A recent leak of an “acidic ferric salt solution” from a water treatment works into local waterways resulted in a £600k fine for a UK utility, and raised the possibility of enduring environmental damage. A widely-trusted line-of-defence against such leaks is the use of bunding. Chemical dosing solutions provider WES offers a review of the approach, its applicability and recent refinements
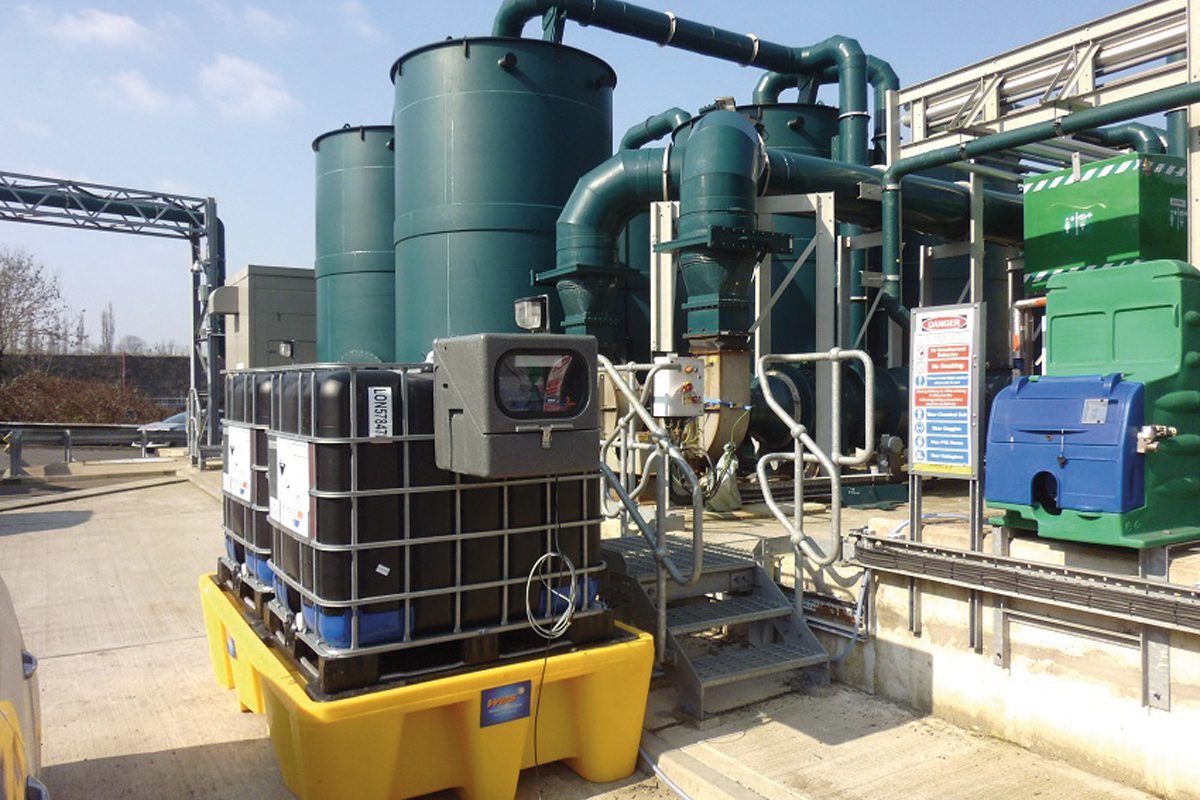
What is bunding?
Chemical storage bunds are structures that create a leak-proof barrier around an area containing hazardous liquids. The job of a bund is to provide secondary containment if the primary vessel leaks or bursts. By preventing leaking liquids from spreading, the bund gives you time to identify the cause of the leak and to fix it. Bunds can be used on all types of storage tanks, intermediate bulk containers (IBCs) and storage drums. Different bunds are available to suit different applications.
Bunds fall into two broad categories: permanent and temporary. Permanent bunds are either built directly on site or manufactured off-site in a factory and then installed on site. Bunds used to enclose free-standing storage tanks are normally designed into a plant’s layout, taking into account future inspection, cleaning and maintenance requirements.
Temporary or portable bunds can be used around smaller storage vessels, and are made from lighter materials. Bunds for IBCs can be constructed for ease of handling by forklift trucks, and are sometimes referred to as pallet bunds. This type of transportable bund helps to protect against spillage from IBCs or drums during transport, as well as when the container is located on site. IBCs are designed as delivery containers, not as permanent storage tanks, but in reality they are often used for short to medium-term storage on site. Crucially, any IBC used to store a chemical should never be left without a bund.
