Trench technology specialist CJ Kelly Associates recently supplied the Brawoliner 3D lining system to Cambridgeshire-based lining contractor Dalrod for installation on what at first appeared to be an “almost impossible” lining project

As part of the refurbishment of classic old Victorian railway buildings in Swindon, two metal downpipes taking rainwater from the buildings’ roof were in dire need of repair because of leakage at joints and water seepage through small pinholes caused by corrosion in the fabric of the original pipes. This at first might appear to be a standard downpipe renovation project. However, the two downpipes were located in the middle of a set of four buildings with no direct or easy access from the roof. Furthermore the bottom ends of the down pipes were located in a toilet area, which also meant that there was very limited access to this end of the pipes.
In addition to these difficulties, the downpipes were part of the building structural support and so could not be removed or cut without detriment to the overall structural integrity of the building.
The building refurbishment contractor needed to find a solution that would not only renovate the pipes but also not impair the ongoing refurbishment works and other activities in the buildings in question.
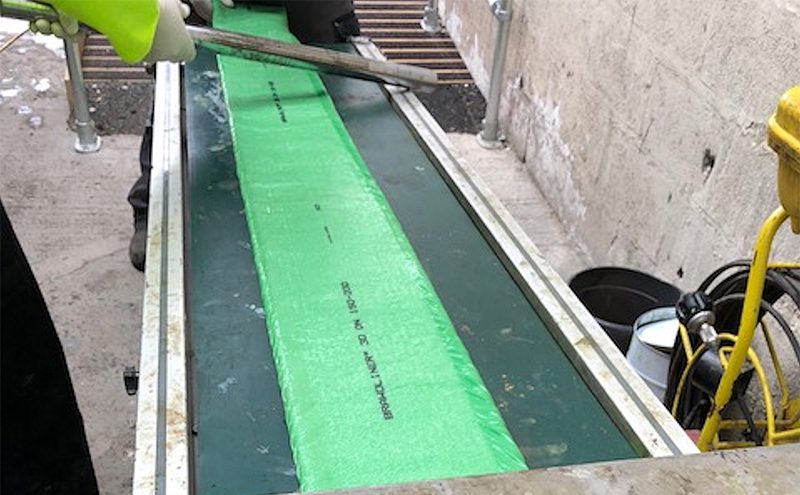
An unusual configuration
On-site inspection not only highlighted that the accessibility of the downpipes would be challenging but also that the pipe configuration was in itself highly unusual. Both the downpipe ‘mouths’ were located in the roof valley between two sloping sections of the roof, which also had unique roof tiles that if damaged would be difficult, if not impossible, to replace.
On inspection, the ‘mouths’ of the downpipes were found to be barely 7 in long x 2 in wide (180 mm x 50 mm) rectangular openings which extended for little more than 11 in (280 mm) downwards into the pipe run. Thereafter the pipes opened out into circular metal pipes of 9 in (230 mm) diameter at the top narrowing to just 6 in (150 mm) diameter after a 90º bend at the foot of the 12.8 m long vertical pipe length. These accessibility constraints and the pipes’ dimensional characteristics would be a challenge for any contractor.
Having employed the Brawoliner® 3D liners on previous projects Mike Pollard, Operations Director with DALROD was sure these difficulties could be overcome with planning and forethought.

Careful design
Given the complexities of the site Mike Pollard took personal control of the design and initial site operations. The logistics of getting the required equipment to the launch sites for the liners was probably the first major challenge. Installing the liners from the lower end of the downpipes was not an option given the amount of excavation this would require in the toilet areas. The only viable access was from the roof end.
To get the liner launch drum to the launch point on the roof, a special dolly was designed that would not only carry the launch drum across four roof spaces but also do so without causing damage to the roof slates, whilst the wheels remained in the roof valley. The dolly with the liner drum attached was fork lifted up to roof level and carefully placed on the roof. Transportation was in itself difficult given the limited space available for personnel access along the fairly long roof route over four different roof tops.
Once at the launch site the drum was transferred to a level platform next to the downpipe mouth prior to the liner launch. The drum also had to be strapped down as the weather brought with it high winds which could otherwise have dislodged the drum in mid-liner installation.
