Engineering design firm Reece Innovation offers some background on its new ‘Flusher Gate’, which promises to make sewer pipes self-cleaning.
Ever since pipelines began to be laid to transport wastewater away from domestic, industrial or commercial sites, one of the greatest difficulties that needed to be overcome was keeping them clean and able to perform to their design specification.
Traditionally, the cleaning operation has been undertaken using high pressure jetting systems that are either manually applied in larger diameter pipes or using mobile high pressure jetting units at smaller diameters. This option, however, requires regular CCTV inspections of the pipes in order to establish which pipes require cleaning, followed by the mobilisation of a cleaning crew and its equipment to complete the operation, an operation that comes at significant cost.
Over the past 18 months, Reece Innovation has investigated the requirements of the UK water industry to develop a cleaning system that will reduce the cost of regular cleaning activities, whilst still maintaining the cleanliness required in water companies’ sewer networks. The result of this research and development is the Flusher Gate.
Using the pipe network
It has long been understood that in gravity pipelines, the presence of high volume, fast flowing wastewater is effectively a self-cleaning mechanism within the pipeline, with the flows preventing silt build-up and minimising the ability of Fats, Oils and Grease (FOG) to adhere to pipe walls and cause blockages over time. This fact was used as a basis upon which any new cleaning system should operate, even where flows were small and slow.
Historical evidence has shown that the concept of using retained flows to ‘flush’ sewer networks has been around since Roman times. This was the concept selected to form the basis of the new Reece Innovation design. So building on Roman ingenuity, the firm has created a modern version of the design that is robust enough to withstand today’s harsh and often variable sewer conditions.
Using this basic principal, a system was devised that comprised the installation of a passive device within a sewer pipeline to control the flow of effluent. Holding back flows until a sufficient volume was retained meant that when released, the movement of the effluent under gravity down the pipeline would generate a flow that would make the pipe effectively self-cleaning. By holding back flows upstream of a collection point and releasing them when required, this would not only initiate cleaning downstream of the ‘dam’ point, but would also generate flow on the upstream side that would do the same job in the pipes used to store the retained volume.
The Flusher Gate
After careful consideration of the potential options and following extensive development and evaluation, the Flusher Gate design was completed. Designed with ease of maintenance in mind, the unit is simple to install as well as being reliable and robust, enabling it to work effectively in harsh sewer environments, thereby significantly reducing sewer cleaning costs over time.
The Flusher Gate comprises a patented latch door mechanism that can be pre-set to open at a point when a specific volume has been retained, the latter providing pressure on the Flusher Gate face to initiate opening (although the system can also be operated from the surface if required). The effluent volume on the upstream side of the gate applies a step change in the resultant moment acting on the Flusher Gate, so when the flow is released there is a highly effective flush and scour sequence throughout the pipe length covered by the Flusher Gate installation. The off-centre pivot of the Flusher Gate makes operation of the unit highly efficient.
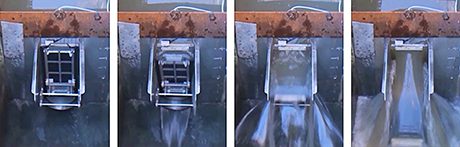
There are also a number of seal options, depending on the application required, including an easy to attach and replace single piece ‘standard’ edge seal. These options enable the system to be easily adapted and installed in multiple manhole configurations including situations such as a straight flow through to a 90o bend installation. The Flusher Gate is available in a variety of sizes and can be designed to fit most pipeline configurations from circular to egg-shaped as well as non-standard cross-sections.
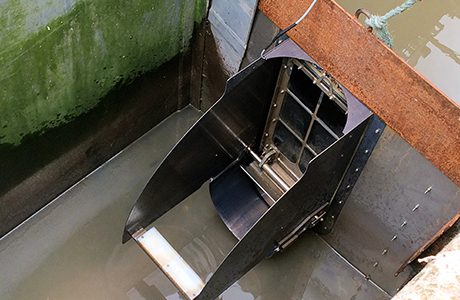
The Flusher Gate also has a ‘Fail Safe’ design, so that the unit cannot cause back-up during high flow events. One additional advantage of this is that the Flusher Gate is also seen as an aid in flood prevention by maximising the hydraulic flow/effluent handing capacity in sewer networks.
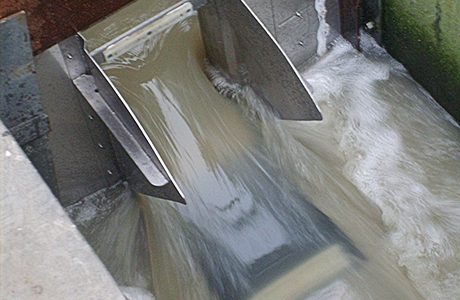
Reece Innovation has also developed a Telemetry Module that can run alongside the Flusher Gate, providing full and real-time information about the operation of the unit over time. This provides data from which engineers can infer the sewer condition and flow rate within the length of pipeline covered. The module can be monitored onsite or remotely via WI-FI or the telecommunications networks.
Commenting on the Flusher Gate development for Reece Innovation, James Martin, Managing Director said: “Having reviewed many of the challenges of the UK Water Industry, we have developed a cleaning system that fits all their requirements. We see this as a potentially widely used tool through the water industry, not only domestically, but also internationally. With the Flusher Gate now commercially available, our team is on hand to discuss potential options for installations worldwide.”