RPC Bpi Recycled Products is the UK’s largest producer of refuse sacks, and the largest polythene recycler in Europe. Recently the firm achieved an ambitious zero waste to landfill target, accredited by Valpak. Here, the company offers some insight into how it was achieved
RPC Bpi Recycled Products now segregates 85% of its waste, ranging from damaged pallets to used ink rags, for reuse and recycling. At its Stroud site, waste management has become self-funding, due to rebates earned from recyclable materials and a reduction in waste management costs.
The company’s four UK sites, in Stroud, Heanor, Rhymney and Dumfries, receive 50,000 tonnes of scrap polythene each year; these are then recycled into high performance finished goods such as refuse sacks and Plaswood lumber.
The firm is one of just a few UK companies that can claim to offer a genuinely closed loop manufacturing business. It does not just produce recycled materials for re-sale; it reprocesses waste into useful, high quality products, managing the entire process in-house.
Incoming feedstock for the recycling and manufacturing process is polythene waste sourced from agricultural, retail and local authority sectors. A typical load consists of 98% polythene, plus contamination, which makes up as much as 70% of the company’s outgoing waste.
The company has been monitoring waste levels at its four sites since 2008, predominantly for general waste and hazardous waste, with metal, wood, paper and cardboard extracted for recycling.
Incoming material is placed onto a sorting belt. The majority is turned into plastic pellets, the beginning of the manufacturing process, with contamination removed at the start of the recycling process.
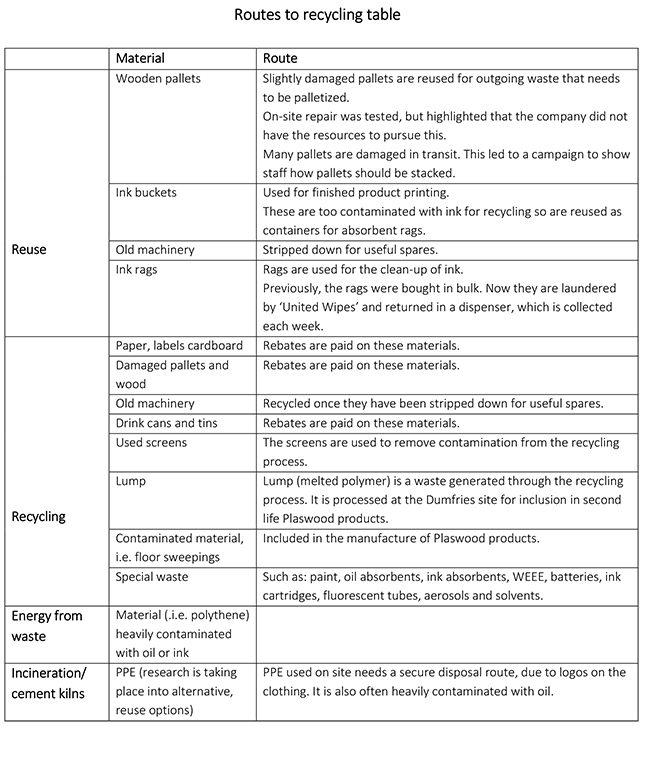
IMS Compliance Manager Daryl Winder said: “Sustainability underscores everything we do; both the products we manufacture and the way we manage our operations. We want to emphasise that the way we operate isn’t just a case of providing a plastic item which could potentially be polluting the environment. We’re trying to promote the idea of a circular economy, whereby everything we manufacture, after use, can be returned to us, recycled, and then start the process again.
We are also exploring ways to include lifecycle analysis and a carbon footprint on our product packaging. We hope that this will help our customers make ethical and sustainable choices.”
Since the Stroud site won a Green Apple Award for waste reduction in 2011 (for reducing general waste by 90% in three years, against a target of 5% year-on-year) the other sites emulated Stroud’s policies. By 2016 the waste reduction methods had resulted in zero waste going to landfill.
[box style=”0″]
Key strategies included:
• the introduction of a simple, colour-coded system to help staff identify different waste streams;
• reducing the number of general waste options. Large 40-yard general waste skips were replaced by two 1,000-litre bins and collected on a weekly basis. This not only resulted in a cost benefit, but also made it easier to monitor contents;
• daily checks and advice ensured that staff were segregating material for recycling; and
• although waste contracts were already in place, additional contracts have been negotiated, where existing suppliers were unable to accept certain waste streams for recycling. External contracts are now regularly reviewed to ensure best value.
[/box]
The company’s zero waste to landfill achievement is particularly significant due to the range of materials appearing as waste; these were often presented as contaminants in material arriving on site for processing.
In 2016, RPC Bpi Recycled Products was independently assessed and awarded ‘Zero Waste to Landfill’ accreditation by Valpak. The company has seen clear benefits, both economically, and environmentally.
Every April, waste company costs increase in line with rises in Landfill Tax. Options for negotiating a better price are limited, so the company’s strategy is to reduce general waste and increase recycling, which means receiving greater funds from rebates for recyclables which, in turn, help to offset the costs associated with general waste.

Since 2015, when the programme began, recycling has increased by 617 tonnes, while general waste costs have fallen.
Between 2015-16 the total cost of waste management contracts fell by over £15,000, while the cost of recycling fell by over £23,000.
• RPC-BPI Recycled Products is the largest recycler in Europe with the ability to recycle 70,000 tonnes of polythene waste each year.