
The issue of biogas leakage is one which many anaerobic digestion (AD) operators fail to address; often because the problem is invisible. However, the dangers associated with it – from diminished profits to environmental pollution and health & safety risks – should not be underestimated. Tim Elsome, General Manager for AD specialists FM BioEnergy, outlines the real cost of unidentified biogas leaks – and the inexpensive steps you can take to reduce the risks on your plant.
The scale of the problem
While most responsible plant operators monitor key parameters such as temperature, digester biology and biogas production, the majority are not checking for gas leaks, believing it’s an issue which doesn’t affect their plant. The evidence proves otherwise. Over the last eight years, 85% of the 964 plants we have surveyed in the UK and Germany were suffering from biogas leakage. Translating this to the UK as a whole could mean that 550 plants are at risk. If each leaked an average of just 0.5% of their capacity, it could result in 6,000 tonnes of methane escaping into the atmosphere annually.
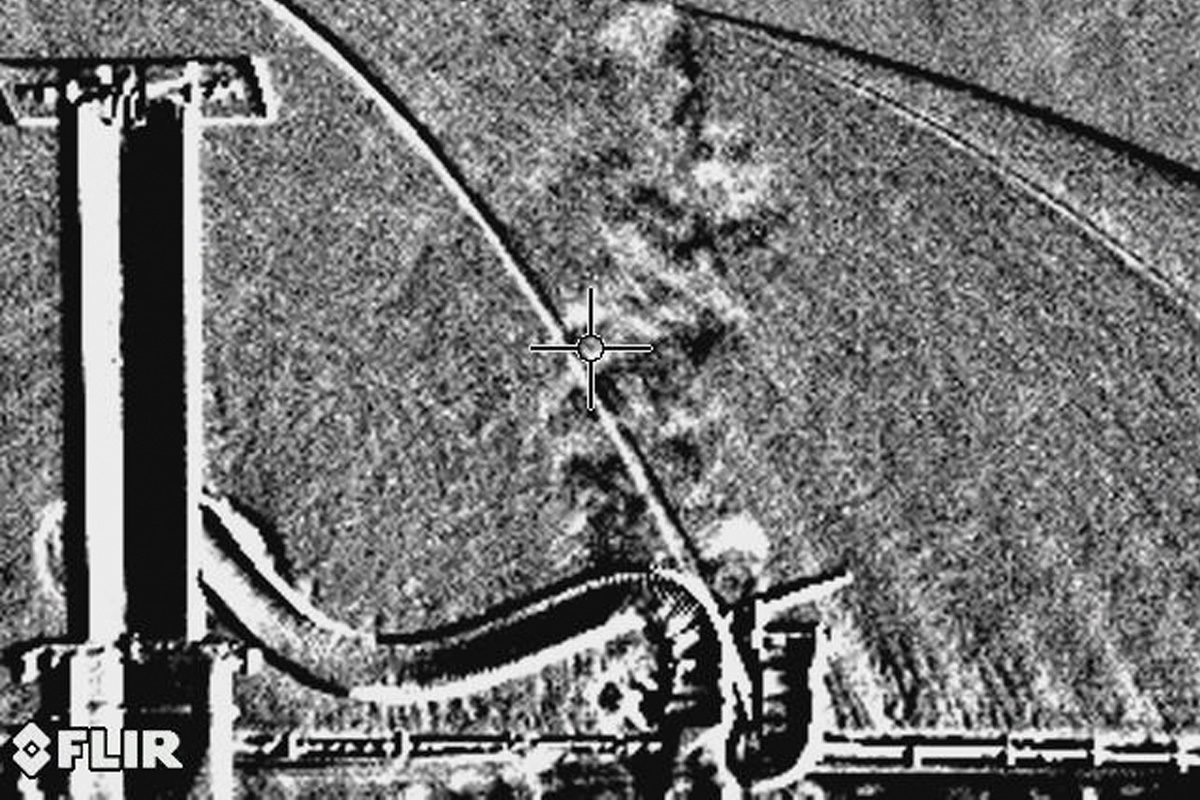
The risks of doing nothing
Aside from the environmental dangers, biogas leaks bring other risks. In the worst-case scenario, biogas in combination with air can form an explosive gas mixture which, in a confined space near an ignition source, can result in explosion. Biogas also contains hydrogen sulphide (H2S), a toxic gas which, in confined, poorly-ventilated spaces, can accumulate and remain unnoticed until someone enters, resulting in sometimes fatal effects.
