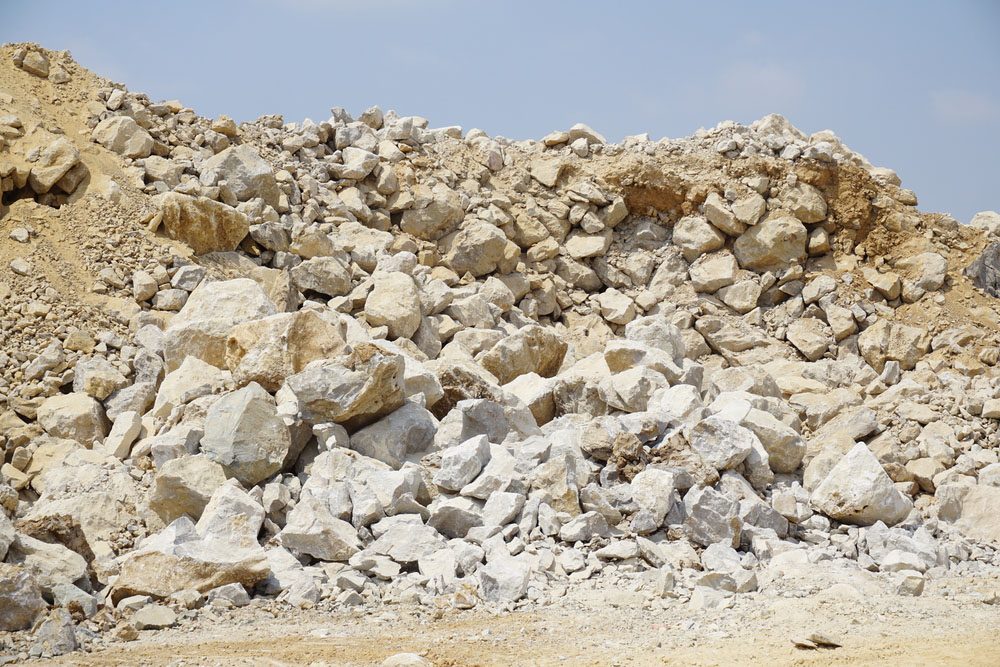
The LEILAC (Low Emissions Intensity Lime And Cement) consortium has secured €12 million in funding over five years from the European Commission Horizon 2020 Grant programme to apply and demonstrate a breakthrough technology that will enable Europe’s cement and lime industries to reduce their carbon footprint significantly. The consortium will also contribute a further €9 million towards the project.
The consortium is led by technology provider Calix, and comprises Heidelberg Cement, Cemex, Tarmac, Lhoist, Amec Foster Wheeler, ECN, Imperial College, PSE, Quantis and the Carbon Trust.
Cement is the primary ingredient in concrete, one of the most important materials in the built environment, providing foundations for most major structures including buildings, roads and bridges. The cement and lime sectors also directly employ more than 388,000 people in Europe, making an important economic contribution to the region. However, the cement industry alone accounts for up to 5 percent of global carbon dioxide (CO2) emissions, while the lime sector has the highest CO2 intensity relative to turnover.
Progress to date
For years, both the cement and lime industries have made continuous efforts to improve their environmental performance and have successfully reduced CO2 emissions from the production process. As around 60 percent of CO2 emissions are released directly and unavoidably from the processing of the raw materials, cost effective carbon capture technologies are needed on a large scale, to help reach the EU’s 80 percent emissions reductions target by 2050.
The LEILAC project aims to help the European industry to achieve these targets effectively and economically. Calix’s Direct Separation process provides a common platform for carbon capture in both the lime and cement industries. This can help these sectors to thrive in the face of tighter international CO2 emissions regulations, where the only options may be to capture and store CO2 instead of emitting it into the atmosphere.
Two-thirds of CO2 emissions from cement and lime production are generated through the breakdown of limestone into lime and CO2 in furnaces. Calix’s technology re-engineers the existing process flows, where it is capable of capturing almost pure CO2 released from the limestone – potentially with no additional energy costs or environmental impact.
How the new system works
The system design is unique, as the furnace exhaust gases are not in direct contact with the limestone. In this indirectly heated reactor, the energy from the heating gases is transferred to the limestone via a special steel vessel. The CO2 released from the limestone can therefore be separated in an almost pure form, offering a unique opportunity as the technology can capture these emissions without significant additional costs or increased energy use. The technology is complementary with other carbon capture methods already developed in the power and cement sector, such as oxyfuel, and can make use of alternative fuels.
During the first three years, the project will focus on finalising the design of the demonstration plant, to be constructed at the HeidelbergCement plant in Lixhe, Belgium once the necessary permits have been secured. The high temperature Direct Separation Calciner pilot unit will then undergo two years of extensive testing in a standard operational environment, at a feed rate capacity of 240 tonnes per day of cement raw meal and 200 tonnes ground limestone respectively, over a continuous basis for several weeks.
Fundamental research on the process demands and performance will be carried out to demonstrate that the technology works sufficiently and robustly enough to be scaled up to full operational use. The project results will be shared widely with industry at key intervals during the testing.
For further information about the project visit www.leilac.org.uk.