Edenbridge based CSO Technik, a firm offering engineered solutions to environmental pollution problems, provides a rundown of the key issues to consider when safeguarding a facility from odour issues.
IT’S fair to say that odour is an emotive topic and sits high on the public and industry agenda when the word ‘waste’ is ever mentioned. Be it a wastewater treatment works, municipal solids waste transfer station, a waste-to-energy facility or an anaerobic digestion plant, the control of odours is central to the success and acceptance of the facility.
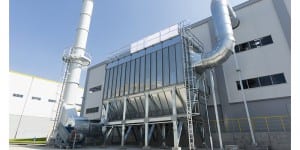
The implementation of a robust Odour Management Strategy is imperative for any organisation that produces odours as part of its daily operation as the Environment Agency is cracking down on permit applications especially where odour is concerned. With that in mind, and as best practice continues to develop and odour abatement solutions can vary dramatically, companies must adopt a systematic approach to ensure the correct and effective selection of odour abatement technology.
To assist companies formulate an Odour Management Strategy, CSO Technik adopts an approach encompassing all aspects of best practice, which does appear to vary from application to application. This will consider client expectations and needs, and help guide the selection of the best type of technology to employ. Relevant techniques include:
• Biofiltration
• Regenerative thermal oxidation
• Carbon adsorption
• Wet chemical scrubbing
• Ionisation
• Dispersion only
In addition, to truly hone in on the correct selection of odour abatement technology the following criteria is assessed for each:
• Odour removal performance track-record and effectiveness
• TOTEX – Total capital and operational costs
• Spatial constraints and planning
• Maintainability and operational up-time/down-time
• Operator interface and experience required
Traditional odour abatement technologies such as biofiltration, regenerative thermal oxides and carbon and chemical scrubbers, have benefits which are well documented. However CSO Technik has one more to throw into the mix – ionisation.
Why ionisation?
Studies of the benefits of ionised air date back to the early 1900s when Albert Einstein first theorised about the effects of ionisation on human health. Having seen the benefits on those convalescing in the Alps – a known location of high negative ion concentrations – he and his colleague Conrad Habicht collaborated to develop a device called the potential multiplier to replicate the same air quality elsewhere. It wasn’t until 50 years later that it was refined and adapted and the principle of ionisation was commercialised for air purification.
Ionisation was first introduced into the UK over 20 years ago by CSO Technik. Originally its main application was in the reduction of bacteria in food processing plants and in medical settings, however in recent years it has been applied successfully in the elimination of odours at wastewater treatment plants and large municipal and food waste reception halls.
CSO Technik’s ionisation system, called Terminodour™, was first installed in the UK in 1996 and since then the process, through an ongoing R&D programme, has become one of the most exciting developments in the field of odour abatement.
Exhaustive process development has now resulted in a tried, tested and proven system that is providing end users with cost effective odour control and improved air quality.
The Terminodour™ process combines ventilation and ionisation technology to provide efficient air distribution with maximum oxidative capacity to deliver highly effective odour control within a building or any enclosed space.
Traditional odour control systems consume a significant amount of energy and, in many cases, utilise large quantities of chemicals, water and media requiring regular and expensive disposal. Ionisation however offers a low carbon footprint solution for odour abatement as power consumption is a fraction of traditional systems. Also: ionisation does not require any chemicals, water or media, making it a favourable option where the priority is to deliver cost effective, proven odour control in an environmentally friendly manner.
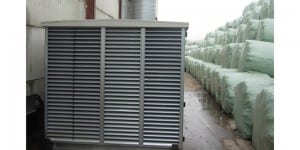
Most odour control systems extract odour from the point of source and feed via ductwork to an abatement system where the odours are either oxidised or absorbed before the treated air is emitted to the atmosphere. With an ionisation system the odours are not extracted but actually oxidised at the point of source using the building superstructure as the reaction vessel.
Footprint thumbs up
Such an approach is far less demanding in terms of space. An equivalent biofilter might require ten times the footprint of an ionisation system, to provide the requisite media bed depth and contact time, rendering it unsuitable for many applications.
Ionisation is therefore particularly suited to large volume low level odour applications such as MSW transfer stations.
The heart of an ionisation system is the air handling unit (AHU) that contains the principal system components; these include the inlet filtration section, fan(s), plasma reaction chamber and ionising modules. As it is not operating as an extraction system and not operating against a closed head (for example, a media bed comprising woodchip, carbon, or similar) the pressure drop across the system is minimal and therefore fan motor sizes are significantly reduced providing enormous whole life savings in energy costs.
Terminodour™ ionisation systems use a plasma reaction chamber containing bi-polar ion tubes operating from an alternating current that produces both negative and positive ions in a 5:4 ratio (as found in nature although in greater quantities). When this super negatively charged ionised air comes into contact with generally positively charged odorous molecules a process of oxidation occurs.
Ionisation has the capacity to oxidise all organic odours and its efficiency is a function of contact time and the length of the molecular structure of the molecule to be oxidised.
Ionisation provides companies with a low cost, small footprint solution for treating high volume airflows where activated carbon would be too expensive to operate and biofilters too large to squeeze into a confined site. Not only that but it also provides a clean working environment for operators – maybe not Alpine, but the air around is substantially improved to the extent some have gone as far as to describe it as “pleasant”.
Case studies
Recently CSO Technik was approached to design, supply, install and commission an odour control solution for a 300,000 ton per annum municipal solids waste facility operating in the North East of England. Prior to CSO’s involvement the client had undergone significant growth and expansion, which had led to odour complaints. Following an initial site survey, a detail assessment of odour control options and a review of the functional and operational criteria, Terminodour™ was chosen as the most relevant and helpful solution. In March 2015 a Terminodour™ ionisation system was installed and the client continues to operate within permit and without complaint.
In addition the Terminodour™ ionisation system has been installed at a food waste anaerobic digestion facility in the North West of England where it has been employed to treat odour sources generated in the depackaging hall and the sludge screen room where high levels of ammonia were present. The system has worked very effectively and CSO has subsequently been awarded a further order to assist with a new plant currently under construction.
Protecting electronics
The flexibility of Terminodour™ has been a factor in its deployment in the protection of expensive control panels in wastewater treatment works. At Dwr Cymru /Welsh Water’s wastewater facility at Swansea, operatives noticed progressive corrosion of the internal circuit boards of control panels to the extent that the site was suffering from frequent breakdowns. Low levels of hydrogen sulphide were identified as the culprit and CSO Technik were engaged to eradicate the problem.
A mobile, floor-standing Terminodour™ Mini AHU (measuring approx. 670mm x 670mm x 670 was installed shortly afterwards. The system will help prevent the sulphuric acid-related corrosion and minimise operational and maintenance costs.