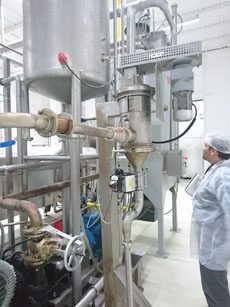
Cooking oil recycling has evolved a little in the past decade or so. Traditional technologies made it difficult to filter used oils consistently and guarantee them for use in food production, so often the aim was simply to recover a material usable as a biofuel in applications like road and rail transport. With ongoing innovation and advances in the equipment applied to filter used oils, it has become more feasible to safely re-use oil, feeding it back into the production cycle in applications like food manufacturing. Darren Ralphs of filtering equipment manufacturer Russell Finex describes a recent case study, involving a food manufacturer in Turkey, an application that highlights the importance of selecting a filter that can meet certain requirements in terms of particle size and versatility.
Milhans Gida is a producer of healthy, high-quality nut products and snacks in Turkey. Established in 2009, the company has grown rapidly to become a major manufacturer of private label products to some of Turkey’s largest food retailers, as well as supplying its own range of Milhans snacks.
At Milhans’ production site in Kocaeli, Turkey, a key area of production is the peanut processing line. Quality and hygiene are important priorities here. The firm is constantly reviewing its processes and how well they perform in these respects, as well as their environmental impact. When seeking a filtration system to optimize the recovery of and reuse of cooking oil from the frying process, Milhans recently consulted Russell Finex.
The peanuts are cooked in an industrial frying machine at around 150°C using vegetable oil. Once a certain quantity of peanuts has been cooked, the oil is removed from the frying machine and filtered to remove contaminants, before being recycled and used again. Previously, Milhans was using a paper filtration system to filter the recovered oil. However, this system didn’t achieve the required throughput, nor did it provide consistent filtration quality. Moreover, there was production downtime given the need to manually change the paper filter cartridges, which often became saturated and blocked with contamination. Changes would sometimes have to be carried out multiple times a day.
Alev Palabiyik, Milhans Production Manager, said, “The paper filters we were previously using to filter the cooking oil were not meeting our production needs. These filters were not able to produce the consistent, fine filtration required and we were experiencing high costs through having to continually change the paper filter cartridges. We also needed a filtration system with significantly higher capacity to meet the increasing demands for our peanut products.”
The firm decided instead to go for the Self-Cleaning Russell Eco Filter®. The device can be installed with a proprietary filter management system that reduces operator involvement and production downtime. This filtration system is available in a variety of sizes, high temperature configurations, and horizontal and vertical specification, making it versatile and easy to install into an existing production line.
Compared to the paper filter-based system , the Self-Cleaning Russell Eco Filter® processes 20 times the quantity of cooking oil, whilst filtering at a finer particle size –these filters can remove oversize down to 10 micron, easily achieving 50 micron compared to the 80 micron achieved previously. In addition, the unique self-cleaning design means there are no stoppages to change filter cartridges and no slowing of throughput to clean blocked filter elements.
Mr Palabiyik continued, “ We can expect to achieve a return on investment of 150% per year on the unit, through savings made on not having to purchase replacement paper filter cartridges. The increased quality of the recovered oil means we can continue to meet the high standards expected by our customers.”
These filters feature a unique wiper system – called SpiroKlene™ – that removes oversize contamination from liquids down to 10 micron. The filters are totally enclosed, meaning no fumes and limited operator exposure to liquid. Russell Finex provides a range of high-flow, high-temperature and sanitary liquid filters, meeting the hygiene needs of food manufacturers. In addition, horizontal and vertical configurations and various sizes are available to fit the dimensions of existing pipework and make them easier to install.