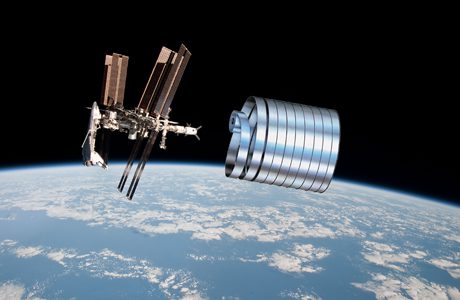
Having received an enquiry from the Spacefaring Institute™ LLC about large scale LNG storage tanks, Lipp UK was surprised to also be quizzed about the suitability of the Lipp double fold spiral seam tank construction method for actually building tanks in space…
As it turns out there are some inherent advantages to a rolled construction versus welded construction for use in space. Mike Snead, President of the Spacefaring Institute™ LLC made the initial enquiry and takes up the story.
“We are investigating the on-orbit fabrication of large space structures as part of an integrated spacefaring logistics infrastructure. These would likely not be pressurized, but would serve as secondary micrometeoroid protection layers surrounding the primary pressure hull or for use as space hangars.”
The project calls for Mike to investigate how a container with a diameter in the order of 10 meters with lengths up to 100 meters would be constructed. The ability to fabricate these from components using fairly simple equipment without the need for welding is attractive*.
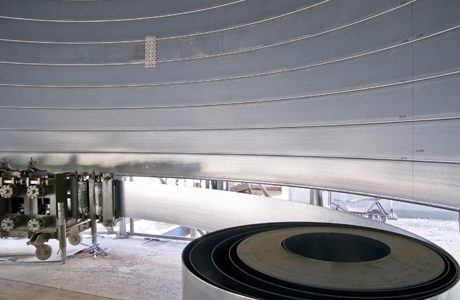
The Lipp double fold system creates a tank that has its own structural rigidity built-in. The tank is formed from rolls of layered material, a strong galvanised exterior material called Verinox, a boundary layer and a stainless steel lining with a smooth polished surface. The edges are folded over twice as the tank is cold rolled in a spiral, this creates a gas tight seal and a strong supporting ridge that runs around the outside of the tank.
The forming rollers are currently hydraulically powered, but could feasibility be driven by compact servo motors. Each set of tooling can be used to construct many tanks and power can be supplied from solar arrays, so no need to constantly transport gas tanks or welding supplies.
Manuel Lipp, the current MD of Lipp GmbH comments, “We supply Lipp tanks to hundreds of applications around the world that vary from salt water containment for fisheries to grain silos, gas storage and a large number of anaerobic digestion plants for slurry storage and as bio reactor vessels. They are popular because they are zero maintenance, they don’t leak and they are fast to erect and can be constructed with minimal work done at heights – we have never before been asked about providing a micro meteorite shield for use in space though!”
The project is a research and feasibility study at the moment, but the Lipp double fold, cold rolled tank construction method is technically still in the running for both large scale LNG storage and a space dock shielding system. Sci-Fi fans will be disappointed that putting the ‘shields’ up will be a bit slower than it is in Star Trek and Star Wars, but it is a step closer to actually happening.
Note: The hazards of welding in space.
Although the Russian Soyuz 6 mission demonstrated that multiple welding processes could work in space back in 1969 and NASA tends to now favour lasers, the Russian experiments also illustrated the risks and complications. The structure, composition and quality of a weld is dependent on the distribution of temperature and materials in the weld pool, which is difficult to control with no gravity. High temperatures and weld spatter are also highly dangerous, as the intrepid Russian cosmonauts found out when they nearly melted through the hull of the space station during the test.