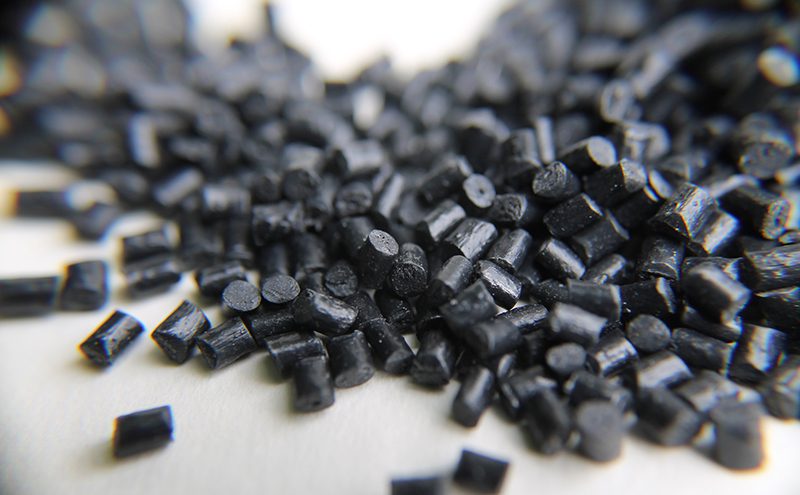
Brexit offers fresh opportunities for the UK and its manufacturers to secure their raw material supplies, such as recycled plastics, from a stable domestic market and stimulate a circular flow of materials, according to Axion Polymers.
The North West-based plastics recycler suggests that potential difficulties in transporting material across borders after March 29 2019 should become a driver for growth in the domestic market as purchasers seek to reduce inward material supply chain risk.
Axion Director Roger Morton asserts that freedom from regulatory controls and external policies, coupled with the ability to set our own rules, could encourage greater investment and enable the UK to ‘get ahead of the rest of Europe’ in material recovery and resource security, provided there is strong Government leadership.
Axion produces its high-grade recycled Axpoly polymers derived from UK end-of-life vehicles at two sites in Manchester. Plastics are extracted from end-of-life cars and other metal scrap at its SWAPP facility in Trafford Park and further refined at Salford, where recent laboratory equipment investment is further enhancing the products’ properties and quality.
Mark Keenan, Axion Polymers Business Development Manager comments: “With 31.5 million cars currently on UK roads, our future end-of-life vehicle feedstock for our recycled polymers is assured. And that can only be good news for UK companies seeking to use locally-sourced plastic raw materials that can go back into a range of products, from new cars and electrical equipment to construction products,” adds Mark.
Roger says: “Brexit is inevitable now. Although complications could arise, we are taking a positive approach. British companies should focus on the opportunity that leaving the EU offers and how we can make the most of our resource sustainable position.”
A good example here, he points out, is steel. With annual consumption (12 Mt) versus annual arisings (11.5 Mt), this market could be much more ‘circular’ than the existing export of scrap/import of finished products model. Similarly, demand creation for the use of recycled polymers in new automotive, electrical and building products could encourage further investment in more processing plants like Axion’s.
While material quality controls, such as REACH regulations and other standards, should remain ‘mirrored with Europe’, Roger suggests there could be an opportunity to ‘take the lead by designing and implementing a set of regulatory measures that drive the transition to a circular economy here’.
Such measures could involve heavily-modulated producer responsibility obligations for brands that make the most effort to change to fully recyclable designs and/or utilise high levels of recycled content. “This would require vision and a brave government with strong leadership” observes Roger, “but in an uncertain world; what’s certain is that material would be available in the UK for use in the UK!”