Lyndex Recycling Systems, a supplier of high-end balers and waste recycling machinery, has launched a cloud-based data logging and diagnostic solution. It provides customers with easy access to essential equipment data and new levels of capability to monitor, manage and control operations and performance via a smartphone, tablet or PC, says the firm.
The online solution provides live real-time remote access to machine status and diagnostic information, including fault, service and inspection alerts, together with a range of production and operational data covering production figures, downtime, throughput, performance and other factors. These in turn can be exported for further analysis and reporting.
Information is presented through a series of management dashboards with graphical representations of equipment colour coded with live data values, plus run-time graphs, counters and key statistics, enabling customers to visualise operations, understand performance and improve management and control.
Doug Lord, Sales Manager at Lyndex Recycling Systems says: “Maturity across the waste sector and economic pressure is seeing a more analytical approach to business with an increased emphasis on data and reporting. While a number of recycling equipment suppliers claim remote diagnostic capabilities, this is the first real solution available. It offers improved engineering support to our customers from day one, mobile access for total flexibility and a range of management and operational insights to drive performance and control. No other system offers this level of sophistication.”
At-a-glance operational information for each machine provides accurate insight across a range of business parameters. This includes run-time graphs by month, week or 24 hours showing machine status and percentage activity, with countdown timers for next inspection, fault alarms and colour coded images to show machine production or idle status, oil temperature, motor condition, faults and material currently being processed.
For production managers this wealth of information cuts time and increases accuracy eliminating the need to manually log information or rely on machine operators to pass information. Operational issues can be more easily interpreted for example by viewing how many hours a machine is actively being fed material versus the number of hours switched on but not in production.
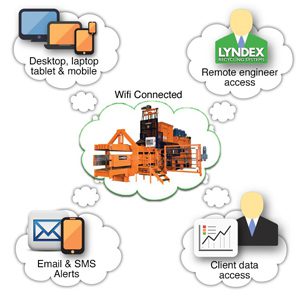
Commenting on the system, Craig Curtis, Director of CS Recycling and Board Director of the Recycling Association says: “In the first month of testing the baler we had access to Lyndex’s own cloud diagnostic system. Two weeks after buying the new Meggabite baler, we wanted to change the settings to improve throughput. I spoke Lyndex on the phone and in front of my eyes, I could see their technicians go deep into the software, make adjustments and just 5 minutes later the changes were made and the baler was ready to use.”
Curtis continued: “It was absolutely amazing. I was so impressed I straight away asked Lyndex to supply one to CS Recycling and we now use it for accurate productivity data. We’d heard of remote diagnostic systems, but this Lyndex system takes the technology to a whole other level.”
It means customers can analyse equipment performance, spot deviations from expected activity, calculate stock and production cost down to a single bale, measure performance by waste stream and optimise energy consumption. Weekly reports can be automatically generated and emailed to colleagues and higher management while data can be exported for further analysis.
Production data records running hours for each machine and total volume of bales produced, together with individual material breakdowns for different waste streams for example PAMS, mixed paper or coloured card. These are picked up automatically each time an operator selects a different material grade on the baler, using pre-set Lyndex ‘recipes’ to optimise performance. The system is completely flexible allowing any number of waste grades to be recorded.
Support and downtime issues are also significantly improved with the Lyndex Remote Assistance module a part of the package. This enables Lyndex engineering staff to connect directly to a customer’s machine to diagnose faults, with the ability to fix 95% of issues either by remotely changing settings on the machine, or by alerting the local operator to the issue.
Text or email alerts ensure alarms aren’t missed, cutting downtime that would otherwise be required waiting for an engineer to visit. In the event of breakdown the system can be used to diagnose problems more accurately so that service managers are accurately briefed and prepared with the right parts, rather than relying on ‘word of mouth’.
With more accurate servicing based on logged hours and fewer maintenance visits, the system also provides a long term diagnostic tool to monitor equipment health and machine upgrades and settings can also be simply changed remotely to improve performance.
Fully configurable and already in use at 10 customer sites across Europe, the Lyndex Cloud Data Logging Solution is available as an option across the latest generation of mid to high-end balers including the Meggabite baler range and in some cases can be retrofitted as an upgrade to earlier models.