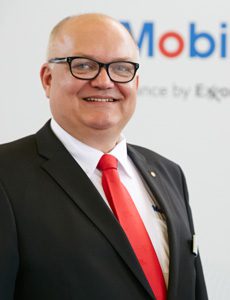
Jarmo Vihersalo of ExxonMobil offers an overview of biogas generation, and some thoughts on running engines to optimise performance, an area where his own firm offers expertise.
Advances in technology have expanded the availability of energy supplies to help meet increasing global demand. Coupled with the world’s aim to reduce emissions, countries are now actively turning to unconventional sources of energy.
One such source is biomass produced from agricultural waste. This can take the form of straw, leaves, roots, waste wood and animal husbandry waste. As biomass energy can come in many forms, it can also be treated and converted to energy in many different ways – by burning, through fermentation and distillation, or using a gasifier. Due to its wide availability and renewable nature, this type of waste is becoming a very attractive energy resource.
Whilst converting this waste found on farmland to gas marks an important time for the power sector it does raise some challenges for operators. This article explores the challenges posed by these new gases and the importance of the right lubricant in maintaining performance and reliable engine operation.
Europe is an important energy from waste market with Germany leading the way in biogas production with almost 8,000 biogas plants. In 2014, more than 26 billion kWh of electricity was generated from these plants and the country employs 41,000 people into the industry.
Other European countries are also contributing to the development and production of biogas – the UK, Italy, France and the Netherlands are all important markets. Italy is ranked as the second largest producer in Europe with 1,200 plants spread across the country, whilst in the UK there are currently just 153 active biogas and anaerobic digestion plants. However, this could be set to rise as the UK’s gas transmission system operator (TSO) believes biomethane could account for 10% of the country’s gas demand in year to come.
As the market continues to grow, more and more gas engines are now operating on this gas produced from waste to generate renewable energy.
Is biomass energy viable?
Using this waste to generate power has many advantages. Biomass energy from the likes of wood, crops and agricultural residue can help reduce excess waste, as well as reduce the emissions released into the air during the normal breakdown of this waste.
Although there are many advantages of generating energy from agricultural waste, there are several aspects to consider when used in gas engines.
One of the biggest demands with biomass-fired plants is in handling and pre-processing the fuel. As some biomass waste is produced from wood chips, which has a moisture content of 40 to 55%, the biomass needs to be dried before combusting or gasifying it to help improve the overall process efficiency but it may not be economically viable in some cases.
Another key challenge with biomass is its architecture. Chemical agents are often used to protect crops from disease, pests and weeds and the use of fertilizers can mean there are levels of nitrous oxide present in the gas.
An engine running on gas with nitrous oxide content needs to be burned at a higher rate and can impact the reliability and longevity of an engine. The engine is placed under great stress and can lead to major engine damage, such as cracked or destroyed pistons.
Gases with high levels of methane can also create difficulties for engine operators. Residuals of unburned methane in the exhaust gas, referred to as a ‘methane slip’, can worsen the overall impact on greenhouse gases, fuel consumption and operation costs.
These gases can also contain high levels of hydroden sulphide, which can pose major difficulties for engine operators. When biogas is burnt in a gas engine hydrogen sulphide can condense with water to produce sulphuric acid. If this sulphuric acid is not neutralised and accumulates, engines are at risk of accelerated corrosion and component failure.
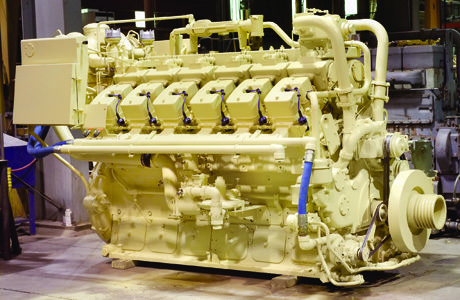
Optimising performance
When generating power from alternative energy sources, special attention needs to be taken to help maximise productivity and reduce maintenance costs – due to the varying make up of these gases. Original Equipment Manufacturers (OEMs) tailor engine components such as the bearings, cylinder head and crank case to withstand the corrosion caused by these gases but thought also needs to be given to the lubricant selected.
One factor to consider when selecting a lubricant for an engine running on biogas that contains hydrogen sulphide is the lubricant’s total base number (TBN). This identifies its acid neutralising capacity and alkaline additives used in higher TBN lubricants can help protect engines by absorbing sulphuric acid and neutralising its corrosive properties. As a result, component and equipment life can be extended, reducing the risk of unscheduled downtime and engine failure. Higher TBN oils also perform for longer in biogas engines, compared to lower TBN lubricants which degrade more quickly, reducing oil drain intervals.
Extending oil drain intervals can prolong engine life, help reduce maintenance costs and improve productivity. However, engines running on biomass waste typically have shorter oil drain intervals when compared to traditional gas. The chemical make-up, engine type, load and maintenance practices can all impact oil life.
ExxonMobil’s gas engine oil, Mobil Pegasus™ 605 Ultra 40, has been designed specifically to help optimise the performance of engines running on gases derived from biomass waste and landfill. Mobil Pegasus 605 Ultra 40 can help double oil drain intervals , which results in more reliable power production.
Along with outstanding anti-wear and anti-scuff performance, Mobil Pegasus 605 Ultra 40 offers exceptional carbon and varnish deposit control. This can help alleviate the impact of nitrous oxide, methane and chemical agents, which can deteriorate engines.
During extensive field tests conducted on a customer’s engine in Auckland, New Zealand, Mobil Pegasus™ 605 Ultra 40 showed its ability to improve engine cleanliness and prevent scuffing. Over an 18,000-hour test period, Mobil Pegasus 605 Ultra 40 more than doubled the engine’s oil drain intervals from 300 hours to 1,000 hours.
Following the product’s performance, the customer now uses Mobil Pegasus 605 Ultra 40 in all of its engines on site.
To help optimise performance, it is recommended that operators carry out regular monitoring of oil equipment. ExxonMobil’s used oil analysis programme, Signum℠, is an online system for maintenance professionals wanting to extend equipment component and lubricant life. Regular monitoring can provide early warning signs of contamination and minimise unscheduled maintenance.
To help reduce the dependency on fossil fuels, governments and operators need to look to alternative sources to keep up with the growing demand for energy and to help comply with increasing emissions.
Being able to manage varying gas qualities and higher specific engine outputs – whilst still delivering excellent reliability – will be the main challenges in the coming years. Operators will need to ensure the lubricant they choose can help mitigate the threats these gases can pose to engine operation and not hinder performance. With these new challenges, the latest advancements in lubrication will become more important than ever to help operators run reliable and efficient operations.