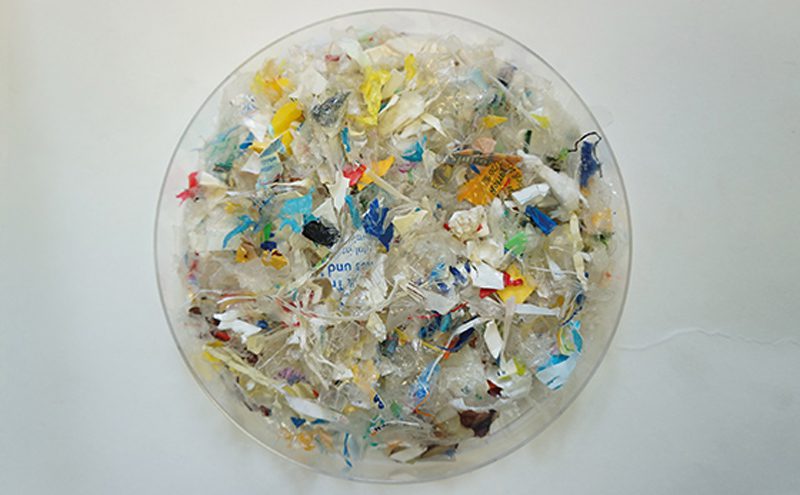
Last year Austrian plastic packaging and recycling specialist Starlinger introduced its technology for odour reduction in post-consumer plastic recycling, and since then it has been in high demand, says the firm. One customer has already ordered its second recycling system equipped with the technology.
Paul Niedl, Commercial Head of Starlinger recycling technology, said: “Our three-step procedure eliminates even deeply embedded odours. This gives our customers completely new application opportunities for their regranulate”. He said recent months have revealed a hunger in the market for this kind of solution.
Post-consumer plastic scrap often contains migrated substances from food, cosmetics or cleaners, which cause an unpleasant smell during the recycling process. But monomers, the residues from oxidation or hydrolysis, as well as decomposition products (VOCs) can be the reason for unwanted smells in recycled granulate too.
Depending on the polymer type, the source or type of the odour, as well as the odour’s intensity, and the specifications of the produced regranulate, Starlinger can adapt its recycling and odour reduction process according to the needs of the recycler. It basically consists of three stages: material preparation, degassing, and post-treatment.
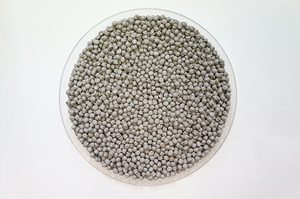
– Material preparation: the SMART feeder heats and homogenises the input material until the ideal operating point is reached. Highly volatile odours are already extracted during this process.
– Degassing: the C-VAC degassing module after the extruder increases the melt surface by 300%, thus achieving an extremely high degassing efficiency. This results in the permanent removal of deeply embedded odours.
– Post-treatment: The odour extraction unit at the end of the process gives the regranulate the finishing touches. Here, the most persistent odours are reliably extracted and removed permanently.
With Starlinger’s odour reduction technology, recyclers of post-consumer plastic scrap have the opportunity to turn their input material into a high-grade secondary resource. The firm says the excellent and homogenous regranulate quality resulting from the process, and its permanent odour reduction, make possible 100% reuse levels with the regranulate.