A technology for measuring VOC emissions in real time – using optical fibres – could play a role in improving safety in chemical plants and other industrial facilities
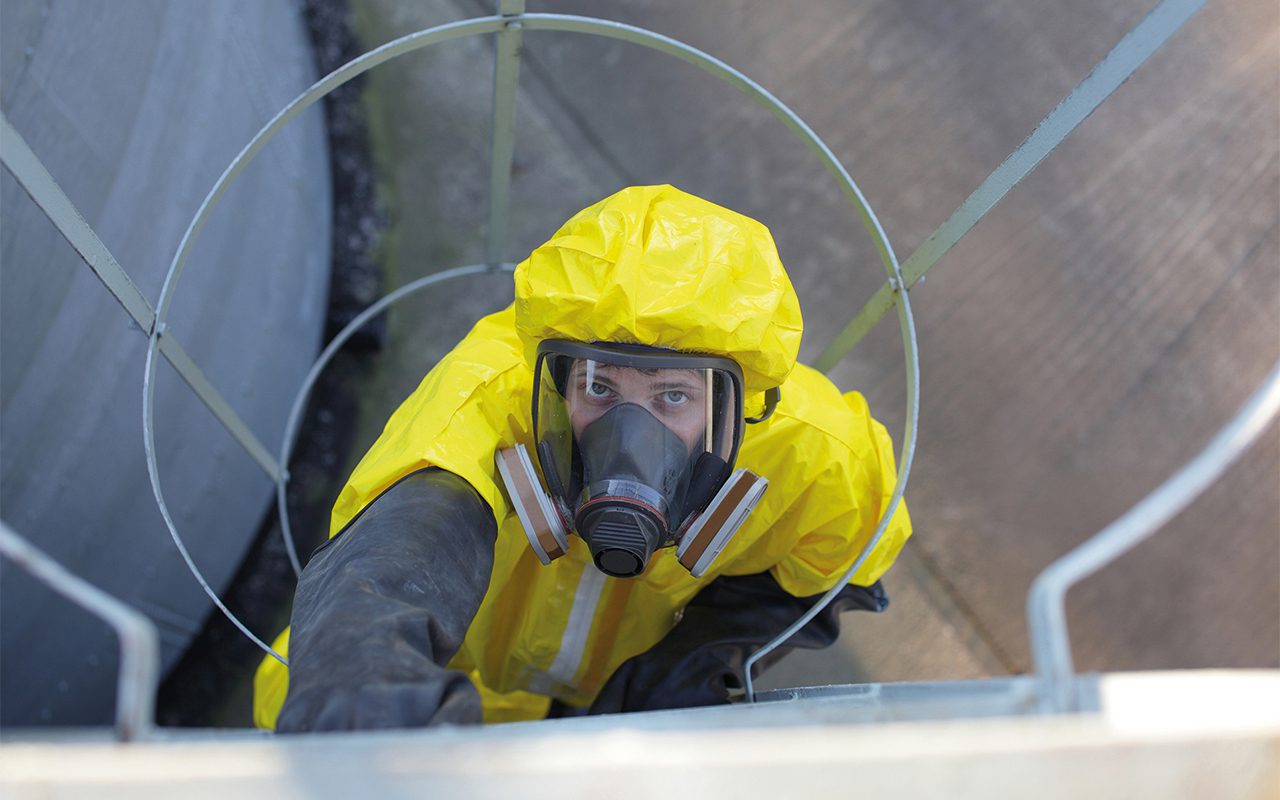
No technology currently exists to perform a real-time, automatic check in fuel tanks for Volatile Organic Compounds (VOCs) – chemicals that evaporate quickly at room temperature. Technologies that are generally used to monitor these chemicals currently use electronic sensors that need to be heated past 150 degrees.
However, scientists from the University of Navarra in Pamplona, Spain have teamed up with the EU photonics innovation hub ACTPHAST 4R to develop a demonstrator for what is described as a breakthrough optical sensing technology capable of detecting a number of chemical vapours that are considered toxic or explosive.
Emptying giant tanks filled with alcohols, ketones, aldehydes, chloroform, and dichloromethane, chemical plant staff have to ensure no traces of vapour or liquid remain.
Having to climb inside these giant tanks, workers are under constant threat of causing an explosion from friction or static electricity.
The new detector uses optical fibres to monitor air quality, with no electrical or flammable components as part of the device.
Chemical plant-related fatalities numbered 681 in 2017, in terms of what was reported in the media. High profile plant explosions in the past year included incidents in Port Neches, Texas (November 2019), the La Canonja explosion (January 2020), and the surfactant unit explosion of Tarapur, Maharashtra (April 2020).
State of development
With a demonstrator ready, the researchers say it will require further testing before being commercially available.
The lead researcher on the project, Dr César Elosúa Aguado, said: “An air sensor using optical fibres for the purpose of VOC detection is a major scientific breakthrough concept.
He said the support received from ACTPHAST 4R had been “crucial to bridging the gap between the ‘valley of death’ in innovation and accelerated TRL advancement.”
If the demonstrator is successful, the researchers will look at commercialisation options such as licensing or starting a spin-out company from the university.
Today’s electronic sensors use metallic oxides that are capable of sensing toxic chemicals but are not safe in the shipping of chemical solvents. Semiconductor metallic oxides can be unsafe and slow to use in dangerous environments.
Dr Elosúa Aguado said the technology “allows instantaneous, real-time monitoring” and avoids “having to wait days for samples to come back from a laboratory”.
How it works
The new sensor looks at the interaction between the cladding modes and the sensitive coating – producing a new signal when the toxic substance is present.
“We still use metallic oxides but our system looks at the refractive index of the sensing material, rather than changes in electrical conductivity.
“The sensor surface is coated with zinc oxide oxides as a sensing material that reacts when the harmful material is present.”
“Cladding modes are a part of the optical signal that is “forced” to travel by a Bragg reflector, not through the core but around the cladding, enabling an interaction with the surrounding media,” he said.
The sensor is therefore specifically ‘tuned’ to a toxic substance, meaning the only molecules that are captured along the sensor are the dangerous gasses under surveillance.
“The reaction mechanism between the metallic oxide and the VOC is a reversible redox chemical reaction. The selectivity of these materials is low, so they react to a wide range of solvents with different sensitivities. Therefore, sensors with different responses combine to form a specific pattern for each VOC.”
“The sensor response will be used to train an AI system capable of identifying the different VOC samples,” he said.