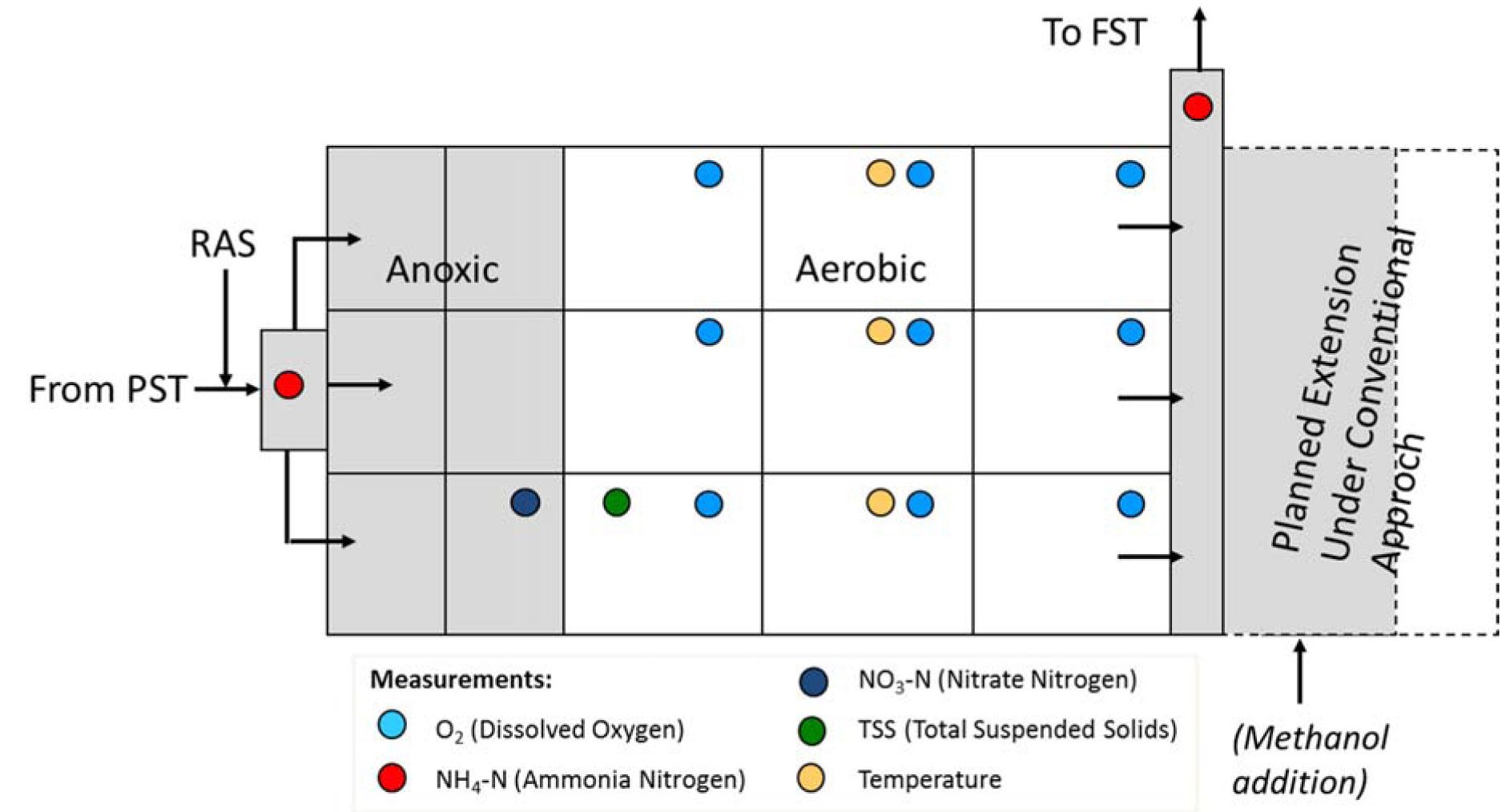
Beyond aeration: Dosing chemicals gaining popularity
To date, the majority of installations have employed aeration control but there is currently an increase in the use of advanced control of dosing chemicals such as iron and aluminium for phosphorus removal, methanol for denitrification and polymer for sludge thickening and dewatering. These processes have been used extensively throughout Europe and there are numerous case studies validating the approach.
A critical factor: Asset condition
Something that must always be considered when implementing RTC systems is asset condition, since this is the single most important factor when attempting to improve process performance with advanced control. Poor assets are more difficult to optimise and it is sometimes impossible for advanced control to make any significant difference at all. RTC always works best on well maintained and well operated plants and with post installation it is of paramount importance that the instrumentation put in place for the application of control is maintained and available, otherwise the plant will return to being operated in much the way it was before.
There are numerous success stories for the implementation of RTC in the wastewater industry both in the UK and across Europe and it is the belief of many that we have barely scratched the surface with far more potential moving forward. However, we are a long way from this approach becoming business as usual and we must take the right steps to ensure that we get the most out of our assets in the future.
Andrew Thornton will chair a panel debate on the scope for real-time control in the UK water industry at Aqua Enviro’s European Waste Water Management Conference & Exhibition (EWWM) on 12-13 October 2015 at Manchester Town Hall. The panel members will be Simon Mazier of Perceptive Engineering, Oliver Grievson of Anglian Water, John Cannon of Southern Water, Ajay Nair of MWH, Anthony Kyriacou of Severn Trent Water, and Ferran Ripoll of SISLtech-Aqualogy.