Biogas upgrading specialist DMT Environmental Technology on a familiar AD bugbear: hydrogen sulphide
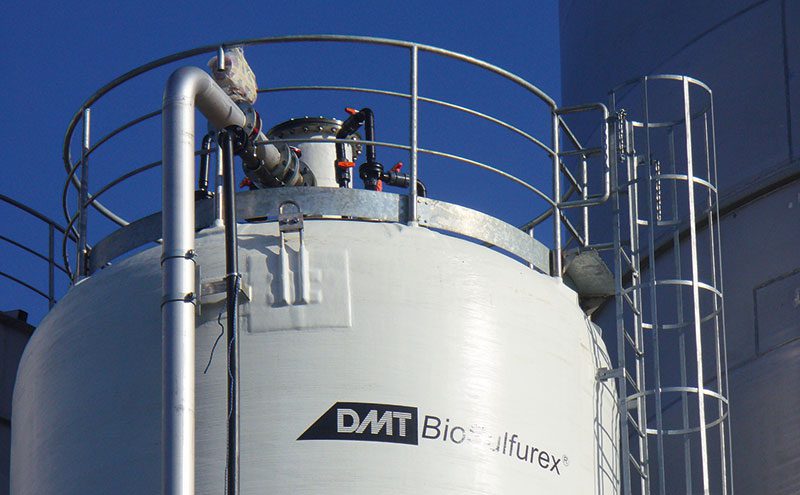
Developing an anaerobic digestion (AD) plant doesn’t come cheap. Costs range from £100,000 up to as much as £24m. When calculating their costings and potential ROI, developers often plan for a plant lifespan of 20 years, so it’s essential that plants are well maintained to avoid unexpected expense. This is particularly important as there are a number of things which can adversely affect a plant’s longevity, such as large deposits of grit, the absence of a pressure relief valve, foaming and process instability, for example. In addition, there is an invisible threat to AD plants which, if left untreated, can seriously impact performance, profit and plant lifespan – sulphide.
Sulphide inhibits the AD process
Biogas produced through the decomposition of organic matter contains hydrogen sulphide (H2S), a colourless, toxic gas which is one of the main inhibitors of micro-organic growth; if the bugs can’t get to work within the digester to break down the organic matter, then the volume of biogas produced per tonne of feedstock will be dramatically reduced, affecting an AD operator’s profit margins. This is particularly relevant for certain types of plants, as different feedstocks contain different levels of sulphates. Examples of feedstock rich in sulphur-containing proteins include cattle, pig and poultry manure, so on-farm plant operators should be especially vigilant.
In addition, there is a high sulphate content in wastewaters from the beer and beverage industry. And in the case of sewage AD plants, sulphates present in wastewater lead to the production of sulphide under anaerobic conditions. Concentrations above 6 mg/l of sulphate will start inhibiting the production of methane (methanogenesis) – above 320 mg/l and methanogenesis will be not be possible.
H2S also has a strong odour of rotten eggs. If it is not removed, this unpleasant smell is retained within the digestate (the nutrient-rich biofertiliser which remains at the end of the digestion process), causing offence to neighbouring communities and making the digestate impossible to sell to farmers and growers.
Sulphide reduces AD plant lifespan
The most damaging side effect of H2S though, is its ability to corrode essential plant equipment – pipes, compressors, storage tanks, engines, etc – and reduce the life of a CHP unit, the heart of any AD operation. The average lifetime of a CHP unit is around 60,000 hours. If it is operated without any desulphurisation technology, the unit will require maintenance after 20,000 hours of operation. However, the introduction of a step to remove H2S can increase uptime by 50 per cent to 30,0000 hours.
Diverse solutions
The AD industry encompasses a wide range of plant types and a ‘one size fits all’ approach should not be applied to desulphurisation. Influencing factors including feedstock type, site conditions, plant uptime, CAPEX and OPEX, and end use of the biogas, need to be assessed before introducing a desulphurisation process.
H2S can be removed in-situ during digestion by air injection or through the addition of iron salts/oxides. It can also be removed from the raw biogas by physical-chemical separation processes or biotechnological methods (or a combination of the two). For high concentrations of H2S, chemical scrubbers are usually recommended, while for biogas upgrading, activated carbon filters are typically used as a pre-treatment. For medium or high loads, alkaline scrubbers are preferred, while upgrading technologies based on physical absorption (such as water scrubbers or non-water sorbents) can simultaneously remove H2S and CO2, but usually require a pre-treatment to achieve low concentrations. Failing that, a post-treatment is required to remove H2S from the exhaust air.
Determining the ‘SSweet’ spot
As well as offering desulphurisation technologies, including a chemical process (Sulfurex® CR), a biological process (Sulfurex® BF), a biochemical process (Sulfurex® BR) and activated carbon for small loads, DMT has developed a system to help AD developers select the best suited desulphurisation technology for their plant. The Sulfurex Selection Work Expert Tool (SSweet) correlates the plant’s gas flow rate and inlet H2S concentration figures to identify the best suited technology from both a performance and financial standpoint. In addition to this, a tailor-made business case is generated by considering site-specific conditions (such as electricity price, water price, caustic price, discharge cost or labour cost), and uses a mathematical model to estimate the total cost of ownership.
By combining a pre-selection step with a tailor-made business case, the SSweet allows an AD plant operator to select the most suitable technology for their project from both a technical and financial standpoint, preserving the life of their plant – and their profit margins – for years to come.