Both Brexit and the Chinese National Sword restrictions present serious challenges for the UK waste and recycling industry. Can we continue to send our waste overseas? How quickly can we establish a home-grown reprocessing infrastructure? A panel discussion at the Scottish Resources Conference (3 October) mulled over these and many other questions.
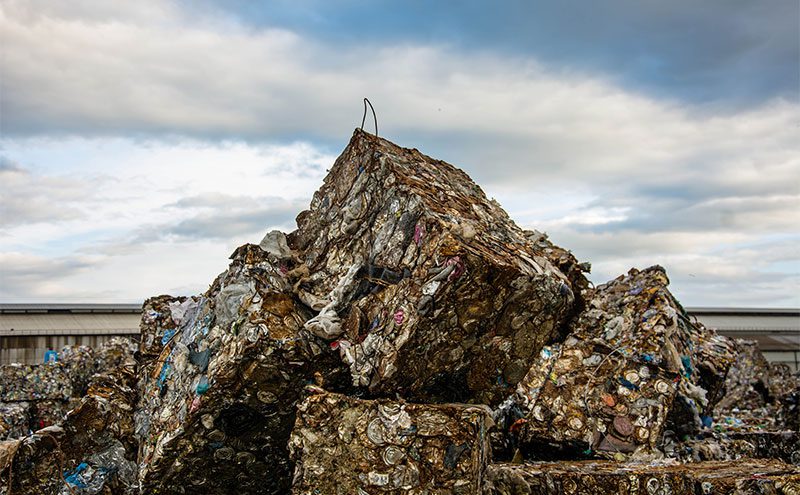
Since China announced its decision last year to restrict waste imports, the prices for these materials have been driven down, and some materials have become “impossible to move”, said Jim Brown, commercial director with the Binn Group, a Scottish recycling firm. While he said he didn’t think firms in his sector “intentionally go out to move or sell materials that are not of high quality”, there was certainly now a great pressure to improve quality.
We’ve seen “a lot of value disappear from a lot of different recycling streams”, said Colin Morrow of SEPA. The immediate challenge is to find new markets for these materials, and to minimise the volumes that are already slipping down the waste hierarchy. Making the transition to a position where we have more domestic infrastructure “will not be easy”, he said. And in the meantime we need to try and maintain public confidence in terms of getting people to put the right stuff in the right bins.
Brown said we need to build the infrastructure here in the UK. There are some great examples of this, such as Project Beacon’s advanced recycling plant to be built in Perthshire. We need more of the same, he said.
Trading places
In 2016, China was the principal destination for UK plastic packaging waste, receiving around 256k tonnes, but now, in 2018, it is not even in the top 10. Malaysia is now accepting around 64k tonnes of this waste but has in recent months introduced a temporary suspension on imported materials. And the EU’s share of these UK waste exports has increased from 33% to 42%. Turkey is another destination that has increased its share, from 3.5% to 12%.
Duncan Simpson of Valpak said there was still a lot of demand internationally for certain types of plastic recyclate including PET, HDPE and LDPE.
Where metal recyclate exports are concerned, Antonia Grey of the British Metals Recycling Association (BMRA) said Indonesia, Vietnam and Malaysia had become more important since China’s decision, a probem since these countries are now talking about restrictions too. “Where our materials go after that, we’re not sure.”
At the same time, the waste industry is having to deal with Brexit, creating a level of uncertainty that Brown said is “beyond comprehension in many ways”. As the only firm currently exporting solid recovered fuel (SRF) from Scotland directly into Europe, he said he had already been hit with the increased costs caused by the change in the exchange rate.
Speaking for the BMRA and metals exports, Grey was concerned about the uncertain fallout from Brexit, and the need to negotiate trade deals, and tariffs of 7 to 25%, depending on the shipping – a lot of extra money to find.
One audience member asked how concerned should we be about a shortage of labour in the waste sector? Grey said the vast majority of workers in the metals reprocessing yards come from East European countries, and they’re doing jobs that perhaps wouldn’t be included in the “skilled jobs” category within the new coding system. It’s often assumed such jobs could be filled by people from the UK, “but it’s not for want of trying”, she said.
Brown seemed to concur: “I think the term ‘unskilled’ is quite demeaning,” he said, since “the jobs we’re talking about are being performed by quite skilled people” and we should be concerned about it.
Adam Read said it was clear Brexit would bring a massive increase in the costs associated with these jobs, with a need to increase wages to attract new workers.
Will recycling levels go down?
Someone else asked: are we as an industry to expect reduced recycling rates going forward, or lower than we’ve had in the past? And if we accept that, how long is it going to take to get back to the levels we had when China was accepting our waste?