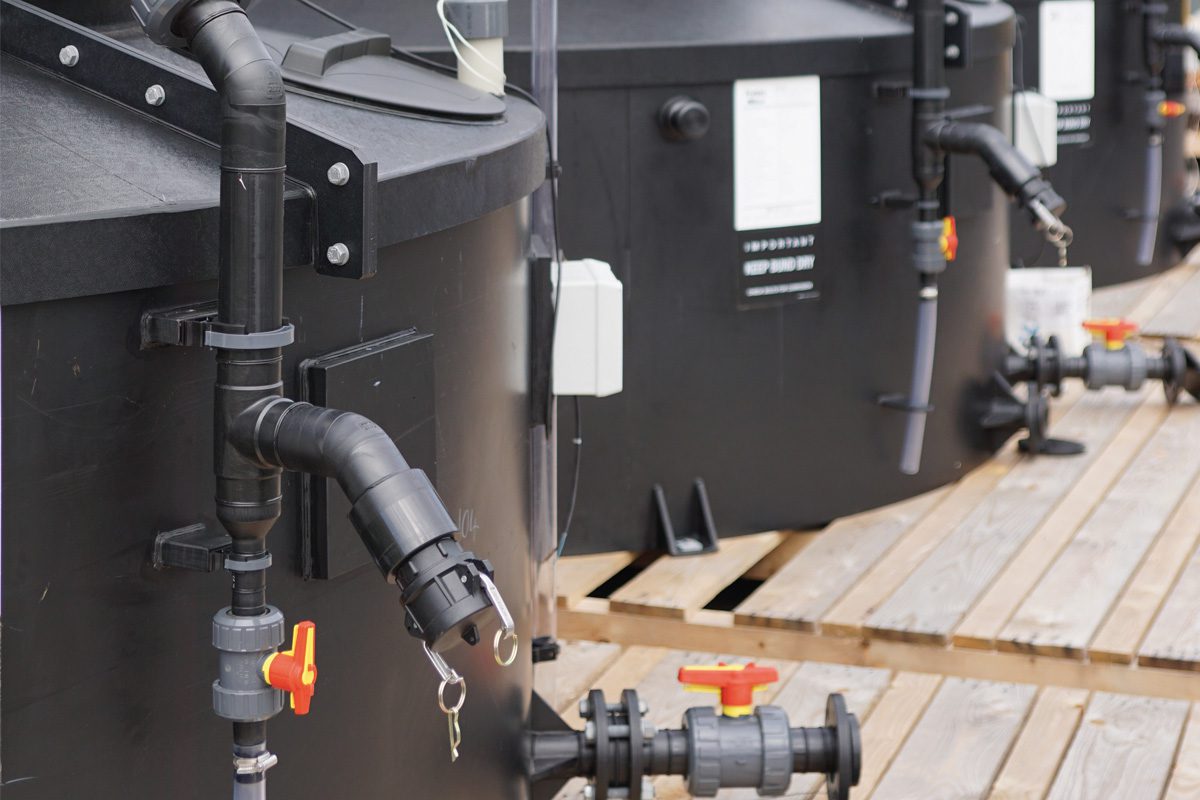
Choosing the optimum material
It’s essential to choose a bund made from the correct material for your requirements. There are several factors to consider, including the size of your storage containers, the nature of the chemical stored, the location of the containers and the environmental conditions. The choice of material is also influenced by whether the bund will be built on site or manufactured off-site.
The chemical resistance of your bund material does not need to be as high as that of your storage tank or container, since it is not intended to contain chemicals for long periods. The general rule of thumb is that the bund should be able to resist the specified chemical for seven days.
If tanks are connected during operation, bund capacity should be 110% of their combined storage capacity.
Most traditional, site-built permanent bunds are constructed from concrete, brick or block walls, standing on concrete floors. These materials, and any mortar used in the masonry walls, must be watertight and resistant to the stored chemical.
In recent years, the growing popularity of off-site manufactured bunds has resulted in a wider choice of materials and construction methods. One option for permanent bunds is prefabricated steel. However, steel is susceptible to both atmospheric corrosion and attack by some stored chemicals, so a special resistant coating must also be applied. There have been some notable steel bund failures in the water industry, where bunds were lined with GRP (glass-reinforced plastic).
Over time, a GRP lining can develop cracks or leak paths, which allow stored chemicals to contact the steel. A more resilient alternative for permanent bunds manufactured off site is plastic, and materials like polyethylene (PE), polypropylene (PP) and polyvinyl chloride (PVC), provide excellent chemical and atmospheric corrosion resistance.
