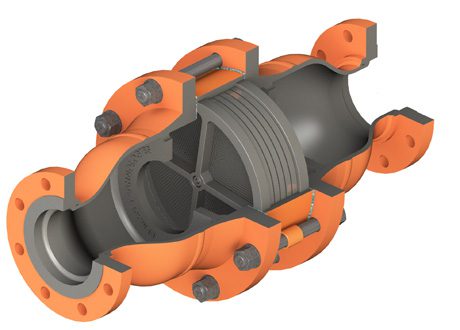
Elmac Technologies has developed the UCA Series of unstable detonation arresters, said to offer better pressure drop and flow performance than any equivalent stable or unstable detonation arrester currently on the market.
By combining its E-Flow™ element technology with a patented High Energy Dissipation System (HEDS™), Elmac says it has created a series of detonation arresters which not only protect against unstable detonations, stable detonations and deflagrations; but which can offer operating energy savings of over 10% and 30% compared to the market leading stable and unstable detonation arresters respectively.
Added to this the fact that unstable detonation arresters have no restrictions on placement within piping systems, or any requirement for secondary protection measures; then the UCA Series sets new benchmarks for performance, versatility and economy.
The UCA series of detonation arresters is designed and manufactured according to the latest flame arrester standard EN ISO 16852, and is ATEX approved and certified for gases in explosion groups IIA1 and IIA.
Over the past 2 years Elmac Technologies has invested heavily in new product development and has, as a result, successfully developed its enhanced flow (E-Flow™) flame arrester element technology which is now used in its EVA, EVB, EHB and ESA series of end-of-line arresters.
CFD studies yield optimal design
The development of the E-Flow™ element technology was achieved by drawing on the benefits of Computational Fluid Dynamics (CFD) to model the behaviour of a system in order to investigate the flow behaviour, including the study of flow patterns and the prediction of pressure drop. This information was then used to optimise designs for the end-of-line flame arresters whilst avoiding the need for costly plant trials.
The next logical step was to take the lessons learned from the development of the end-of-line arresters and transfer the technology to in-line deflagration flame arresters. This was successfully achieved in Elmac’s LCA and LEA series of in-line flame arresters.
To complete the development schedule Elmac’s engineers then turned their attention to detonation arresters with the aim of creating the world’s best-performing devices. Merely installing E-Flow™ technology into a standard unstable detonation arrester did not provide sufficient improvement in terms of pressure drop and so a new High Energy Dissipation System (HEDS™) was developed and patented. HEDS™ facilitates suppression of the detonation shockwave within the arrester housing allowing for a reduction in the number of element banks required in the arrester; thus lowering resistance to flow and reducing the weight of the device.
Where are they suitable?
These new products are suitable for use with gases in explosion groups IIA1 and IIA and have model variants which include:
– Operating pressures up to 1.2bara
– Short-time endurance burn capability of up to 20 minutes
– Removable, modular easy-clean elements
– Size range of 15mm to 300mm nominal bore
– Concentric or eccentric reducers
In-line unstable detonation flame arresters are designed to prevent the propagation of pipeline explosions in their developed stages, when flame velocities reach supersonic velocity and extreme pressures are experienced. As such these units are utilised in applications where the close proximity of the flame arrester to an ignition source cannot be achieved, perhaps due to pipework restrictions or maintenance access requirements.
Maximising flexibility and safety in vapour recovery systems
One common application of unstable detonation flame arresters is vapour recovery systems. The flame arresters are installed in the vapour recovery venting lines to prevent any internal ignition source, possibly from a scrubber, pump or fan; propagating back into the tanks’ vapour space. Elmac unstable detonation arresters can be used in isolation as single protection equipment – EN ISO 16852:2010, offering maximum safety with unrestricted flexibility in installation.
The new UCA detonation arrester ranges minimise the impact of using an arrester on the process, meaning higher flow rates are achievable with smaller flame arresters. Accordingly, the E-Flow™ detonation arresters are “smaller, lighter and easier to maintain with significantly reduced fouling in the element”, says the firm.
“Certification testing of our new UCA series has proved that not only have our engineers made the world’s best unstable detonation arrester, but that they also exhibit better flow and pressure drop characteristics than the market-leading stable detonation arresters,” commented Peter Evans, Operations Director at Elmac Technologies.
“This is a significant landmark for Elmac as we have a long-standing commitment to supplying only the safest possible solutions to our customers, and only offer unstable detonation arresters in any application where a detonation could occur.”
Elmac can assist clients by specifying appropriate products for proposed new installations and plant retrofits. In addition, Elmac are able to provide advice on the positioning of these products in an installation and to evaluate the suitability of flame arresters or other protection devices already fitted.