Envirotec spoke to UK distributor REC about the Dryclone® Air Drying System, and about the opportunities that exist to dry bio-waste and sludges at significant cost savings by using waste heat and electricity generated on site
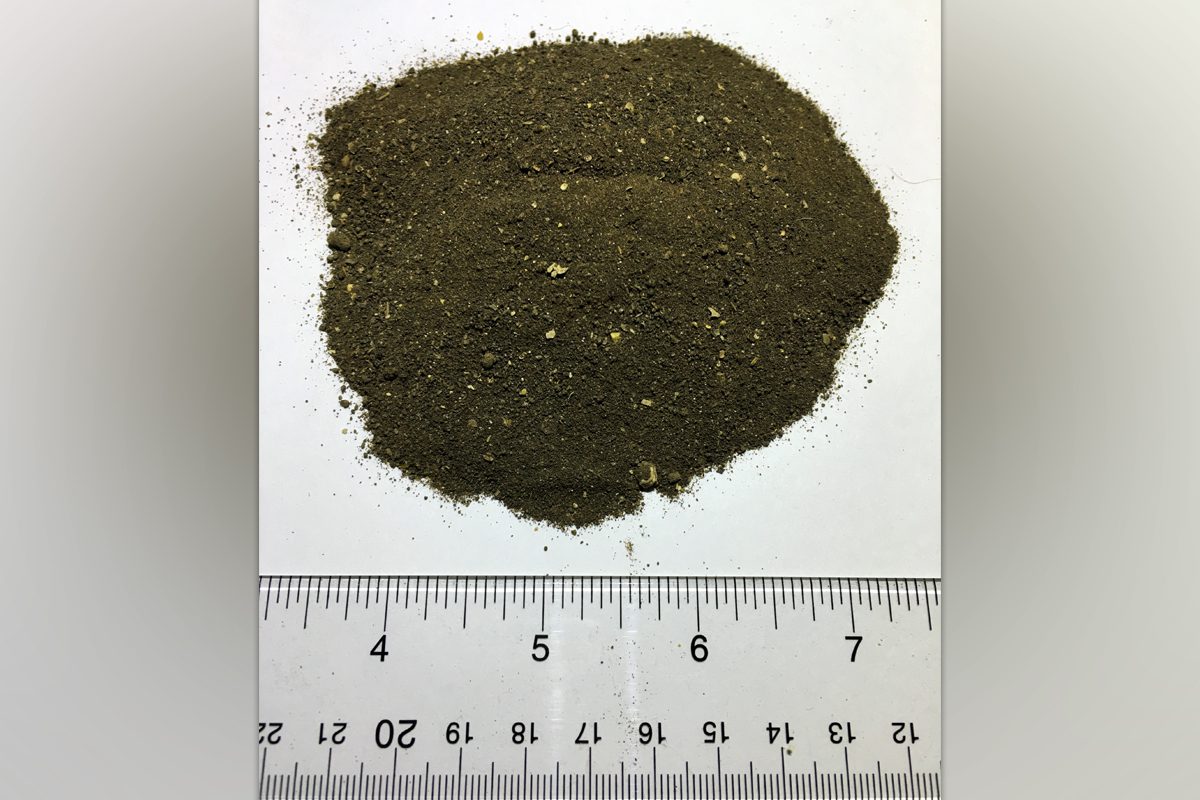
An increasingly rich menu of techniques and equipment is emerging to help recover energy and value from organic waste, and to keep it out of landfill. Anaerobic digestion has obviously become a popular and well-established destination for food waste and other types of material, but it is becoming increasingly apparent that it is just one of a range of options available. On the downside, AD – as with many other processes – leaves you with a wet, sludgy material that requires some form of disposal.
Two disposal routes for wet sludge present themselves at this point: spreading the material on the land as fertilizer (the ‘nutrient’ route) or disposing of it usually in landfill. However, if the sludge is efficiently dried, then you have more options in the nutrient route, and you also get the option of sending it to an energy-from-waste facility (the ‘energy’ route). While there are already signs emerging of a stricter regime in terms of the material that is deemed acceptable to be spread on fields, and the possibility of regulatory changes here in the future, it seems likely that many will want to regularly appraise the viability of these routes.
Sludge drying: the options
Bio-waste and sludges are frequently dried using equipment like drum dryers, fluidized bed dryers and other natural gas dryers, but other approaches have started to emerge. REC is offering an aerodynamic drying and pulverisation system called the Dryclone, whose function and apparent advantages were explored in a recent edition of this magazine (see Envirotec, May 2019, p50). The firm presents Dryclone as a cleaner, less expensive and more efficient alternative to the more traditional, thermal drying approaches. REC says one striking quality about the material produced by Dryclone is its homogeneity, with a much lower variance in moisture content across large batches cited by the firm’s CEO Pete Mulvany compared to other types of dryers.