When it comes to temporary bunds for storage tanks up to 1,000 litres, most are made from moulded low-density polyethylene (LDPE). This is similar to the material used for some chemical IBCs, drums and other containers. The material has good corrosion resistance, while its moulded construction creates a robust vessel. Steel can also be used for temporary bunds, but again it will need to be finished with a corrosion-resistant lining.
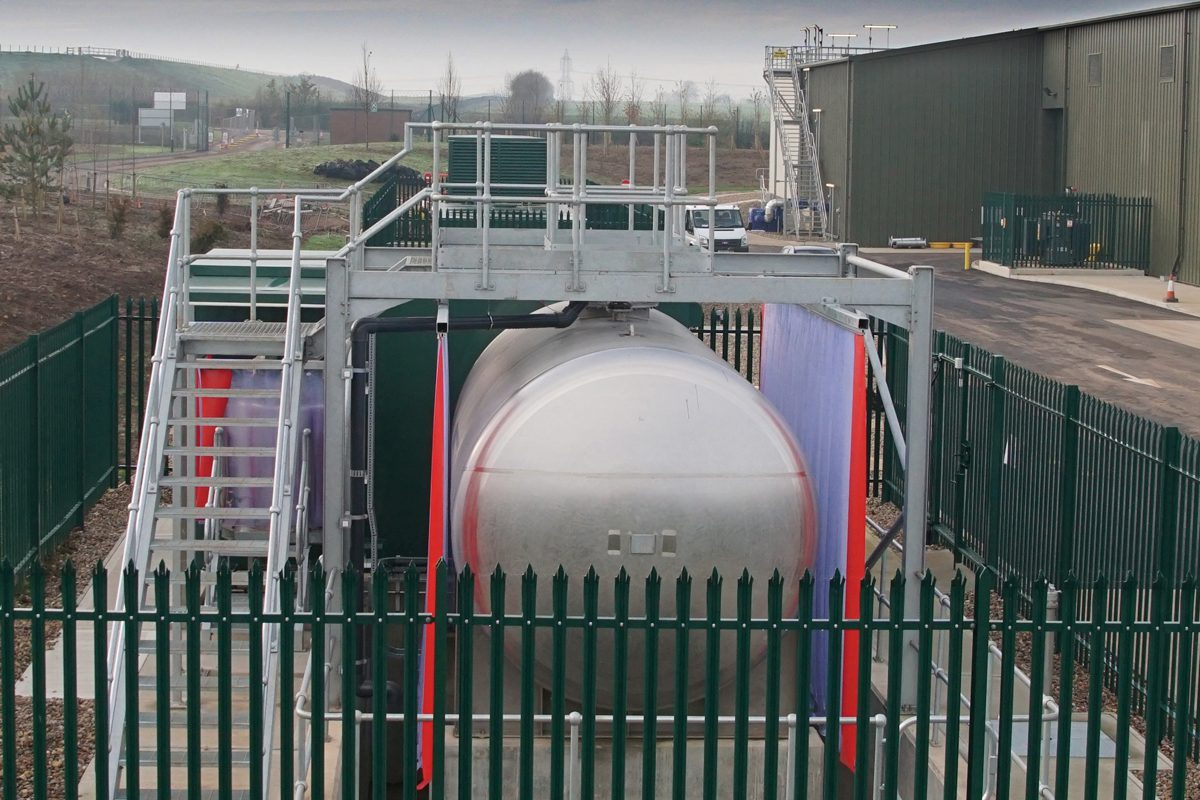
Developments in bund design
Off-site manufactured and modular chemical dosing systems have been growing in popularity, and there have been considerable advances in bund construction and design. For packaged systems up to around 30,000 litres, fabricated PE or PP bunds with a rectangular footprint are now commonplace. However, important design issues need to be addressed if these are to be considered a viable alternative to civil-engineered bunds constructed on-site.
Firstly, the plastic welds on plastic permanent bunds are not usually as strong or resistant to chemicals as the base material. Therefore, the bunds need to be well designed and reinforced to provide the required strength. Like any bund, they must be strong enough to contain the specified chemical, and to withstand any shock load created by a full tank suddenly rupturing.
Any fabricated bund design should include reinforcement bands or added strengthening webs to reduce the load on the welds. As well as protecting welds from high loads at the corners of the bund, external bands stiffen the sidewalls. Without them, many rectangular plastic bunds will bulge when filled with liquid.
Plastic fabricated bunds must also withstand the rigours of handling. Any bund manufactured off-site will be handled and moved frequently, from its completion in the workshop, through to loading, transportation and installation on site. Although a bund may be designed to form a rigid unit when sitting on a flat base, this rigidity can be compromised when the bund is lifted or moved. Protecting a bund’s integrity during handling may require purpose-made pallets, lifting points or additional fabricated features.
