A new aeration system has increased production and saved tens of thousands of pounds in energy for one of Europe’s largest malt makers. Simpsons Malt, which supplies the brewing, distilling and food industries, had been experiencing issues for around seven years.
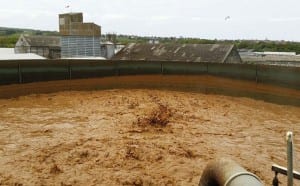
The firm’s Berwick-upon-Tweed maltings employs around 120 people and produces 236k tonnes annually. Though it comes at the end of the process, the wastewater treatment plant on the site drives the entire production facility.
At its peak, membranes within the former filtration system got blocked causing the whole plant to close down several times a week while they were cleaned. The equipment, which aerates the 17m wide tank which measures 8.5m deep, should have had the appearance of a freshly opened can of coke – but instead looked like the rapids of a river.
To solve the problem, Suprafilt, aeration specialists based in Rossendale, installed a fine bubble aeration system – which created a greater surface area than the large volume bubble and allows for better oxygen transfer.
To win the contract, a test grid was installed and it worked immediately. Gary Shaw, head of water quality and microbiology at Simpsons Malt, said: “In terms of aeration it made an immediate visible difference. The tank reached the required oxygen levels in two days and the entire biomass was transformed in about two weeks.”
The contract, valued at £58k, was installed in September 2015 and the whole system apparently paid for itself within the first month.
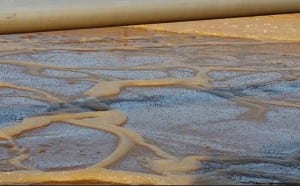
Due to the inadequacies of the old aeration system, full production loads had been dropped costing several hundred thousand pounds.
The company is also on track to save £37,000 in energy costs alone in the first year of operation — equating to 1900kW hours saved per day. Gary said: “Working with Suprafilt was positive and rewarding because they were so willing and helpful at each stage of the process.
“They visited the site, understood the issues and worked with us on a solution. By creating the test system, they gave us the confidence we needed to proceed. I’d recommend them 100%.”
From a design perspective, the new system was difficult as it had to fit around existing floor mounted system.
Suprafilt designed and manufactured two liftable grids that could be dropped into the tank – using the original tank drawings to work out where space was available below the system. At 12.5m long, with 16 tie bars each to hold them together, and featuring 250 diffusers, they were two of the largest retractable grids Suprafilt has ever produced.