Over the past two decades, the value of sludge to the wastewater treatment sector has been turned on its head, transforming it from an unavoidable and costly waste by-product into black gold – a business opportunity to add value while achieving vital energy and carbon reductions. Keith Hutchings, senior market development engineer with Hydro International, argues that, in order to deliver true value, the sludge business case should not just be the concern of accountants but also engineers.
To be fully ready to seize the spoils from sludge, UK water companies need to develop strategies that take business planning one step further and ensure pre-treatment processes are optimised to ensure maximum value is extracted.
Until relatively recently, sewage sludge was simply an unwelcome by-product of wastewater treatment. Culturally and historically it was the dirty end of the process and management focused on minimising the handling and cost implications.
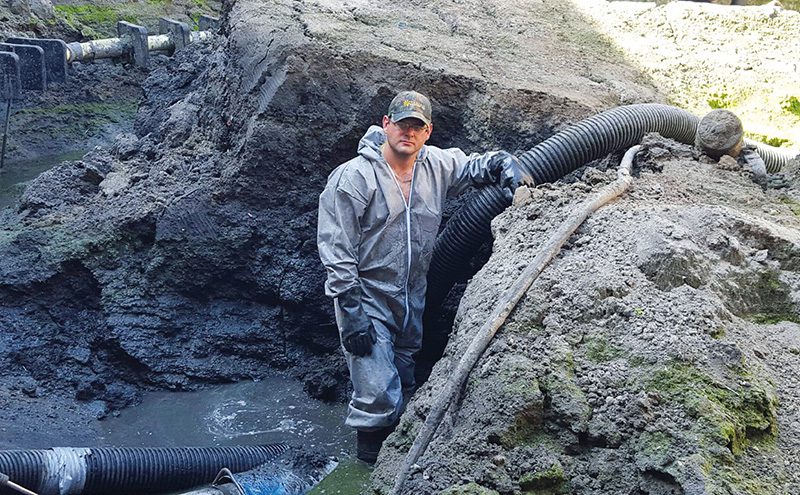
By contrast, in other parts of domestic municipal waste recycling, as well as in heavy industry, we have been very used to viewing waste reclamation as a value-added activity. Frameworks are in place that support synergistic business streams through recycling and re-use. So, why should the wastewater industry be any different?
Two distinct drivers are now making change happen in the municipal water sector. The industry is estimated to use up to 3% of the UK’s total electricity and to contribute 0.7% of total greenhouse gas emissions, so electricity generation is a major target for cost reduction – not only to please the regulator and offset operating costs, but also to meet the UK’s Carbon Reduction Commitment. Wastewater treatment is highly energy-intensive, with 50% to 65% being consumed by the aeration process alone on a typical activated sludge treatment plant. Wastewater treatment is, therefore, a front line process in the battle to meet national carbon reduction commitments.
At the same time, rapid advances in technology have opened up new opportunities for renewable energy generation. The industry has already invested significantly in reclaiming energy through dry sludge incineration and Combined Heat and Power schemes. Now advances in Anaerobic Digestion (AD) technologies have transformed energy reclamation opportunities through biogas generation.
The use of AD is not only expanding rapidly among municipal wastewater treatment operators, but also among industrial sludge producers, for example in food and drink manufacturing, as well as in agriculture.
As part of its Water 2020 reforms, Ofwat has fired the starting gun on the commercialisation of the sludge market in the UK, promising new opportunities for UK water companies to make money from sludge. This is likely to include looking for economies of scale by combining sludge treatment across their boundaries, as well as potential collaboration with the private sector to maximise the opportunities for renewable energy generation available through AD.
The more astute water company mandarins will be making an early start on developing their business strategies for sludge. As they set up their spreadsheets, they would be well advised to take their analysis beyond a business formation and pricing strategy, if they want to make a complete success of it.
The UK water sector is also targeted by the regulator to adjust its business and spending priorities towards a Totex (Total Expenditure) model with a greater focus on optimising through-life operating efficiency and maintenance.
Energy efficiency
So, there is much to be gained by hunting down the ‘hidden’ energy-eaters. To begin with, there would be little point in any operator looking to make money from sludge if existing processes remained energy inefficient.
In the US, operators are already talking about aiming to be energy or carbon neutral. In the UK, Yorkshire Water has just announced plans for a new £72million sludge treatment facility at Knostrop and the water company wants to recycle 94% of its sludge into energy by 2020. Ofwat has called for greater innovation in generating energy through sludge.
Producing a quality fuel
In order to optimise energy recovery, whether for incineration or AD, operators are looking at ways to create a fuel with optimum solids content and a high calorific value. In particular, operators are beginning to look at sludge pre-treatment processes to produce good quality sludge to feed the AD process. The use of thermal hydrolysis to pre-treat the sludge, sometimes known as the Cambi process, is now reported to be used by a dozen or so UK wastewater treatment operators. Its use is also growing rapidly the US.
