The UK sewage sludge treatment sector is undergoing rapid change. Leslie Eaton of SEEPEX, a manufacturer of progressive cavity pumps, offers a view on where new pump developments fit into the picture
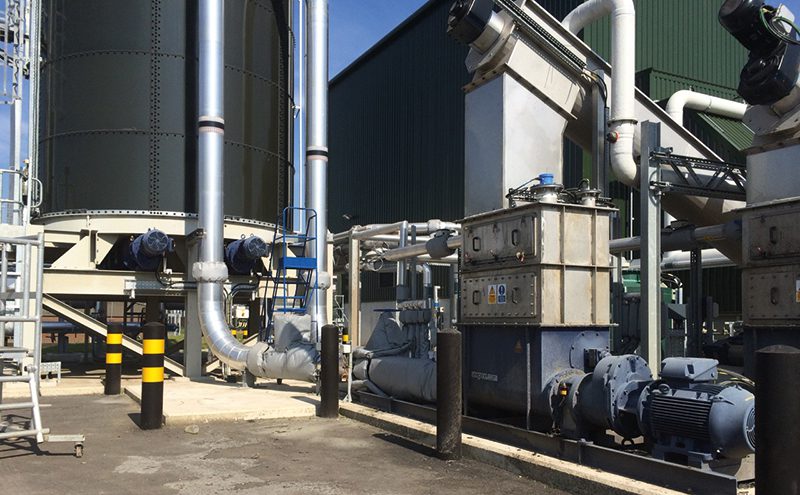
Energy generation from the anaerobic digestion of sewage sludge has reached 888 GWh, according to figures from the 2016 Digest of UK Energy Statistics – an increase of over 25 per cent since 2011. Yet over the same period the installed theoretical MWe capacity has grown by just nine per cent, with only 159 biogas plants using sewage sludge as a feedstock. How has the energy generated by the anaerobic digestion of sewage sludge increased so dramatically? And is the trend for efficiency improvements in the water sector set to continue?
Turning up the heat
One of the biggest changes to the treatment of sewage sludge in recent years is the use of high temperature heat treatment, of sludge, which sterilises the sludge and changes its rheological properties. This makes the sludge more biodegradable and enables the loading rates to the anaerobic digesters to be doubled, delivering a higher gas yield. A further benefit of the process is that the final sludge from the digester is pathogen free and can be easily dewatered, resulting in a more valuable final product for application to land.
Existing treatment practices
Currently, a significant proportion of sewage sludge is treated by water authorities in their own large, centralised treatment centres, which take dewatered sludge from their smaller satellite treatment works. Raw sewage can constitute up to 99 per cent water and the satellite sewage treatment processes work by removing this water and thickening the sludge using a series of steps involving both gravity settlement for primary effluent and mechanical thickening of secondary sludge. Thickened sludge is often dewatered at the point of production using a variety of equipment technologies to produce sludge with dry solids content (ds%) of between 18-35 per cent before transfer to the larger centres. The process of dewatering cuts the sludge volume and reduces transport costs – vital if economies of scale are to be realised. When dewatered sludge is received at a central processing plant it is mixed with indigenous sludge to produce the ideal ds% for energy generation and other onward processes.
Water 2020
However, the trend for water companies to treat only their own sludge is set to change as a result of the Water
2020 report, published by the regulator Ofwat, which is designed to kickstart a market for treated sewage sludge. Speaking at the 2016 UK AD & Biogas Conference, Ofwat’s Principal Engineer Alison Fergusson explained that the regulator hopes to encourage markets between operators in order to move sludge from a company where it’s expensive to treat, to one that is cheaper. Ofwat modelling suggests that if its proposed changes are implemented, around 30 per cent of all sludge could move between different water companies. The plans aim to make sludge a potentially valuable product, leading to more efficient treatment and greater energy generation.
Specifying pumps
While process optimisation, economies of scale and deregulation will all play a part in the continued increase in energy generation by the water industry, it is important not to overlook the importance of correct equipment selection. Pumps in particular are vital to the water sector’s continued success and a ‘one size fits all’ approach should not be applied. For all pumping applications, the correct pump selection will give the optimum return on investment so it is important that the pump is not treated as a standalone commodity. A thorough understanding of the product to be handled and the process requirements should be considered, with tailor-made packages often providing the best solution. Minimising the energy use of equipment is desirable, PC pumps compare well in this respect to other pump technologies, with their ability to maintain flow, even with varying pressures and variable sludge viscosities which is specifically important when feeding heat exchangers to ensure the most efficient heat transfer for heating the sludge. Integrating pumps with complementary equipment, such as special live bottom silos, boundary layer injection systems and back-mixing technology, together with intelligent control systems, is crucial for reliability, performance and cost efficiency. Sludge cake pumps are large so it is vital that they are efficient in use and have accessible wearing parts for ease of maintenance when required.
