Pollution solutions provider CSO Technik was recently approached by Morgan Sindall Grontmij, working on behalf of Yorkshire Water to assist with an odour problem at the Toll House Pumping Station. The pumping station is located on the seafront on Marine Drive and just a few hundred yards from Scarborough Harbour and tourist attractions.
The site presented two principal challenges:
1. An odour target of 2 OUe/m3 at the site boundary which is literally the walls of the pumping station
2. The limited access and availability of space to install and locate the odour control system
The pumping station at Toll House was originally completed in 2014 as part of Yorkshire Water’s £26 million Scarborough Revised Bathing Water Directive scheme. The pumping station includes a 20m diameter x 35m deep storage shaft with a volume of 6,786m3. Odour problems became apparent after completion and CSO were contacted to assist in resolving the issue and odour generation was subsequently measured as being in the region of 200 OUe/m2/s.
The lack of space within the pumping station and on land outside of the pumping station was the first significant challenge to overcome by CSO’s designers. The odour control system would need to be installed within the building envelope due to external space limitations. However internal space was also very limited and effectively ruled out any large footprint solution such as a Chemical scrubbing or Biofiltration. The smallest footprint technology that CSO supply is the Terminodour™ Ionisation process. Normally the system is used without any additional abatement stages, but given the 2 OUe/m3 at the boundary performance target it would also need a polishing activated carbon stage to ensure compliance at this very sensitive site with immediate receptors.
Terminodour™ is CSO Technik’s low voltage oxidation and ionisation system, technology which has now been granted Best Available Technology (BAT) status for odour abatement in the latest drafts of BREF documentation for the Waste and Waste Water industries.
CSO’s design was based on delivering ionised air directly into the wet well where it would oxidise odours, which had been identified as being H2S primarily. During a storm event the deep shaft wet well fills and the odour emitted meets the blanket of ionised air within the tank and the oxidation reaction commences. As the tank fills air is also extracted from the tank and is fed via a range of ductwork into the activated carbon system which would provide a final polish to any residual odours not oxidised by the Terminodour™ system, prior to emission to atmosphere.
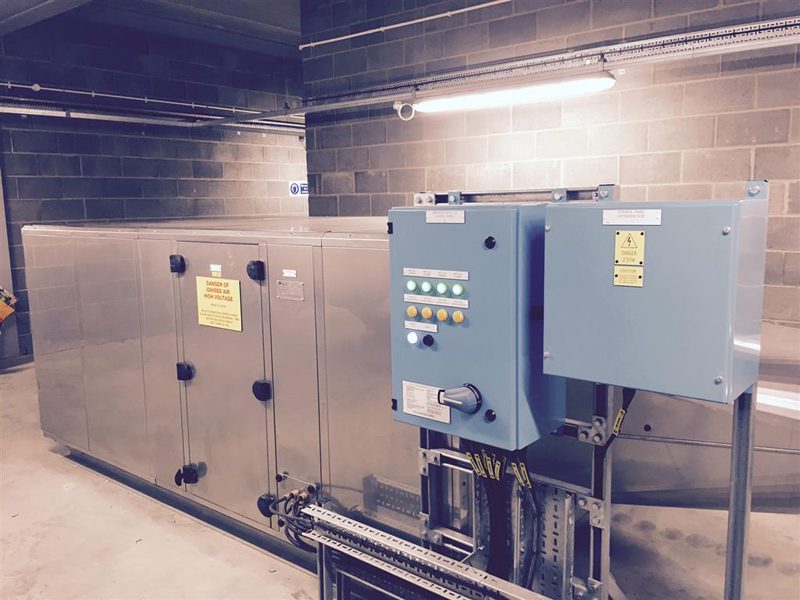
To minimise the size of the Terminodour™ air handling unit (AHU), the standard module sizes were dispensed with and a purpose-built model was designed to fit into the available space. The specially designed AHU houses a filter section for particulate removal, fan and the plasma reaction chamber with its ionising modules. Due to the close proximity of the sea wall and the potential for salt and sand ingress a special filter was included within the design. The AHU unit measured just 2865 x 1910 x 1155mm high. Low energy consumption is another benefit of this particular system and the total power consumption is less than 3.0 kW.
The activated Carbon system was based on a cartridge system to allow easy access to remove and replace spent carbon in the enclosed environment. The carbon filter housing measures just 1000 x 1900 x 1650mm high. The carbon filter is linked to the wet well by a range of uPVC ductwork and duty/standby extraction fans with an extraction capability of 2,350 l/s. The treated air is emitted via a stack.
Normally both the Terminodour™ unit and activated carbon system are supplied pre- assembled to minimise site installation time. However, because of the limited space within and access to the building both the carbon system and the Terminodour™ system were supplied only part assembled for final assembly on site.
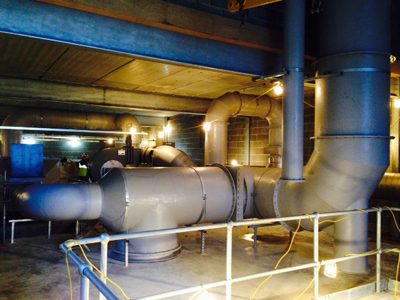
Post installation performance monitoring was undertaken by an independent third party which the system passed.
CSO Technik have a great deal of experience in designing odour control systems where the available footprint is severely limited. Recently CSO were awarded three major schemes for Terminodour™ in the waste to energy sector where the standard biofilter solution would have taken up more space than was available. Normally a biofilter will require 1 m3 of media for every 100m3 of air treated, therefore a system with an extraction rate of 40,000 m3/hr will require 400 m3 of media. It is advisable not to exceed a media height of 2m so the footprint would be circa 200 m2 excluding fans and ductwork. A Terminodour™ system for the same treated air volume will require less than 20m2 making it the ideal odour abatement solution for applications with significant space constraints.