AD plants house a complex biological environment and one that is still far from fully understood, though it must be managed carefully to maximise biogas yields. At July’s AD & Biogas show, a panel of experts shared opinions about getting the most from a plant, and making the best choices when setting it up or attempting to nudge its operation in the right direction. Envirotec reports.
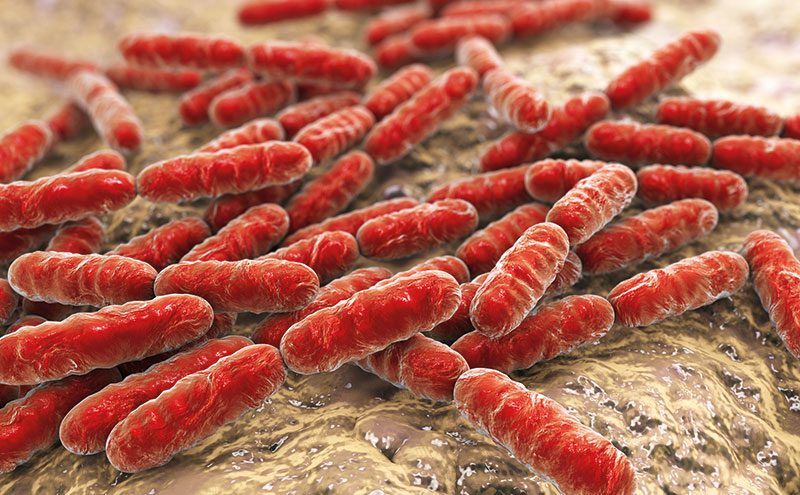
It might be relatively young as an industrial endeavour, but anaerobic digestion is a process we are all well acquainted with through our stomachs. And similarly, as several speakers were keen to point out, each AD plant is an individual, with performance and properties that depend on how it is fitted out. So many factors have a bearing on it, such as the size of the tank, whether or not it has stirrers, the types of feedstock, the specification of the retention tank, and so on.
The complexity can lead to mysterious process dysfunctions, which can be difficult to diagnose. One whose job it is to help is Dr Melanie Hecht, whose talk was titled “Protein-rich feedstocks: feed heaven or hell?” As a biogas process manager with Schaumann BioEnergy, she provides consultancy services for biogas plants – including advice in the event of an emergency.
A whole range of process dysfunctions land on her desk, it seemed, and Schaumann has developed formulas and biochemical tweaks that can be applied to suit. Trace element deficiency, for example, can be treated with the addition of bespoke nutrient mixtures. Similarly, for viscosity problems Schaumann has specific oil-enzyme mixtures that can be used to dose an ailing plant.
Trace elements are important for ensuring a high gas yield. With food waste, for example, it seems to be cobalt and selenium that get depleted easily, because these aren’t so prevalent in food.
Ammonia inhibition
Hecht was eager to talk about the problem of ammonia inhibition, whereby the presence of ammonia – while an essential nutrient for bacterial growth on the one hand – can, above certain concentrations, noticeably inhibit the activity of methanogenic bacteria. This is an issue that has been cropping up more and more of late. Partly it is down to the greater prevalence of enriched feedstocks, which contain high amounts of protein or uric acid. These feedstocks are popular given their ability to produce high gas yields at low cost.
The question of how to remedy ammonia inhibition calls for a clear understanding of what is happening, she said. Lowering the pH by adding acids seemed an obvious tactic but one she warned sternly against. For one thing, this could cause foaming – very disruptive to plant operation. These plants have a very strong ‘buffering’ system which helps keep the pH stable, and is very important for the bacteria, she said – drawing the analogy that pH is for bacteria a little like what oxygen is for us.
On ammonia inhibition, she illustrated with a sample taken from a plant in March 2016, and went through the kind of analysis she might perform. First, a look at the total acidity levels. In this case, 7.2g/L of acids definitely seemed like too much. “Next thing I’ll look at the single acids because they are a bit like symptom pin-pointers, they point you in the right direction,” she said, citing lines of enquiry that might come up at this point: is it micronutrient deficiency? Over-feeding? Or is it maybe – as in this case – high propionic acid concentrations? This seemingly pointed her in the direction of ammonia toxicity.
Reaching the conclusion that there is a lot of free ammonia in the digester, it’s time to ask the plant operator what temperature the process is running at. With a knowledge of the temperature she seemed able to calculate the amount of free ammonia.