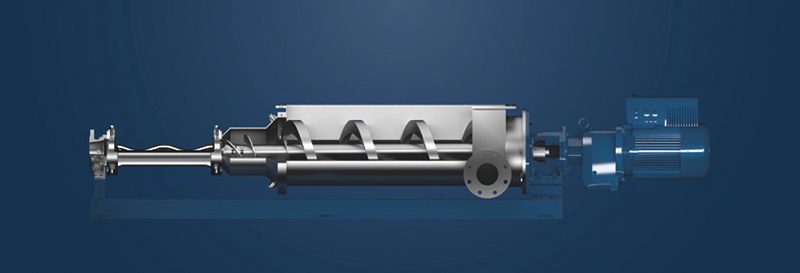
One utility’s quest for efficiency
Anglian Water is the largest water and water recycling company in the UK by geographical area, supplying over six million homes and business customers in the east of England with clean water and treatment services. During the AMP5 period, which ended in 2015, the company installed sludge reception centres and advanced energy generation using thermal hydrolysis at three locations within their area. It was important that these plants were as efficient as possible to provide the double advantages of reduced energy consumption and increased generation.
The utility installed SEEPEX progressive cavity (PC) pumps for efficient sludge transfer and mixing duties. PC pumps were chosen as they can handle both low and high viscosity products, can pump sludge with ds% up to 45 per cent, and are not hindered by solid particles. In addition, their good discharge pressure capabilities enable long distance pumping, and their non-pulsating flow characteristics make them a popular choice for many wastewater applications.
Open hopper pumps for high solids transfer (up to 30 per cent dry solids in this case) and liquid transfer pumps formed part of the package, while a visit to an existing sludge treatment plant demonstrated how efficiencies in installation could be achieved, removing the need for conveyors in parts of the process. This was achieved by using customised pumps fitted directly to silo outlets which could back-mix sludge cake with dilution liquid to the required ds% needed for energy generation. Integrated controls link the liquid addition and back-mixing silo pumps to ensure optimised mixing.
As well as lower capital costs, operating costs were reduced by using very small amounts of liquid injected constantly to the outlet of the pump. This produces a lubricating boundary layer around the sludge, reducing friction losses and hence operating pressure. The load on the pump is reduced and service intervals are extended by using this boundary layer system, made possible by the accurate dosing characteristic of PC pumps.
Maximising energy and minimising sludge
Thames Water has 15m customers, 350 sewage treatment works (STW) and treats over 4.2bn litres of sewage per year. Its strategy is to adopt treatment processes that maximise the generation of renewable energy and minimise the volume of residual sludge produced, and the company is using thermal hydrolysis of sludge before anaerobic digestion to achieve these aims, often on existing STW.
The utility’s STW at Reading aimed to reduce onward sludge transport costs by increasing the ds% of dewatered sludge from 22 to 25 per cent. However, the piston pumps which transferred the sludge were identified as a limitation due to frequent maintenance requirements and the high pressures generated. While piston pumps are able to operate over a wide pressure range and can move viscous products over long distances, they do incur high operating and maintenance costs and have a very strongly pulsating flow. This is due to the pump action of filling and emptying a chamber of product which is then pushed through the pipe using a reciprocating action, requiring check valves to regulate and direct flow through the system. The pulsation creates a high operating pressure – at Reading, the piston pumps generated pressures of up to 64 bar and this would be likely to increase if the solids ds% was higher. Furthermore, they had hydraulic drives and drew absorbed power of 31 kW. These factors, along with the high maintenance requirements, added up to a high operational cost for Thames Water.
In comparison, progressive cavity pumps are also able to operate over a wide pressure range and can move viscous and abrasive products over long distances. However, they have a different principle of operation and employ a rotary action via a series of cavities which are filled and emptied continuously as they are ‘progressed’ through the pump. This results in low pulsation that generates lower pressure in the pipework, and which can be further reduced by boundary layer injection due to smooth laminar product flow. PC pumps have lower operating and maintenance costs and in this case drew absorbed power of 18 kW – a reduction of 40 per cent compared to the piston pumps.
Thames Water replaced the piston pumps, which transferred dewatered digested sludge from the energy generation plant to storage silos, with SEEPEX PC pumps. SEEPEX project-managed the installation, working with the utility’s approved contractors to deliver a turnkey system. The new pumps transfer higher ds% sludge with a lower energy demand, bringing the additional benefit of a reduction in the system’s pressure rating, enabling de-rating of pipework and valves to suit.
Over their two years of use, no maintenance interventions have been required. The PC pump system has delivered a hat trick of cost reductions compared to piston pumps: lower sludge disposal costs, lower energy use and reduced maintenance costs.