Temporary bunds, when moulded from a material like LDPE, have fewer problems as there are no welds or other stress points. However, those designed for transport by forklift may need special reinforcing features to give extra strength and stability.
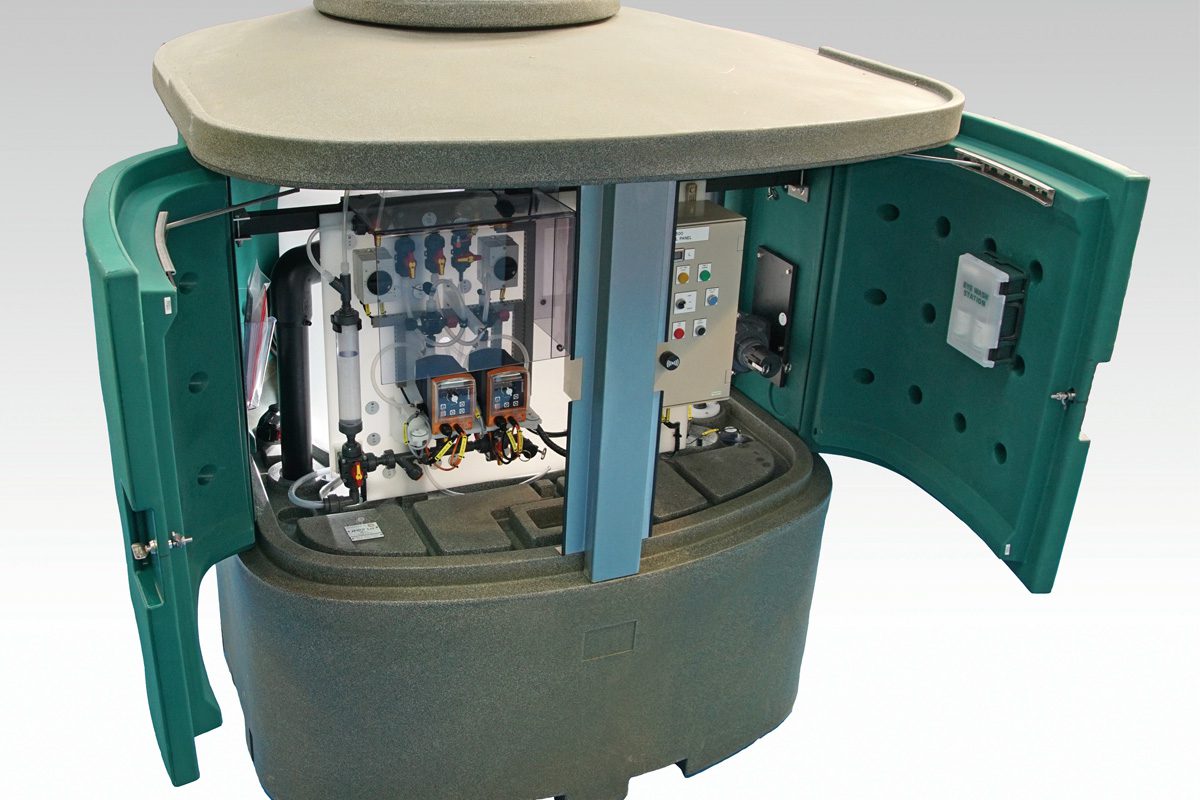
Bund sizing guidelines
WIMES: Water Industry Mechanical and Electrical Specifications provide detailed information on water industry standards relating to bunding. WIMES 8.02 stipulates that bund capacity should be 110% of the total storage capacity of the largest tank or 25% of the total capacity of all tanks, whichever is the greater. If tanks are connected during operation, bund capacity should be 110% of their combined storage capacity.
When calculating the required size for a bund, you must take into account any objects that take up volume within it, such as supports and tank stands, which reduce its effective capacity.
The wall height and floor area of a bund can be varied according to your needs. Choosing a lower wall, and a correspondingly larger floor area, will give you easier access for cleaning and maintenance, and for assessing tank condition. There is also less potential load on the sidewalls. However, low walls can be breached more easily by spigot flow – a powerful jet of leaking liquid passing over the bund wall. This risk can be countered by installing splash screens. A low wall can also be breached by the tidal wave effect caused by sudden and catastrophic tank failure.
Higher bund walls, with a correspondingly smaller floor area, have the advantage of a more compact, space-saving footprint. Their limiting factor is restricted access for maintenance and space for valves and level sensors.
With so many variables to consider when choosing appropriate and effective bunding, the simplest and safest option is to buy or hire complete chemical storage and dosing set-ups from a bunding specialist. That way, you get the optimum bunds for your needs, along with all necessary filling and safety systems, all pre-assembled and pre-tested.