Digestate quality
Digestate is the by-product of the AD process usually sold on as fertiliser. Looking to make the most of digestate, so that it delivers a quality product, depends on thorough optimisation of treatment processes, to ensure, for example, that the resulting product does not contain high volumes of useless, inert materials such as grit or plastics.
Sludge handling
Even at the earliest stages of mechanical handling in the pre-treatment and primary settlement phases, Hydro International’s customers have been working with us for some time to optimise the throughput of sludge as early as possible in the treatment chain. The growing use of Zickert® sludge scraping technology for example, has helped major UK water companies, including Thames Water, to deliver sludge efficiently for energy recovery schemes.
Equally, our technologies for screening and dewatering such as the Hydro-Sludge™ Screen can be used to remove and compact solids to provide sludge with higher energy value for incineration or reduce solids handling costs as part of the sludge pre-treatment process.
Grit removal
However, operators can perhaps make greatest gains in optimising their processes for energy recovery by looking at their grit removal systems.
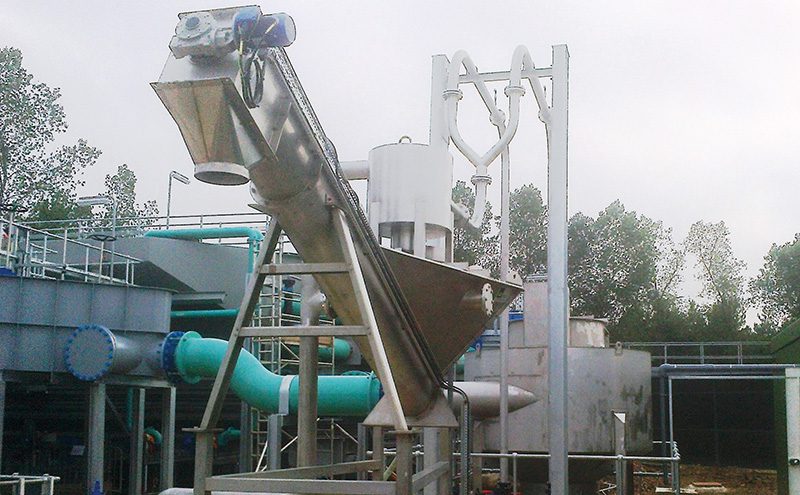
Energy studies at wastewater treatment plants indicate that for every 1% of grit that bypasses the inlet works and into downstream processes, 1% more electricity is needed. In the activated sludge process, grit build-up in tanks and channels, particularly in the aeration process, can dramatically reduce energy efficiency to make biological processes less effective and to clog up aeration blowers. More electricity is needed to compensate for these less efficient processes and to pump that extra grit around the plant.
At Hydro International, we have worked with more than 400 treatment plants over more than 30 years to apply our grit removal technologies and target more, finer, grit at the inlet works. Most real-world wastewater grit is smaller and lighter than the hypothetical standard against which conventional equipment is designed.
Many treatment plants are already experiencing the process, operating and maintenance efficiencies gained by targeting to remove 95% of all grit 75 microns and greater from raw incoming waters after mechanical screening. We call this approach Advanced Grit Management®.
Sludge treatment
Grit in sewage sludge used in the AD process is also a matter of concern. Operators that overlook the grit content of their sludge prior to AD are shooting themselves in the foot. According to research published in a 2010 report, grit and rag could account for up to 40% of the effective treatment capacity in a digester.

Moreover, especially in the UK, sludge is frequently transported from smaller plants to sludge treatment centres, from where it could be used as a feedstock for AD. Indeed, a significant amount of imported sludge is injected into the treatment chain downstream of the headworks. This leaves the door wide open for grit deposition in anaerobic digesters.
So, alongside targeting fine grit removal at the headworks, operators should be looking to optimise their sludge screening, dewatering and degritting processes at treatment centres.
For example, Anglian Water upgraded its sludge treatment operations to support its Special Projects Biosolids Programme as part of its AMP5 capital investment plans with the aim of processing at least 80% of its sludge output by advanced anaerobic digestion by the end of 2015.
Anglian has around 75 Hydro-Sludge™ Screen units installed across the East of England to ensure effective and efficient screening procedures to protect equipment and help optimise sludge output. The equipment protects downstream equipment such as pumps, heat exchangers and anaerobic digesters from difficult inclusions such as rag which evade mechanical screening.
Operators also need to consider how to optimise processes such as thermal hydrolysis through effective sludge screening and degritting. In the US, for example, we are increasingly being approached to install the Hydro-Sludge Screen to work alongside new investment in Cambi systems, especially for larger operators.
Optimising sludge treatment processes to minimise energy consumption and deliver sludge of the right quality needs to be considered by any operator keen to explore value-added opportunities from sludge.
Just as you wouldn’t fill your car with dirty fuel, you need to ensure good quality sludge as the starting point for energy-recovery: a process that starts right at the beginning of the treatment chain.