Morrow of SEPA said it was a question of how long will it take to invest in the requisite infrastructure – probably “quite some time”. Uncertainties at present – which tend to impede investment – include those around the supply of material, and establishing markets for different types of material and incentivising their development – “it’s very difficult to put a time frame on that”.
Simpson of Valpak said “the recycling level will probably fall or certainly stagnate”, but he believed it would go up again eventually, following a raising of standards and a move towards a more accurate and robust system of measuring and regulating materials than has been the norm. Higher PRN prices – and with plastic waste they are higher than they have ever been – could be seen as a sign things are moving in the right direction. Eventually everyone will accept paying the sort of PRNs that normally only paper can get.
Brown agreed that a drop in recycling rates is inevitable given where we are, but “whether our customers want to accept it is a different thing”. Obviously what’s needed is greater investment in the UK’s recycling infrastructure, which begs the question of where the money for this should come from. Scotland, for example, has a recycling industry dominated by lots of small, regional, family-run SMEs, who don’t have the money to invest in high technology separation plants and the like. He believed government should step in here. The chair asked who in the audience agreed, and almost no hands were raised.
Simpson spoke about some of the EPR proposals that are currently on the table with plastic packaging. Greater producer responsibility for waste seems to be the direction of travel presented by legislative measures such as the EU’s Circular Economy Package, which specifies a minimum cost recovery level of 80% to be reached by 2023 – in other words, producers must be responsible for at least 80% of the cost of recovering any packaging they put on the market. This kind of progress will make things clearer for the collectors, and remove some of the costs they face. It’s important not to cut the reprocessors out of the equation, he said. “You can collect as much stuff as you like but if it’s not got a home to go to, it’s a very sad world we’re living in – worse than the China situation.”
Technology might also prove a salvation – or at least an important contributor to easing the current pressure, and Grey cited important developments such as processes to enable the recycling of the aluminium laminates used in flexible soft drinks packaging for things like Capri Sun.
One audience member, Jamie Pitcairn of environmental consultancy Ricardo, said he’d spent time this year in Australia. He said that if we in the UK think we’ve been hit hard by China’s National Sword initiative, Australia are “on their knees”. They’re having to work without the well developed kerbside recycling infrastructure of the UK, although they do have a lot of space available for landfill.
Developing secondary markets
Pitcairn also asked the panel how they felt about a procurement drive to help develop secondary markets for recyclate, and develop the infrastructure.
There are already high levels of recycled content in glass and metal products, but plastic is something of a laggard in respect of this kind of development.
Simpson of Valpak lamented the loss of an earlier UK initiative to stimulate secondary markets in this way, called REMADE, which was dropped by WRAP and ZWS. There was a change of focus at the time, towards collection (quality and consistency and so on), “and I think we lost an opportunity there, for a period of time,” he said. He seemed to think a focus on public procurement was the right direction to go. A forthcoming EU Procurement Directive will focus discussion in this direction, he said. Other initiatives such as the UK Plastic Pact will also help stimulate this kind of procurement within the private sector.
On 12 October the Plastic Pact announced a £1.4 million competition to support creative business ideas to stop plastic being thrown away, a contest that will be managed by WRAP and UK Research and Innovation (UKRI).
Source separation seems to be a direction of travel in the UK, for recycling collections. Back in 2007 and 2008 the UK government were making more of a case for commingling, which led to a lot of investment in Materials Recycling Facilities (MRFs). One audience member asked the panel if the days of the big MRF are now over, and if that kind of thing will become a niche business. If you were in the business now, and forced to choose between investing in treatment or collection infrastructure, where would you put your money?
Pam Walker of Aberdeen City Council said they had been running a fully commingled MRF system for about 18 months – “absolutely necessary” in a city environment like her own, where there are around 40k properties, all in communal collections that are very difficult to serve with kerbside collection. She said they had recently seen an increase of 50% in their uptake of commingled materials.
Commingled collection clearly suits certain localities – extremely rural areas, for example. But everyone else – 60 to 65% of all UK local authorities – should be running some form of dual – or tri-stream collection. “If the whole system is about getting quality [material] to reprocess, then it’s going to be about capturing that at source and trying to turn difficult materials into recyclable materials later,” said the chair Adam Read. And if there were to be bespoke targets for local authorities along these lines, these would have to take account of the varying challenges in different areas – so inner London wouldn’t have the same targets as Cornwall.
Another panel member said he’d seen the MRF in Aberdeen and had been “absolutely amazed” with the quality of material coming out. With the right kind of separation equipment, for example, people were achieving very good results with MRFs. And this is evident when you look at places like Germany, France and Belgium – they’ve got bigger MRFs but they’re able to do the job right.