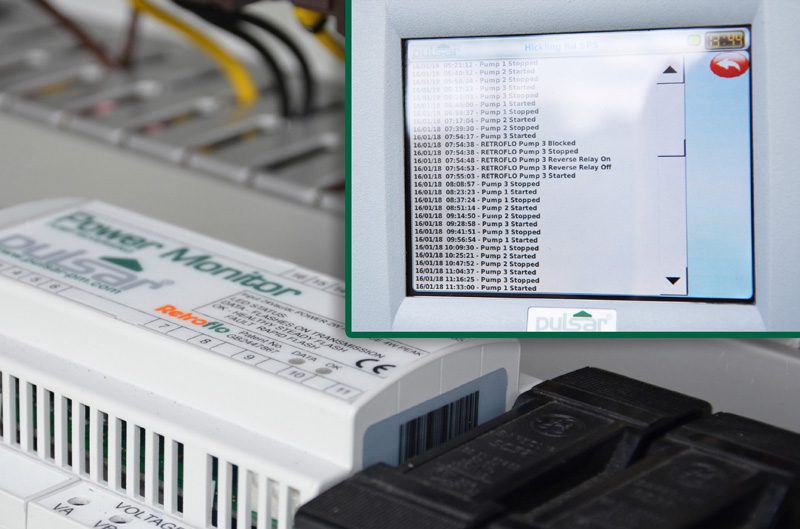
Measurement and control firm Pulsar Process Measurement offers a recent case study, where one of its control system products helped reduce the costs associated with a terminal pumping station.
Challenged with a significant problem of pump ragging in a Sewage Pumping Station (SPS), which caused repeated pump tripping and regular pump lift and clean operations, measurement and control firm Pulsar Process Measurement recently worked with Severn Trent Framework Panel Builder CEMA Ltd to supply automatic pump reversing technology delivered through a high specification control system (the Pulsar Ultimate Controller product). The Ultimate Controller also logs site data and provides all necessary control functionality for the well. There was no need to modify the existing compact cabinet or replace drive units on the pumps.
The SPS, in a village on the Nottinghamshire/Leicestershire border, is a terminal pumping station, receiving from three other pumping stations in the village and pumping to the local treatment works, 1km distant. It was identified as a problem site as part of an exercise undertaken by Severn Trent. The SPS, 30 minutes drive from the nearest engineering base, was creating frequent telemetry alarms requiring a 4-hour response. Operators and technicians were responding to calls at all hours to reset tripped pumps, and STW faced possible ODI (OFWAT Outcome Delivery Incentive) penalties. Staff responding to out of hours callouts were then unavailable the following working day, meaning that programmed work had to be rescheduled.
Control systems provider CEMA Automation had supplied the MCC panel, and Framework Manager Chris Hutchinson attended site and subsequently chaired a meeting with all stakeholders. Chris said, “It became clear to us that the issue was in the chamber design, causing the pumps to rag up excessively, tripping the pump starters.” The pumps were being lifted and cleaned as often as once a month.
Hutchinson went on, “I had attended a seminar at Pulsar in Malvern, and I knew that their Ultimate Controller offered a pump reversing feature as an optional extra. The normal solution to the issue would have been to install variable speed drives, but in this case there was no room, a new cabinet would have had to have been supplied”.
Pulsar’s Ultimate Controller is a compact control system that also incorporates the firm’s DATEM level control software, offering the user a choice between non-contacting ultrasonic or RADAR measurement (in this application, ultrasonic was used). The Ultimate Controller is designed to offer sophisticated control of the pumping station, including an in-built WITS compliant telemetry outstation and even the option of a camera. Pump power usage is monitored by optional Pump Monitor modules mounted in the starter section, which in this case included proprietary Retroflo® software that automatically detects load and reverses the pumps to clear ragging.
Since the installation of the Pulsar equipment in August 2017, there have seemingly been no further unforeseen maintenance requirements on the pumps. As Zac Dorn, the technician responsible for the site said, “Each lift and clean operation required a couple of operators and a couple of hours, and it meant that planned work went out of the window. I’m really pleased with the Ultimate system. The data logs are also invaluable, we can immediately see how many times the Retroflo® has reversed the pumps, we don’t need a PLC to manage the station and we can rely on the equipment to perform.”