The operator of a crop fed biogas plant has apparently seen its energy output double in just six months following an overhaul of the digester biology by anaerobic digestion (AD) experts FM BioEnergy, the authors of this case study. Based in Consett, Co Durham, the 1MW Generation X AD plant was operating at just 40% efficiency and was suffering from biological instability. But after control of the biology was handed to FM BioEnergy the plant was successfully recommissioned and is now operating at more than 80% efficiency
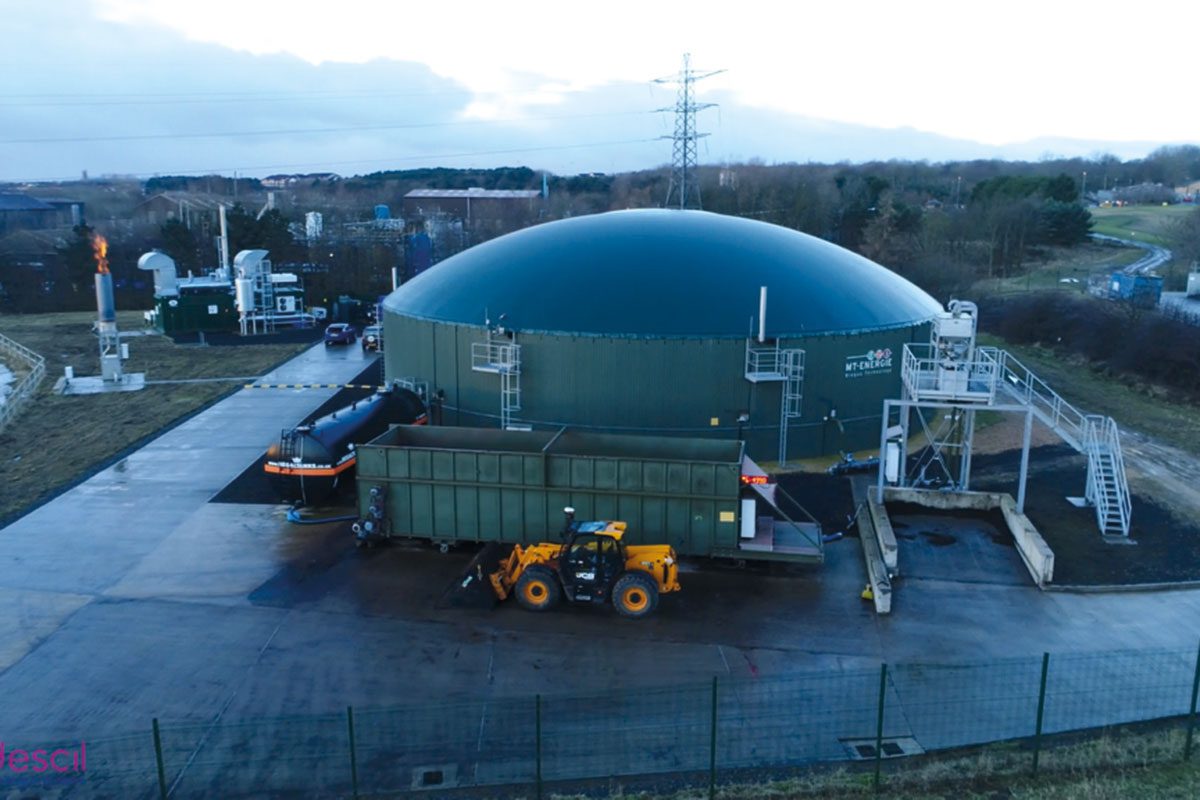
“The AD plant was developed in 2015 and was originally commissioned on 100% maize. But due to its location in an area where maize is difficult to grow, it was impractical to secure a long-term, reliable and affordable supply of the crop. It was therefore fed a mix of equal parts maize, grass and wholecrop cereal,” explains Ben Jenkinson, the independent management service provider brought in by Generation X.
The plant is a simple, single-stage mesophilic design and coped well with the initial 100% maize feedstock, as maize is extremely easy to digest. However, it was a different story with the more complex feedstock mix. Although cheaper and more readily available, grass and wholecrop cereals are more fibrous and difficult to break down, and the plant soon ran into problems.
Just a year after it was commissioned, the Generation X facility was averaging only 40% electrical output and was in a biologically and financially precarious position. By October 2017, the biological issues proved too great to overcome and the plant suffered a complete digester failure.
The road to recovery
During this time, Ben met Tim Elsome, General Manager at FM BioEnergy, part of the ForFarmers network. “I was impressed with FM BioEnergy’s background; the fact they are part of the same network as biological giants Schaumann and have a strong focus on R&D,” says Ben.
“But having already employed two biological consultants and seen no improvement, I was sceptical of repeating the same mistake. I decided to embark on a trial with FM BioEnergy and in February 2018, challenged Tim to successfully recommission the plant.”
Tim recommended the company’s dedicated BC ProStart micro/macro nutrient product, specifically designed to support AD plants during the delicate commissioning phase by creating optimal digester conditions for the bacteria to reproduce. He backed this up with an iron supplement, Atox:SCon, which has a fast reactivity to control hydrogen sulphide (H2S) levels in biogas.
Working on the assumption that most of the previous biology had been lost, the feeding plan was quite conservative at first. But after a short period, it was aggressively increased (going from 0-50 tonnes of feedstock per day in just one month), to achieve a high gas output in a short timeframe.
