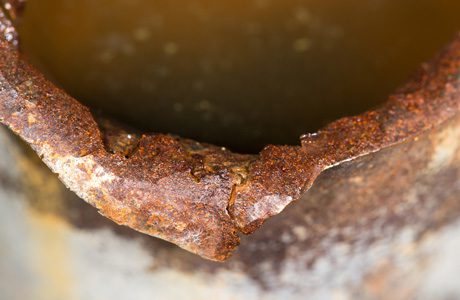
BSI, the business standards company, is developing a new standard, BS 8701 Full ring ovalization test for determining the susceptibility to cracking of linepipe steels in sour service — Test method. The draft standard is now open for public comment until 31 March at the following link: http://drafts.bsigroup.com/Home/Details/55910. Comments are invited to ensure the final standard is robust.
Measurement of corrosion and environmentally assisted cracking of pipelines has always been of great importance to the oil and gas industry for the safe transportation of petroleum and natural gas products, not least because of the damage that can be caused if a pipeline fails and spills product into the local environment. This standard updates the 1996 HSE Guidance document OTI 95 635 which features the protocol for ensuring pipelines are properly tested to avoid environmental damage from pipeline failure.
Factors that affect corrosion in pipes
Different factors have to be taken into account when testing pipes: such as environments, age of pipeline, materials used, coatings etc. In addition to this, the types of corrosion must be accounted for too, such as sweet corrosion, (wet carbon dioxide (CO2)) and sour corrosion (wet hydrogen sulfide (H2S)). Both scenarios exist in pipelines.
Prior to testing materials and weldments for pipelines, basic parameters need to be established such as what was the pipeline designed for, what is the environment inside and/or outside? Whether the internal environment is sweet or sour etc. In the case of testing the influence of the sour environment, previous guidance is not up to date. However, BS 8701 rectifies this and looks at the cracking problems that can occur in pipelines.
Ways of assessing the likelihood of cracking
One of the best ways of assessing the susceptibility to cracking is through testing a full ring specimen of the linepipe in a sour environment where a stress level is applied at two regions on the specimen. Both during and following exposure of the specimen to the sour test solution, ultrasonic monitoring can define crack initiation and propagation, and a metallographic study made post-test, to classify any defects found by the ultrasonic survey.
David Fatscher Head of Market Development for Sustainability at BSI said: “Although we are more used to hearing about spillages from oil transporters such as tankers, it is not unheard of for pipelines to fail and lose the products they are transporting. In any case this spells disaster for the ecosystem into which a spill occurs. This standard can help ensure that spillages from corroded pipelines is minimized, as this type of spill can be just as detrimental to the environment (be that marine or otherwise), as a tanker spill. We aim to keep all relevant guidance up to date, and by developing BS 8701 we can help manufacturers keep an eye on the hydrogen sulfide based wet pipeline scenarios.”
BS 8701 is of importance to manufacturers of pipelines which are designed for the transport of petroleum and natural gas products. It was developed using a collaborative consensus-based approach with input from industry experts within the petroleum, petrochemical and natural gas industries. The final standard is expected to be published in July 2016.