The race towards Industry 4:0 is on, it seems. Progressive cavity (PC) pump specialist SEEPEX is assisting AD operators, particularly those starting from a ‘low tech’ baseline, to think ahead and utilise smart pump technology to keep their AD plant connected and boost productivity, as this article explains
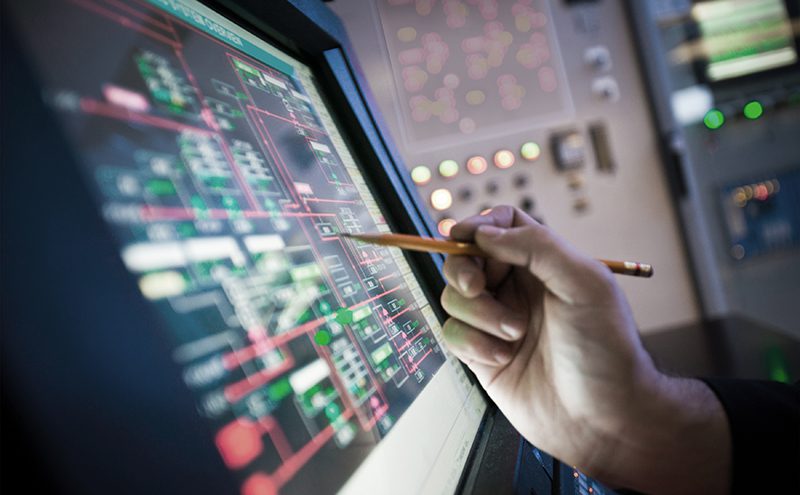
“All processes in the AD industry, no matter how simple, can benefit from preparation for Industry 4.0 or ‘future proofing’,” says Lesley Eaton, Business Development and Marketing Manager for SEEPEX UK. “There’s a general misconception that enhanced connectivity and Industry 4:0 are for big operations with ultra-sophisticated data capture strategies. Yet, like most decisions in business, whatever the size of your AD plant, it’s about thinking smarter, selecting the right pumping equipment for the job and factoring in current and future demands.”
Sensors and sensibility
PC pumps are often used to handle delicate components that are difficult to work with, due to high viscosity, the presence of soft solids or shear sensitivity – for example, food waste, slurries or digestate. However, smart PC pumps offer a perfect example of how embedded technology can help even the most common and straightforward equipment to optimise processes.
An example of this application could be using transducers as pressure or level controls which speed up and slow down the PC pump, varying the flow rate as required. Rather than using an on/off response when fill levels are reached, these pressure transducers send a variable signal to a PLC integrated to a variable speed drive, that will increase or slow the speed at which the product is delivered accordingly. This reduces the wear rate of the pump, extending the service life and lowering the total cost of ownership (TCO).
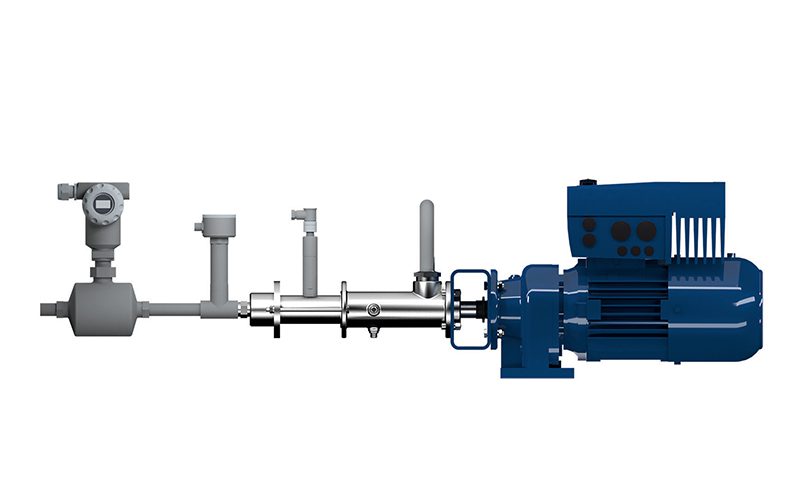
Likewise, there are a number of PC pumps fitted with sensors using IO-Link interface capabilities to switch pumps on or off. Replacing these with variable sensing technology reduces the reliance on remote data processing, enabling intelligent analysis of performance as well as variable flow rates. In addition, flow meters linked to variable frequency drives (VFDs) allow for real time feedback and speed control of motors to achieve accurate product flow, as well as enabling predictive maintenance schedules.
Pipework, valves and downstream equipment can all affect a pump’s performance. As pumps become digitally integrated into an AD operation, a properly selected PC pump can collect data to provide diagnostic tools for the entire system.
For example, an unexpected pressure increase could signal a product change, a closed valve or a pipework obstruction. Additionally, an increase in measured flow could indicate narrowed pipework. Using a comparison of theoretical flow vs actual flow can provide an early diagnosis of the condition of pipework and downstream equipment such as heat exchangers, enabling remedial action to be taken before issues occur.
Scalable for the future?
When selecting pump technology, it’s equally important to consider existing technology infrastructures and industrial control systems and how your new technology will integrate into common supervisory platforms, such as SCADA.
The development of progressive cavity smart dosing pumps (SDPs) by SEEPEX caters to these future requirements. Used either as a standalone item or integrated easily into SCADA systems, these PC pumps maintain accurate flow using continuous real time feedback and adjustment to overcome product and process changes that affect flow rates.
To simplify integration, the SDP has an intelligent VFD incorporating a PLC and special software and fieldbus communications. Input interfaces can be via a centralised system, a handheld HMI or by analogue and digital devices, which means that in addition to controlling the pump operation, data can be collected remotely and a picture of performance becomes clearer. Pump and system protection can also be managed using temperature and pressure sensors linked to the integral PLC.
Connecting to opportunities
As evidenced above, even a simple pump, tasked with distributing product from one source to another, becomes exponentially more valuable when connected. Data from one sensor can be combined with data from another and linked with cloud intelligence to make smarter, even autonomous, business decisions.
Rather than just connecting for connectivity’s sake, many of today’s AD operators are seeing connected devices as a transformational opportunity. “The reality is that data connectivity and Industry 4:0 permeate every aspect of every business, large and small,” adds Lesley. “With scalable options, there’s the potential to revolutionise how we work and cut downtime by providing continuous feedback on performance.”