Rich Matthews, MD at water technology firm Siltbuster Process Solutions (SPS), makes the case for offsite manufacturing treatment facilities, which he says can deliver multiple benefits for water and wastewater infrastructure projects. He argues for a more “enterprise thinking” approach to capital delivery.
Given the ever more exacting compliance and efficiency pressures being felt by water firms, the 2020-2025 investment cycle could be a time for offsite manufacturing to demonstrate all the benefits it can bring.
Offsite construction allows for modular solutions to be deployed, supporting environmental resilience but requiring us to think differently about capital delivery.
The construction industry has massively advanced its skillset in offsite manufacturing in recent years – the water industry can capitalise on this, adopt key progression lessons, and take advantage of existing supply chains.
The end-goal is SMART delivery models – the deployment of standard, modular, agile, responsive treatment systems. These are geared towards providing flexibility and are aligned to offsite manufacturing.
Offsite manufacturing is also ideal for projects requiring repeatability.
These factors notwithstanding, more needs to be done to encourage decision-makers to approach solutions differently. This means adapting procurement approaches and aligning more closely with supply chains already serving other markets in this manner.
Evidence of success
If you want evidence to support the offsite approach to building treatment plants, you can find examples aplenty in the food and beverage industry. These firms are under pressure to ensure their effluent treatment plants comply with exacting regulations. Onsite space constraints are also a challenge – a pain point for the wastewater sector too – and downtime is a luxury that can seldom be afforded even if a plant has to be maintained or upgraded. Organisations rely on offsite manufacturing, deploying systems that use pre-assembled package plants and ancillaries to minimise downtime.
Risk reduction
Offsite manufacturing avoids many of the problems associated with the onsite activity involved in a treatment plant project. When manufacturing is completed offsite, it is much easier to manage the working environment in a factory, putting in effective control measures and procedures. If Design for Manufacture and Assembly (DFMA) principles are put into effect then risks are minimised. This makes provision for standardising products and subassembly design.
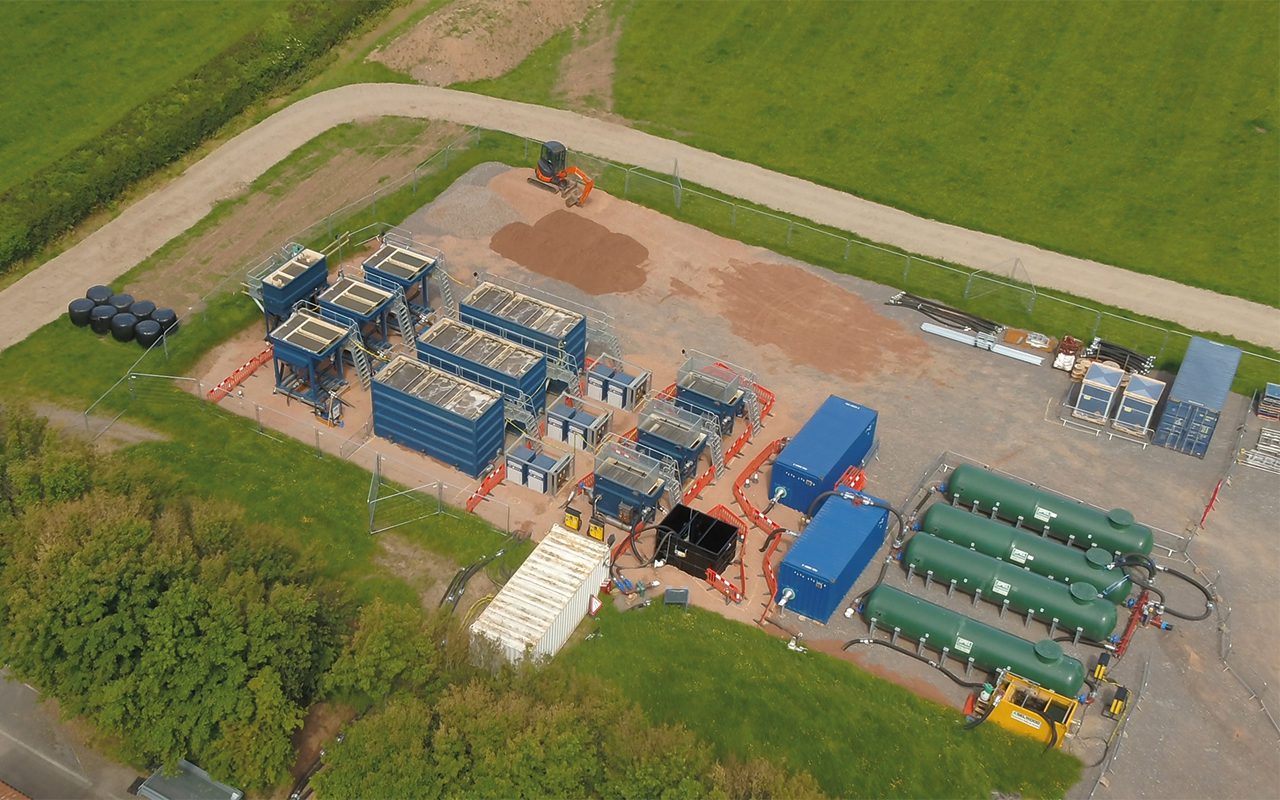
Focusing standardisation on parts allows for predictability in procurement, but seeking to standardise a complete asset can constrain the versatility of the solution and its ability to adapt to site specifics.
A key ethos in subassembly design here is working with defined battery limits and interfaces. Subassembly design also has to pay close attention to factors such as the overall size and weight of the installation, bearing in mind the site constraints.
The primary benefit of production-based delivery is that the factory-built assets can run concurrently in the construction program. Production programming means understanding lead times and supply chain interactions or dependencies and working smarter with the key links. As a result, contractual relationships need to be defined much earlier in the delivery process, using these key links to secure the knowledge and experience to fulfil the efficiency-boosting opportunities.
Bringing together this information is crucial for the management of interfaces, design parameters, and program constraints. The integration of building information modelling (BIM) into the delivery process will assist with this but must not be relied upon solely as the driver for DFMA.
When is it suitable?
Another factor to consider: Are we talking about applying offsite manufacturing to a single component, sub-assembly, or a fully packaged plant? Site-specific considerations have a bearing on the suitability of the approach, as do process requirements – flow, load, and consent. With the primary DFMA concern being to minimise site activity, there will likely be opportunities to implement some offsite manufacturing on every site.
While deployment can often require extensive logistics planning, the savings in site assembly are evident where complete treatment systems can be installed and commissioned in a matter of weeks as opposed to months.
Offsite manufacturing of effluent treatment plants also presents opportunities to support futureproof upgrades. Elements can be added to provide increased capacity or to deploy different treatment technologies as the demands of the catchment change. This futureproofing flexibility is important for an industry with such long investment horizons during which so much could change politically, environmentally, and financially within the UK.
While the benefits are many, the scale of the cultural shift needed to adopt offsite manufacturing and the DFMA ethos should not be underestimated. DFMA requires commitment from all members of the project team and at every level within a water company. Its success is dependent on a willingness to challenge and adapt a proven concept with the wider construction industry and through the momentum gained of minimising site activities and associated risk. This will deliver a more responsive investment program without compromising compliance.
The fact that offsite manufacturing fundamentally delivers so many benefits needed right now surely means its moment has come.