In this example, it turned out the plant had an ammonia content of nearly 1g/L – very high. “Starting from 300mg I start to get nervous,” she said, explaining that, from 500mg upwards, you can be fairly sure the plant is suffering from ammonia inhibition. In this case, it isn’t possible to change the pH because of the need to maintain the high buffering capacity, but there is the option of changing the temperature, as the plant is operating at near-thermophilic conditions of 45ºC or so. By lowering the temperature very slowly, it was possible to bring the ammonia down to a level of 700mg.
Time to use a binder
The next option would be to try and change the feedstocks if possible – that would bring down the ammonium level even further. In the case being illustrated, Hecht said they used an ammonium binder to start with, “because this plant was severely inhibited” – you couldn’t change the pH, couldn’t initially change the feedstocks, and even lowering the temperature wasn’t enough. The binder is an ion exchanger with a high affinity for the positively charged ammonium (NH4+) ion. So it will bind it selectively and only release it later, such as when the digestate is being spread on a field. By using the binder, it was possible to bring down the pH, the total inorganic carbon, and the acid levels. The whole remedy took around three months, she said, “and that is not unusual – ammonia inhibition is a very severe inhibition, and it takes a while for a plant to recover,” she said, even if several remedial options are put into action.
At first, when the binder was used, ammonium actually went up to 6.64g/L, along with the dry matter content. It plateaued for a while before going down, without any change to the feedstock. “That’s a very good sign that the plant is starting degrading again, where the inhibition is being remedied,” she said, explaining that as ammonia is taken out of the system, the methanogenic bacteria recover and start working again.
Her own firm assists with plants where an ammonium binder is used as an emergency measure, and others where it is used continuously, to allow the continuous use of enriched feedstocks. Answering a question later in the session about the binder’s cost effectiveness, she said that “in comparison to [plant] downtime, the cost of the binder is pretty much negligible”. The binder also isn’t recovered, but is simply spread on the fields with the digestate, a preferable option as the ammonium remains bound until the very last moment.
There was also the question of how much ammonium should be present to justify the use of a binder. After all, it might take other useful things with it, trace elements and so on. Hecht said if you had an ammonium content as low as 1 or 1.5g/L then a binder would indeed cause these problems, but at levels of 4 or 5g/L or above, it wasn’t a problem.
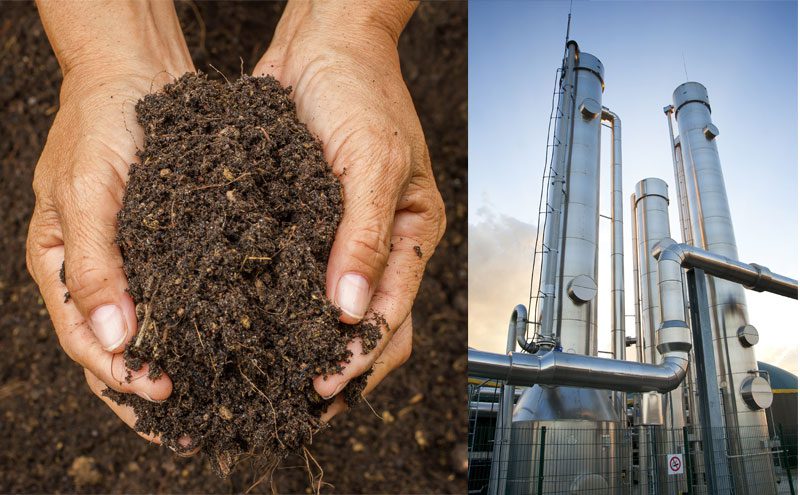
Feedstock choice
At any rate the choice of feedstock is clearly of central importance in determining the likely biogas yield from a plant, as Dr Phil Hobbs of Privileged Asset Finance explained. You might want to visit other plants to make sure you’ve got something that really works. Nowadays a feedstock contract can be an important hinge of the financial requirements for securing investment in a site, he said. You need to ensure the supply of a feedstock won’t be adversely affected by a change in weather conditions, for instance.
He also warned about certain types of feedstocks, where acidity might be an issue, and lead to foaming. Fruit juice, for example, where the molecules are very soluble. However, this kind of feedstock can also raise the biogas yield.
Nitrogen content is a factor to consider too. Ideally you want a carbon-to-nitrogen ratio of about 20:1 or 30:1, he said. This gives you an optimum level. If you start going to 80:1 by adding straw alone, for example, then you’ve got a nitrogen issue. You need nitrogen to build the cell walls and ensure an effective fertilizer is produced.
