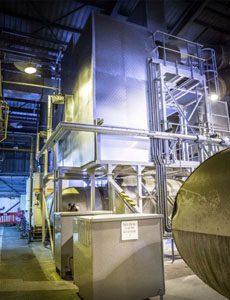
Best practice for business dictates that ways to improve operational efficiency should be constantly sought out, says Neil English, Managing Director of waste heat recovery systems manufacturer ThermTech.
While the humble boiler became popular over 100 years ago, it remains a major energy consumer in many factories and other types of business, generating waste heat from the spent gases used to heat the water.
Luke Hall, Project Manager at ThermTech, supports the universal application of boiler economisers. “Using an economiser provides a guaranteed method of reducing fuel usage while providing the same boiler output, typically achieving 4% to 6% fuel saving with a return in investment between 6 to 18 months. Even if you are only concerned about the immediate economics, it still makes a lot of sense. We also frequently see monitoring figures before and after installation, so we know it works.”
Applying boiler economisers
In an industrial boiler system heat is usually considered ‘waste’ when it is below 100°C as it can’t be used in main processes for boiling, steam creation or sterilisation. This spent heat could be used for ambient heating of the factory or building, but its use is restricted to colder climates or during colder times of the year in temperate climates. Plus, installations to provide this type of heating are often large and costly.
A more useful alternative technology is to apply a boiler economiser. Spent heated gases from the outlet or flue of the boiler burner are returned to the inlet of the boiler to pre-warm the in-feed water, thus providing a higher inlet temperature to the boiler. This results in less fuel demand to reach a usable water heat. This technique is often used in modern domestic boilers but is not common for industry. Many industrial boiler systems are often older installations and awareness of this energy efficient technique as a retrofit option is not always known, therefore energy savings are looked for elsewhere.
How do economisers work?
Installed between the boiler outlet and the flue or chimney, economisers operate on the principle of heat exchange, salvaging boiler gases to pre-heat the boiler in-feed water. This reduces the energy required to heat the boiler feed water to operating temperature. Usually constructed from carbon steel, the economiser design incorporates finned tubes containing the boiler feed water running perpendicular to the flow of hot outlet gases. By heat transfer the flue gas temperature reduces as it increases the feed water temperature.
The extent to which the economiser pre-heats the feed water depends on the design of the economiser and existing boiler parameters. The key to efficient heat transfer rate however is the design of the finned tube surface, which needs to maximise total thermal contact with the hot gas.
Off-the-shelf or custom built economisers
Since every application is different, each economiser should be purpose built to achieve the best transfer efficiency for the boiler design and the way it operates. This may include minor changes to an existing design, which is common for some more traditional designs based on boilers that operate continuously at maximum flow rates. More modern designs with variable flow-rates however, will usually require something more specifically suited to the application.