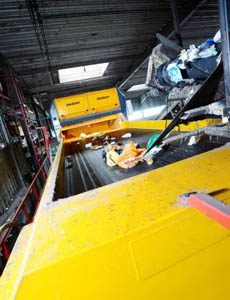
German waste disposal firm Hündgen says it has achieved important gains in recycling rates for plastic packaging with the help of the UniSort Black sorting system from Steinart, a specialist in magnet- and sensor-based sorting systems.
Plant manager at the family firm, Christian Hündgen, says they are focused on achieving as high a level of material purity as possible when sorting waste. “We concentrate more on the sorting depths than on high throughput rates. It ensures our customers in our region will remain loyal to us,” says Hündgen.
His firm worked with Steinart to examine the remaining losses from the sorting of lightweight plastic packaging. Whenever waste cannot be avoided, it’s best to recycle it back into the production process. And if it can’t be recycled, it can be incinerated to generate energy. To date, the materials left over after sorting the contents of Germany’s “yellow bag” recycling containers have been used as high-calorie substitute fuels for thermal recovery. However, there has remained a strong impetus to find ways of increasing the amount of material that can be recycled.
The UniSort Black system was released earlier in 2016 and incorporates an imaging technology able to distinguish and sort bits of black plastic, which normally elude detection using the IR sensors of traditional optical sorting equipment. It can sort all black plastics out of the flow of materials, and can also sort out plastics that have a NIR-specifiable spectrum (such as PE, PP and PS).
Hündgen were impressed with the system, says Steinart, having examined its performance at a test centre. They were also attracted by the provision of remote maintenance, ensuring rapid assistance when making adjustments.
Waste disposal firm’s processing stages
In order to prepare materials for recycling, Hündgen separates them according to grain size. The fraction of material to be sorted with grain sizes of 60–200 mm has the greatest sorting depth. The materials go through a number of stages, involving processing steps that use overbelt magnets, Steinert NES eddy current separators and Steinert NIR sorting equipment. Until recently, the process ended here and the material left over was used as substitute fuel for thermal recovery, in cement plants, for example.
However, Hündgen decided to add another sorting step after testing UniSort Black. “UniSort Black not only enabled us to offer a more flexible range of services for our customers, but to report higher sorting rates to the operators of the dual recycling system,” says Hündgen. This increased the plastics yield from the residual fraction and allowed the materials to be reintegrated into the material flow and recycled. “It also makes it easier for us to achieve the contractually agreed-upon sorting rates, to reduce incineration costs and, last but not least, to acquire additional materials by extracting polyolefins (PO) in the form of bottles made of PE and PP,” says Christian Hündgen.