The lack of useable space at the launch site also meant it was not possible to get access for items such a hot box or hot water system near the launch drum for hot curing of the liner. The nearest point at which this could be achieved was some 80 m from the liner launch point. So, it was decided that the liner installation had to be achieved using a standard Brawoliner® 3D with standard ambient cure resin.
This again would not normally be a problem. However, it turned out that weather conditions for the period scheduled for the installations were some of the hottest in the year to date. This of course meant that the ambient cure lining had to be deployed in an even shorter timeframe, to prevent the liner curing before it was fully in place in the host pipe. To overcome the hot daytime temperatures, lining was prepared early in the morning.
The next limiting factor that threatened to make life difficult was the ‘letter box’ access of the downpipe. With such a limited open area to work in, the liner being installed had to be folded and fed through precisely, along with its attendant control rope, to prevent it hanging-up in the opening and yet in such a manner as to allow it to be fed into the pipe with sufficient speed to complete the installation before curing of the resin started to occur, a very delicate manoeuvre.
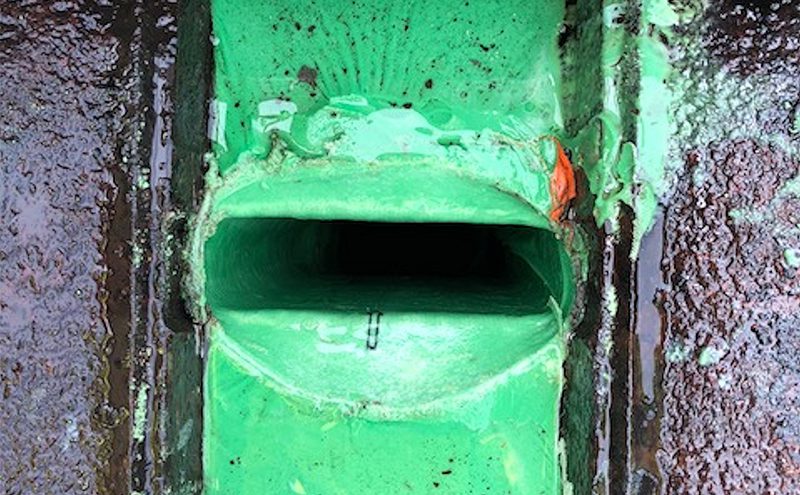
Lining
Having measured the downpipes and ascertained the liner length required, the liner was impregnated at ground level and loaded into the liner drum. This was then lifted by fork-lift to roof top height some 18 m high, from a nearby railway siding. From there it was guided on the dolly to the downpipe mouth. The liner was then attached to the downpipe and the inversion started taking care with the liner as it passed through the letter box opening. The liner installation involved a combination of both water and compressed air to complete the inversion using techniques that have been developed in-house by Dalrod over the years. Once installed the liner was allowed to ambient cure over 1½ days to ensure complete curing.
To finish the installation, Mike Pollard designed and manufactured a bespoke top seal using the green Brawoliner resin. This covered the top of the liner and the surrounding roof felt to ensure that the liners and the host pipes would be watertight and not affected by any changes in conditions in the future.
As designed, both lining installations were achieved with great success, without the need to dismantle any facilities or excavate in the downpipes. Mike Pollard said of the project: “In all my years in the lining game I have seen and operated on some strange sites but this must be one of the strangest. To say this was a challenge is something of an understatement, but with the right team, the right planning, perseverance and the right liners, we were able to meet and beat all the challenges placed in front of us. Whilst each lining needed to have a slightly different approach, both utilised the same basic idea for installation. Each was however a one-shot installation. If anything had not gone to plan, there would have been significant problems for the client, but ultimately both the liners were installed to our customer’s complete satisfaction.”
Senior partner John Kelly said this was the sort of installation that Brawoliner was made for. “The seamless textile liner adjusts itself to every pipe diameter during the installation process without operator intervention which ensures a crease free finish to the cured liner.” He also praised the effectiveness of the job carried out by Pollard and team.