There is also a financial impact. Losing just 1m3 of methane per hour will result in a loss of approximately £5,000 per year.
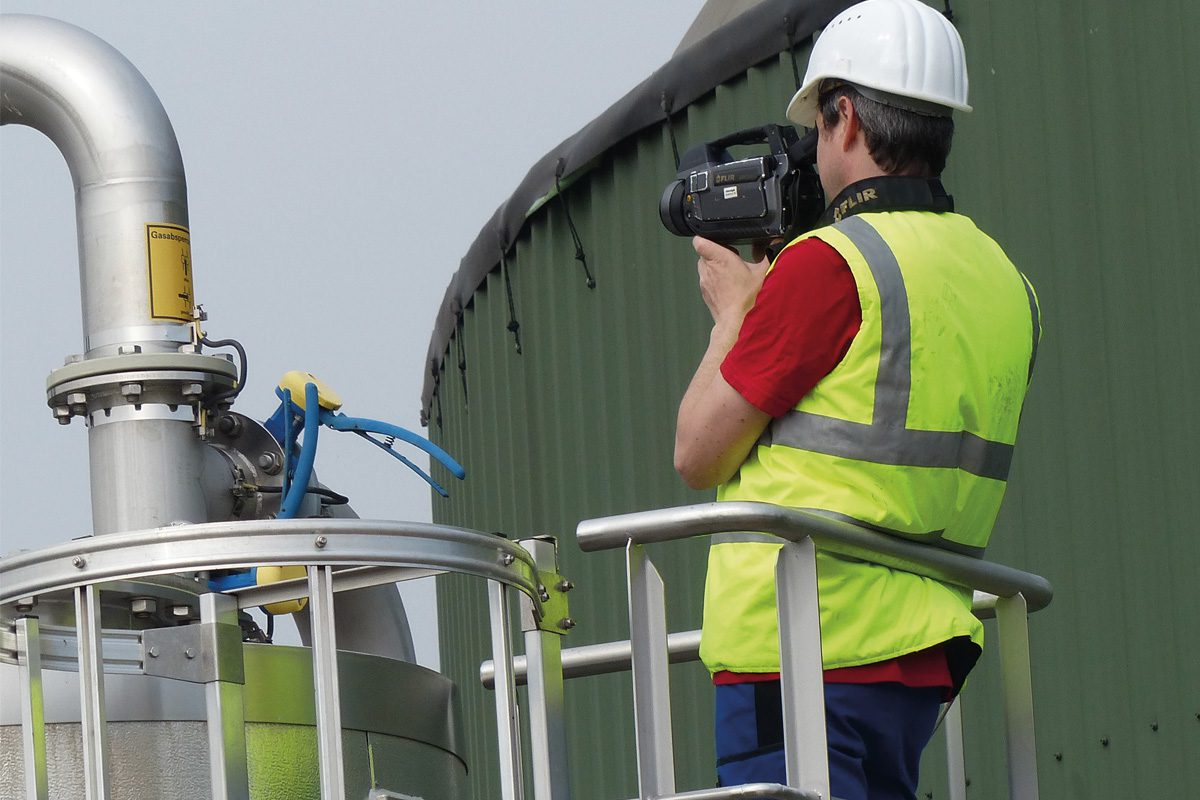
Leakage hotspots
All digesters have inherent weak points which make them susceptible to biogas leakage. Potential hotspots include: Gas membrane connections; cable grommets; flange connections; viewing windows; carbon filters; and any areas where maintenance is carried out.
Reducing your risk
Identifying a leak is a simple and affordable process which should form part of any responsible operator’s ongoing maintenance programme. The FM BioEnergy service covers a full AD plant survey with a methane-sensitive monitor and laser, as well as infra-red devices, including: Survey of all tanks, CHP, biogas upgrading equipment, roof membranes, pipes and flanges; analysis of emissions from CHP and double-membrane covers; and a report with images, videos and repair priority table.
The best times to conduct a detection survey are at the start of full operation; after significant maintenance work; if your feed-to-gas conversion is lower than expected (and the biology remains stable); and of course, if you can smell biogas. The cost of detecting a potential leak is minimal but the implications of leaving it to chance could be massive.
www.forfarmers.co.uk/fm-bioenergy