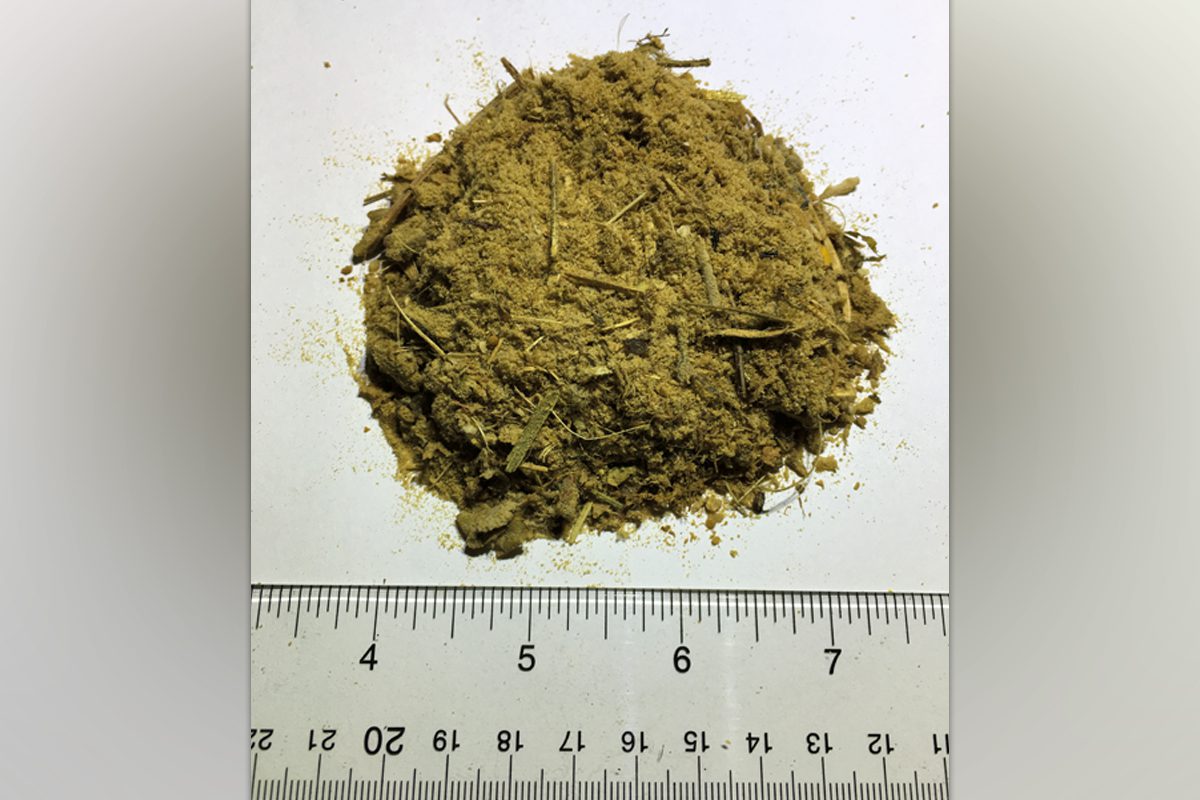
With conventional drying systems, the resultant material will tend to be toasted on the outside while the interior will retain more moisture, says REC, such are the results seemingly achieved by aerodynamic pulverisation. This moisture is a liability in emissions terms, since it can lead to the production of dioxins and furans when submitted to processes like gasification and pyrolysis. The moisture also makes the energy recovery process less efficient.
One bugbear with drying is its energy requirement. One way to make drying more economic is obviously to harness waste heat. “In Europe, the regulations and incentives are heavily slanted towards using every available BTU of waste heat,” says Mulvany.
Waste heat reuse has been harnessed frequently to support the operation of belt-drying systems.

For firms who choose to go down the energy route, significant quantities of high-grade waste heat may be available from the energy recovery stage, which might be a process such as incineration, pyrolysis or gasification, and at the electricity production stage, which might be handled by gas turbines and CHP units. Traditionally this high-grade waste heat can be used to support the operation of belt-drying systems. In addition, many bio-waste treatment processes produce a lot of low-grade waste heat, which can be difficult to harness in conventional drying systems.
Because the Dryclone is a low-temperature dryer thanks to its aerodynamic pulverisation, it’s able to use all the available low-grade waste heat from bio-waste treatment processes as well as conventional high-grade waste heat, says REC. And the firm says this results in significant energy cost savings and increased opportunities to benefit from incentives for using waste heat.
Mulvany speaks volubly and with some enthusiasm about the cost-saving opportunities opened up by combining the use of all available waste heat and by the use of ‘behind the meter’ electricity in this way.