Industrial pollution and odour control specialist Simdean Group is offering a new plasma-based hazardous waste destruction system that has been developed for the pharmaceutical, oil, chemical and gas industries.
The system provides an alternative to incineration and landfill, the only options currently available for some types of waste. Both are controversial, being contested on both environmental and health grounds.
High levels of dioxins are present in the ash that is left after hazardous waste has been incinerated: polychlorinated dibenzodioxins (PCDDs), polychlorinated dibenzofurans (PCDFs) and polychlorinated biphenyls (PCBs).
These dioxins, which are environmental pollutants and a health risk, are formed not from a single compound but a mixture of different constituents that combine during high level combustion. The ash containing the dioxins is either transported to treatment plants or sent for landfill. A proportion of the dioxins also escapes into the environment via exhaust gases from the incineration plant.
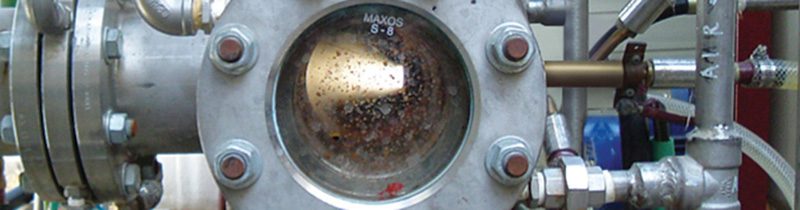
The new plasma system uses a novel technology that completely eliminates even the most concentrated hazardous waste, avoiding all issues and problems associated with incineration and landfill whilst providing a significant cost advantage over both of these methods of disposal.
The plasma technology
The company behind the patented plasma system – Environmental Systems and Treatment (EST) – was established in Israel in 2004 by a team of scientists and engineers. The team worked for six years on the technology before a commercial launch in 2010. The system uses extremely high temperatures (2000°C – 4500°C) to destroy a wide range of waste, with the constituent atoms being transformed into a non-hazardous ionised gas for emission to the atmosphere.
In some cases this material is also used as a basis for separate commercial products. The system is equally effective in treating wastes in the form of liquids, slurries or contaminated gases including halogenated waste and halogen acids.
The plasma installation is capable of integrating into the client’s production line, eliminating the need to transport or store waste products – an undertaking that is complicated and costly from both a financial and environmental point of view.
The process, which can easily be modified and calibrated to suit most production lines, is safe, user-friendly and simple to operate. Emissions from the system process comply with all international standards and regulations.
System overview
The system’s technology consists of four parts.
• Plasma reactor: decomposition of the waste by the plasma stream
• Cooling system: rapid cooling (quench system) of the output gaseous mixture. This prevents the formation of undesirable by-products such as dioxins and NOx
• Main scrubbing system: additional cooling of the gaseous mixture from 450°C to 80°C and main absorption of the halogen acids by process water
• Ecological scrubbing system: additional cleaning of the exit gas so that any emissions to the atmosphere are non-hazardous and meet environmental regulations
The plasma process
• The waste stream is treated by the plasma stream generated in the reactor. The high temperature in the plasma field can be adjusted depending on the type of chemical waste
• The extreme temperature instantaneously disintegrates the waste material, even breaking the covalent bonds within molecules, leaving only the constituent atoms. High temperature plasma is generated by initiating a powerful electrical discharge into air or other gas, such as nitrogen, argon and/or steam
• The hot gas mixture undergoes a rapid cooling phase in order to prevent formation of non-desirable compounds such as dioxins, furans and NOx
• Output products include water, CO2 and halogen acids (in the case of halogenated waste treatment). These products are fed into a scrubbing system, where they undergo absorption of the halogen acids and additional cooling
• The gas stream is recovered by the ecological scrubbing system. The exit gas is clean so that any emissions to the atmosphere are non-hazardous and meet all environmental regulations
The types of waste for which this method is suitable include hazardous organic waste, toxic waste, medical biochemical waste, halogenated waste, gaseous waste, liquid and suspension waste, industrial and laboratory solvent waste and PCBs
Downstream treatment
• The liquid and slurry wastes are supplied to the reactor by a special pump. They pass through an atomiser and go directly to a plasma jet generated by a DC non-transferred plasma torch.
• The interaction between the waste streams and the high temperature plasma jet destroys practically all thermo-stable components contained in the waste, gasifies organic compositions to CO2 and H2O and forms halogen acids.
• The products in the hot gas mixture are then exposed to rapid cooling (quenching), producing water vapour, CO2 and gaseous halogen acids.
• After quenching, the gas flow proceeds to a specific gas cleaning system, wherein the decomposition products are separated into liquid and gas phases. If required the acid gas solutions can be used as a separate reusable commercial product.
• Finally the exhaust gases (containing no organic components) are disposed via an exhaust stack, in accordance with local environmental standards.
For more on the technique see www.simdean.co.uk.