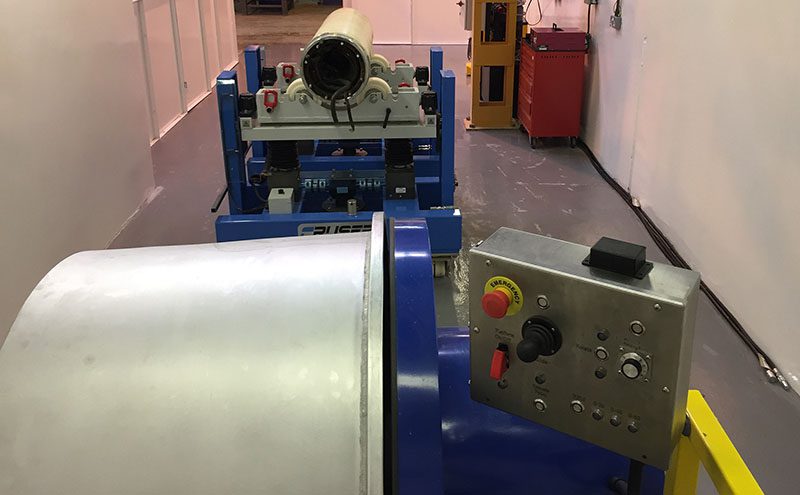
Rapid Solutions, an AEMT member based in Baku, Azerbaijan recently added a specialist rewind facility for submersible pump motors within its existing IECEx accredited service facility. As a result, it has cut time-to-completion massively and won a prestigious order from one of the Caspian Regions Oil and Gas Industries major operators.
Founded in 1996, Rapid Solutions is an integrated solutions provider of lifecycle services which include: engineering and design, process and pipeline services, automation, electrical, control and instrumentation, safety and fire protection construction, maintenance and support services. Aftermarket services includes the motor maintenance, rewind and repair operation, which offers a wide range of services from a large, dedicated motor services workshop as well as additional workshops for rotating equipment and valve maintenance and repair services.
Until fairly recently, Rapid Solutions did not have the capability to repair submersible pump motors. Equipment owners had to send these motors back to the UK, adding significant expense and time, as well as introducing additional risks associated with consignments getting lost or damaged during transit.
Due to the sizeable offshore oil and gas production industry in the region, Rapid Solutions realised that investing in and improving their local capabilities would be beneficial for themselves and the industry in general. Rapid Solutions did some research into the needs of the region and with technical collaboration and support of Hayward Tyler the company which provides similar services in the UK and which also manufactures the specialised equipment which is used to undertake these specialised repairs, it was decided that a relatively large state-of-the-art facility would be the best option to pursue. Further, it was realised that this could be set up as a dedicated facility within the existing Rapid Solutions rewind centre, a solution that had operational, technical and commercial advantages over a separate building.
The design and layout of the new submersible motors workshop is based on the innovative Hayward Tyler Centre of Excellence in Luton, England. Like its counterpart, the Baku facility is achieving high levels of productivity through the use of ‘Cruser’ trolleys rather than overhead cranes for moving the large motors and associated parts between the workstations.
Overhead cranes are the conventional choice for workshops where large workpieces have to be moved. However a better, safer and lower-cost solution has now been established at Hayward Tyler by transporting the motors on specially-designed trolleys. These have become known as Crusers in memory of a Hayward Tyler colleague who passed away unexpectedly.
Each Cruser is kitted out with fittings and equipment matched to their duty and can carry loads of many tonnes. They are driven and steered by a battery-powered detachable pedestrian-operated tug. As such they are highly manoeuvrable and in use are proving far more flexible, efficient and cost-effective than overhead cranes. As the trolleys may be at each workstation for a considerable time, the tugs can be uncoupled and used elsewhere, sent to recharge or simply stored.
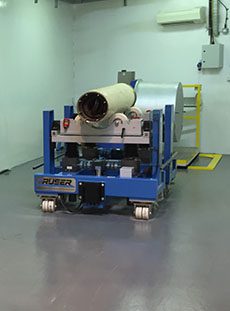
Rapid Solutions also installed a special design of motor winding drum in its new Baku facility which helps speed up the process considerably compared to traditional methods.
With its newly improved facilities, Rapid Solutions quickly secured a contract from the operator to repair wet wound, submersible motors, which are primarily used on offshore oil production platforms to provide sea water for process and fire-fighting duties. The motors range in size from 265 kW to 1100 kW and operate on 690 V or 3,300 V supplies. The motors are used to drive vertical, multi-stage pumps which are suspended from the oil production platforms. They are critical components since all the water needed by the platform is provided by these pumps. Reliability and availability are therefore of the utmost importance.
Parts used for the repair are provided by the motor OEM, American company SPX Flow, and Hayward Tyler through their technical support and proven submersible motor design is enabling upgrades to the motors to be carried out when requested.