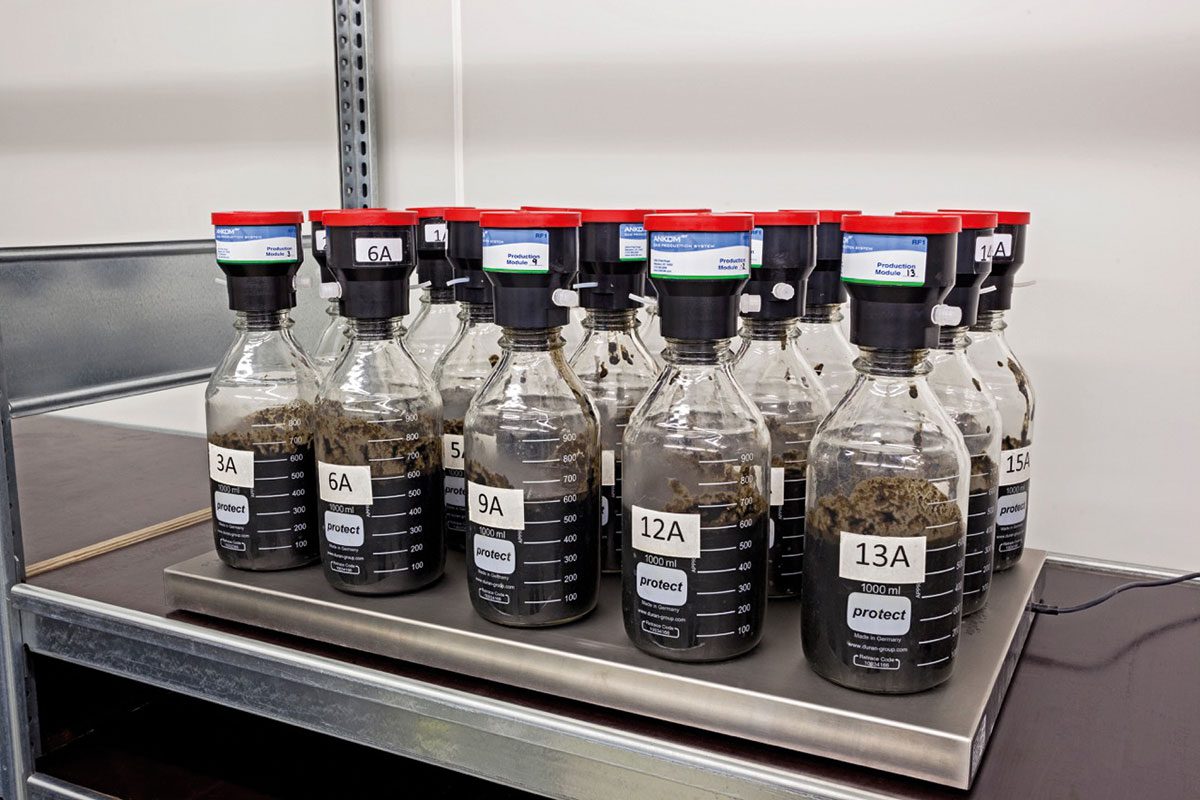
This ensured the successful restart of the digester and impressed Ben enough to continue the partnership: “In May 2018, after rolling out of the commissioning phase, we agreed to retain FM BioEnergy’s services long-term; but I knew this was when the hard work would really begin.
After all, the plant had been successfully commissioned the first time around only to subsequently fail, and I was well aware that our complex feedstock mix would still be a difficult fit for the plant’s design.”
Ongoing support
However, thanks to their extensive experience working with AD plants of all types and sizes, the team at FM BioEnergy was not fazed by the challenge. They devised a bespoke six-month biological support programme for the plant, which involved analysing the feedstocks to determine the expected gas yields and create the optimal feeding plan.
“We analysed digester samples once per week, looking at the FOS/TAC, acid speciation, ammonia and dry matter levels, and altered the feeding plan as necessary. And we spoke to the site’s operatives on a daily basis to review the gas yields, to ensure the plant was performing as expected,” explains Tim.
The Generation X AD plant is now consistently generating more than 80% of its electrical output potential – double the previous year. “The plant is running well and we want to keep it that way,” adds Tim. “We still analyse the digester contents once per week and now supply our BC Magxx supplement; a bespoke blend formulated against nutritional analysis of the digester, to ensure all trace element levels are within the correct range, with no over- or under-supply.
We are continuing to feed the digester with iron and also provide a bespoke enzyme product. Grass is fibrous and wholecrop rye is viscous; enzymes help to break them down in the digester and enable the plant to better cope with these complex feedstocks.”
For Ben Jenkinson and the Generation X team, the difference that FM BioEnergy has made cannot be understated. “FM BioEnergy stand head and shoulders above the other biological consultants we’ve come across,” states Ben.
“They’re not afraid to get stuck in and have walked our operations team through every stage of the process change needed in the feed make-up. In a relatively new industry like AD, knowledge-sharing like this is crucial to success. They’re quick to respond and take time to call into site when in the area to see things for themselves. Their knowledge of the AD process and how the entire plant should run is exemplary.”
Ben continues: “We’re now generating more than double the energy we were before they came on board; which is significant for this asset. But more than that, the constant battling issues we were facing were distracting us from the day to day business of running the plant effectively. All our time was spent fire-fighting. With FM BioEnergy’s support, we are now optimising our plant, with a view to getting it up to 100% electrical output.”