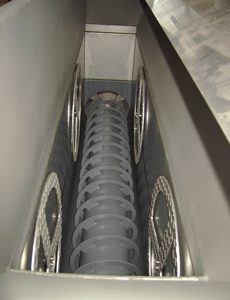
Pumps that can reliably convey thickened sludge with a high dry matter content, without the risk of overpressure, have been supplied by Netzsch Pumps, a specialist in difficult pumping applications, to the municipal works of a small town in South Hesse, Germany.
The pumps, the company’s NEMO® BF progressing cavity pumps, have been equipped additionally with a bridge breaker and lubricant injection to prevent accumulation of sludge.
The Hessian wastewater plant was producing thickened sludge with a dry solids ratio of 25 to 27 percent, which could no longer flow but had to be transported through the plant. The plant management reached out to Netzsch, which provided two special progressing cavity pumps that are capable of ensuring thickened sludge conveyance at a stable pressure and volume, regardless of viscosity.
How does it work?
The progressing cavity pumps can successfully convey media with such a high dry matter content due to their superior conveyance principle, says Netzsch, in which a rotor rotates in an oscillating motion within a fixed stator, resulting in conveying chambers being formed and media being transported from the inlet to the discharge side. The NEMO® BF hopper pump used also has a horizontally-positioned conveying screw around the coupling rod and a removable conical formed compression chamber, which together improve the introduction of the sticky substrate into the actual conveying elements.
In this application, there was the risk that solid material contained in the thickened sludge would entwine or interlace in the upper part of the hopper and thus block the infeed. To prevent this from occurring, the NEMO pumps were fitted with the Netzsch-patented asynchronous bridge preventing modules (aBP-Module®), which prevent the formation of lumps that can cause bridge building in a sewage sludge conveyance system.
The aBP-Module® is made up of a hopper extension with two spoked wheels attached to its internal sides. Sitting deep inside the hopper and very close to the walls, the turning wheels generate the effect of moving hopper walls, which creates a shearing effect in the medium. This shear effect tears the bridges apart in the early stages of formation, so the mix can be conveyed continuously.
Anti-seize agent
Additionally, the risks of overpressure and system failure due to the thickened sludge conveyance are mitigated by the injection of an anti-seize agent downstream from the pumps. The polymer mixture is precisely dosed and injected with a NEMO® BY progressing cavity pump. This pump’s location in the conveyance system allows the solution to be uniformly distributed across the inner wall of the pipework, reducing friction by up to 70 percent, reducing conveying pressure to approximately 116 psi / 8 bar, and permitting significantly more economic transportation of the thickened sludge.
The conveyor systems also include independently-powered fans to cool the pump motors in the event of overheating due to low conveying volume, and a dry running protector system which protects the components against damage in an emergency.