If you put a lot of new feedstock in, and it’s at a cold temperature, then you should expect your gas yield to drop temporarily as these plants don’t like temperature changes.
When changing or altering feedstocks, proceed slowly. It is also critical to monitor the process continuously, to understand what is happening with it.
In a later question Hecht also mentioned that certain feedstocks appear able to alleviate ammonia inhibition. Sugar beet, for example, is an interesting one in this regard. She said that sugar beet and maize – when used in the right ratio – also produce a higher gas yield than you would expect from either feedstock on its own. So there’s a lot of research that could be done in this direction, she said, “and it’s a really fascinating subject”.
Feedstock quality is a tricky area, said Hobbs, because there are so many elements to consider. As the crop gets older there will be a preponderance of lignin, a large polymer important in providing the structural properties of trees and plants. Methanogenic bacteria don’t like lignin, and can’t convert it. But on the other hand you need a certain amount of such biomass to ensure a high gas yield. So there’s a balance to be struck. One option is pre-treatment techniques.
Pre-treatment options
Mechanical pre-treatments are common, for instance, using techniques such as extrusion, maceration, different knife systems, and so on. “Generally speaking if you start getting below 0.5 cm,” said Hobbs, referring to feedstock particle sizes, “you’re in the right area for the bugs to be effective. The bigger the surface area of the material, the more bugs can get to it, to produce the enzymes that can break it down”.
Thermal pre-treatment is another option, and one that might seem attractive if the plant is receiving the RHI. “Thermophilic processes are brilliant,” he said. “What they do is dissolve the waxy layer on the outside of things like grasses and straws and enable the bacterial enzymes to get at the celluloses and hemicelluloses and break them down and convert them into sugars, ” he said.
Chemical pre-treatments and enzyme pre-treatments, on the other hand, are something that you’ve got to keep paying for, so might not provide the required economic return.
The type of bacteria will also have a bearing on gas yields. One of the panellists Sandra Esteves of the Wales Centre of Excellence for Anaerobic Digestion, gave a talk that dealt briefly with the different types of methanogenic bacteria, and the fact that some like to chew on acetic acid, others prefer hydrogen or carbon dioxide, and so on. So getting the right balance of bugs is an avenue towards plant optimisation, and Hobbs said there are a lot of research groups trying to figure this out.
The panel spent some of the session marvelling at the mysterious properties of bacteria. Hobbs mentioned the fact that in some cases micro-organisms appear to have a “memory” in that, if one set of organisms has in its past been fed a high proportion of protein, for example, then – even if it has since been changed to a high carbohydrate diet – it will retain an affinity for protein, and a noticeable ability to generate biogas from this material when it is returned to it.
He mentioned work at Exeter University, looking at how methanogenic bacteria populations evolve over time.
Digestate potential
Esteves said one of the neglected areas of AD at present is the digestate. “Not much is being done on the utilising of digestate and gaining value from that,” she said, referring to work where the digestate is used as a nutrient media for fermentation. So “there’s a lot of nice work that could be done to match different digestates from AD with different industries, such as fermentation or bio-refining”.
Process monitoring and control is also an important consideration. As Hobbs said, it is a 24/7 process, “and I think that if – for just a few thousand pounds – you can add 5 or 10% onto your biogas [yield] ╨ that is really the icing on the cake”, he said.
Esteves’s talk touched upon the challenges with process monitoring, making mention of a project she is involved with, using AI-based control strategies. This can get around difficulties such as, for example, if one sensor in the system is failing and giving you the wrong information. This could be dangerous if you are using some kind of on/off control system (i.e, ‘feed’, ‘don’t feed’), because it could result in the wrong control action.
One questioner wondered if there might become available a means of determining feedstock quality, in a fast and reliable way. Hobbs said that currently farmers send samples of their feedstocks for their livestock to analytical experts who use techniques like near-IR spectroscopy, scanning samples very quickly (in about 30s) referring the spectra to a reference library, which provides accurate results. One agricultural body has a reference library of manures, and information about the nutrients they contain.
What would be really interesting, he said, was if there was a means of looking at digestate and determining its properties. If there was a way of doing this quickly it would provide the basis for automated process control of digesters.
So there’s a lot we’d like to know about biogas plants, to make them operate better. Onlookers would have taken this as possibly the strongest message of the session.